Strength Testing of Definitive Transtibial Prosthetic Sockets Made Using 3D-Printing Technology
Jpo Journal of Prosthetics and Orthotics(2020)
摘要
Introduction: Unlike endoskeletal connectors and prosthetic feet, prosthetic sockets are not subjected to structural strength testing using internationally recognized test standards, such as International Organization for Standardization (ISO) 10328. Definitive prosthetic sockets fabricated in the traditionalmanner have been shown to be inconsistent in the ability to withstand the loads applied by these standards. Persistent concerns regarding the strength and durability of 3D-printed prosthetic sockets are a barrier to clinical adoption of 3D-printing technologies in prosthetic socket fabrication. To develop a robust prosthetic socket design based on 3D-printing technology, an iterative development process was used with integral validation testing using the ISO 10328 loading conditions performed independently by two testing centers. Materials and Methods: Twenty-four 3D-printed transtibial prosthetic sockets were tested using ISO 10328 loading conditions designed to represent the greatest atypical elevated loads a 125-kg user would be expected to place on their prosthesis without failure (ultimate strength test at the P6 load level). Several design iterations and variations were tested. One socket of a design that withstood the ultimate strength loading was reprinted and subjected to cyclic testing, up to 3 million cycles. All tests were conducted under the forefoot loading condition (Condition II of the ISO 10328 standard), which generates greater moments at the distal end of the socket than the heel loading condition. Results: Early socket designs were unable to withstand the ISO 10328 ultimate strength test to the P6 load level. Successive design improvements increased the strength until a robust final design was achieved. Variations of that final design for different suspension types and a different limb model demonstrated consistent performance. The final design was significantly stronger than the initial design (P = 1.35 x 10(-7)). The socket that was tested for durability completed the 3 million loading cycles at the P6 load level without damage and withstood the subsequent static proof loads. Conclusions: An iterative design process with integral structural testing can result in strong, durable prosthetic sockets made using 3D-printing technology that may be robust to variations in limb size/shape and suspension type.
更多查看译文
关键词
prosthesis, socket, strength, ISO 10328, 3D-printing
AI 理解论文
溯源树
样例
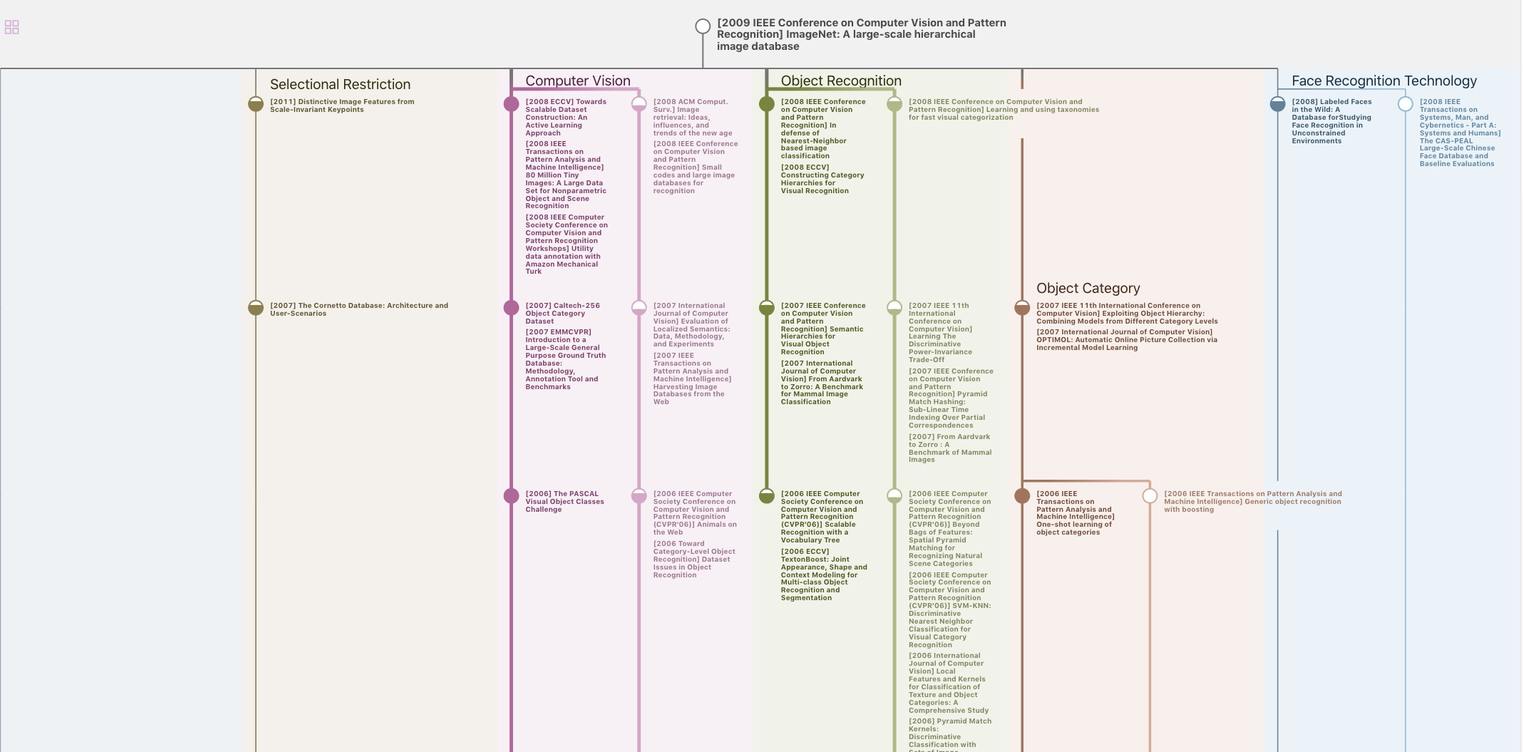
生成溯源树,研究论文发展脉络
Chat Paper
正在生成论文摘要