Effect of process parameters on the microstructure, tensile strength and productivity of 316 L parts produced by laser powder bed fusion
Materials Characterization(2020)
摘要
The influence of process parameters during laser-powder bed fusion on the microstructure, tensile strength and build time of 316L parts is studied. By increasing both, scan speed and hatch distance, an improved productivity while maintaining acceptable properties were achieved. The samples were evaluated using volumetric energy density. The microstructure characterization showed that all produced samples had elongated grains aligned with the building direction independent on energy density that was used, whereas the grain size was strongly affected by the different energy densities. A high energy density resulted in larger grains with a very strong 〈101〉 crystallographic orientation while the lower energy generated small grains with a random crystallographic orientation. This indicates how both, crystallographic orientation and grain size, can be tailored by altering the energy density. Even if a large variance in microstructure was observed, the tensile test results only showed about 5% difference in yield strength between standard process parameters and the samples produced with the lowest energy density but with a 20% faster build time. Due to the decreased energy density, the amount of defects was increased which had a negative effect on the elongation. The samples produced with the lowest energy density had 32% elongation compared to 45% for the samples produced with standard process parameters. This study clearly indicates that the build time can be improved while maintaining good mechanical properties by adjusting the process parameters.
更多查看译文
关键词
Laser powder bed fusion,Additive manufacturing,316L,Process parameters,Mechanical properties,Microstructure
AI 理解论文
溯源树
样例
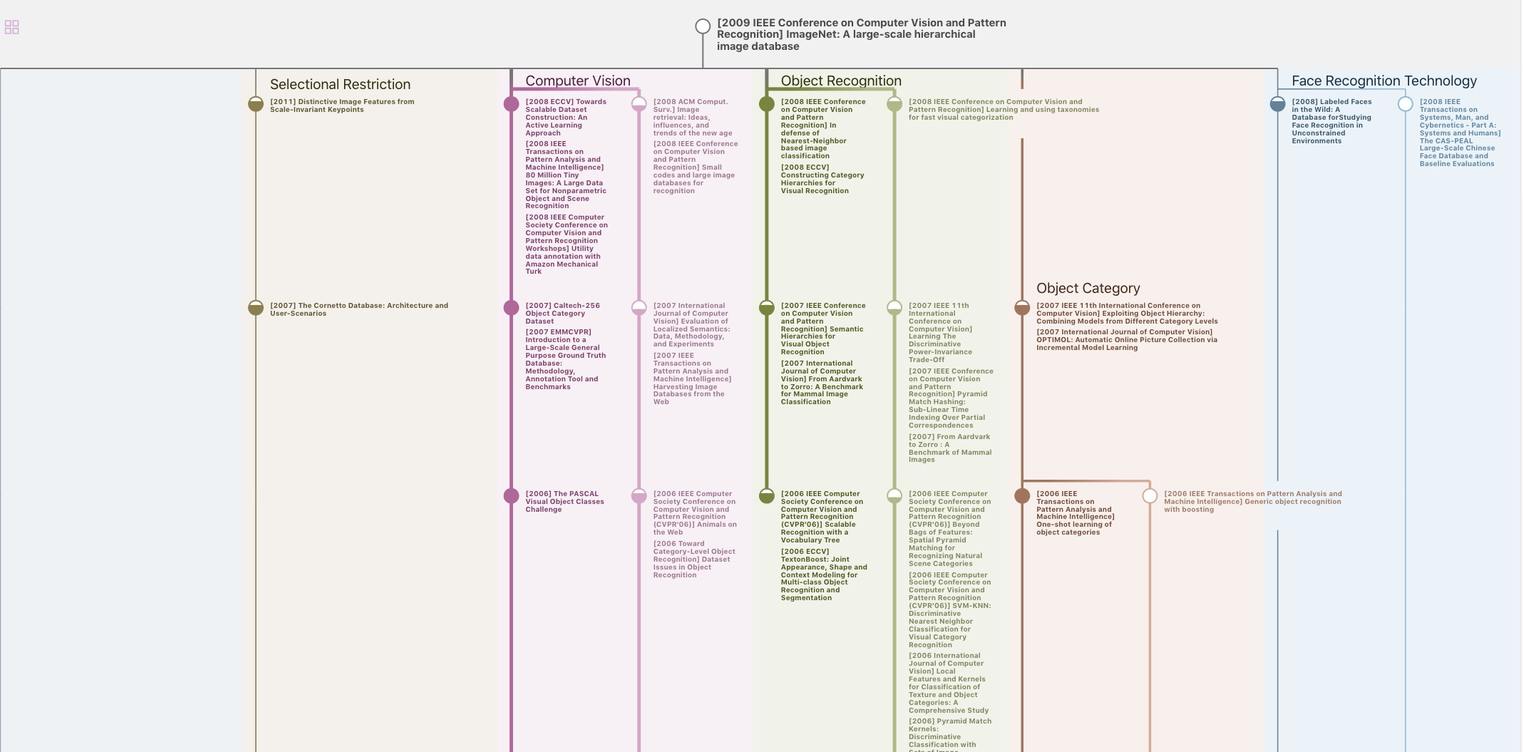
生成溯源树,研究论文发展脉络
Chat Paper
正在生成论文摘要