Derivation of knockdown factors for grid-stiffened cylinders considering various shell thickness ratios
AIRCRAFT ENGINEERING AND AEROSPACE TECHNOLOGY(2019)
摘要
Purpose The purpose of this paper is to derive knockdown factor functions in terms of a shell thickness ratio (i.e. the ratio of radius to thickness) for conventional orthogrid and hybrid-grid stiffened cylinders for the lightweight design of space launch vehicles. Design/methodology/approach The shell knockdown factors of grid-stiffened cylinders under axial compressive loads are derived numerically considering various shell thickness ratios. Two grid systems using stiffeners - conventional orthogrid and hybrid-grid systems - are used for the grid-stiffened cylinders. The hybrid-grid stiffened cylinder uses major and minor stiffeners having two different cross-sectional areas. For modeling grid-stiffened cylinders with various thickness ratios, the effective thickness (t(eff)) of the cylinders is kept constant, and the radius of the cylinder is varied. Thickness ratios of 100, 192 and 300 are considered for the orthogrid stiffened cylinder, and 100, 160, 200 and 300 for the hybrid-grid stiffened cylinder. Postbuckling analyses of grid-stiffened cylinders are conducted using a commercial nonlinear finite element analysis code, ABAQUS, to derive the shell knockdown factor. The single perturbation load approach is applied to represent the geometrical initial imperfection of a cylinder. Knockdown factors are derived for both the conventional orthogrid and hybrid-grid stiffened cylinders for different shell thickness ratios. Knockdown factor functions in terms of shell thickness ratio are obtained by curve fitting with the derived shell knockdown factors for the two grid-stiffened cylinders. Findings For the two grid-stiffened cylinders, the derived shell knockdown factors are all higher than the previous NASA's shell knockdown factors for various shell thickness ratios, ranging from 100 to 400. Therefore, the shell knockdown factors derived in this study may facilitate in the development of lightweight structures of space launch vehicles from the aspect of buckling design. For different shell thickness ratios of up to 500, the knockdown factor of the hybrid-grid stiffened cylinder is higher than that of the conventional orthogrid stiffened cylinder. Therefore, it is concluded that the hybrid-grid stiffened cylinder is more efficient than the conventional orthogrid-stiffened cylinder from the perspective of buckling design. Practical implications - The obtained knockdown factor functions may provide the design criteria for lightweight cylindrical structures of space launch vehicles. Originality/value Derivation of shell knockdown factors of hybrid-grid stiffened cylinders considering various shell thickness ratios is attempted for the first time in this study.
更多查看译文
关键词
Shell thickness ratio,Buckling knockdown factor,Orthogrid stiffened cylinder,Hybrid-grid stiffened cylinder,Postbuckling analysis
AI 理解论文
溯源树
样例
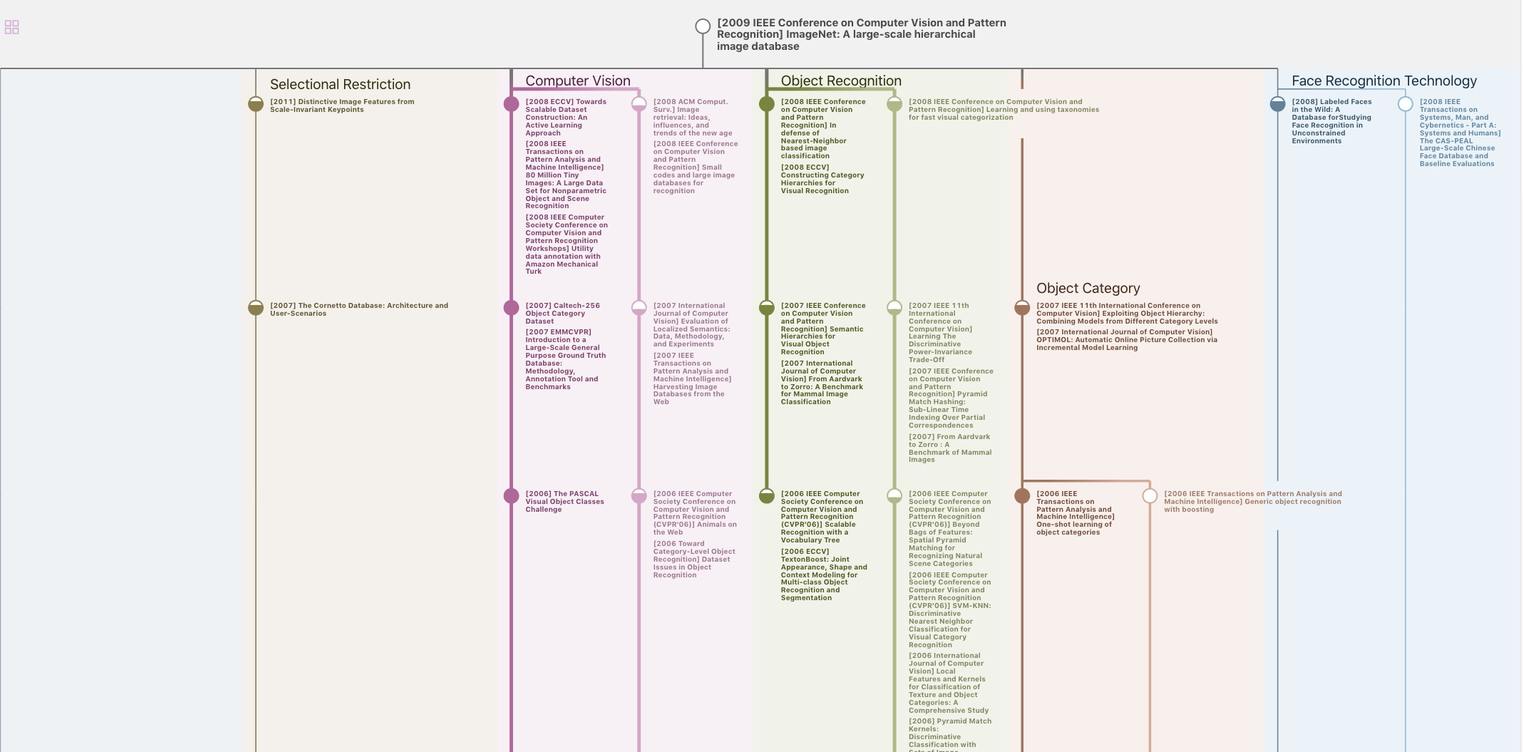
生成溯源树,研究论文发展脉络
Chat Paper
正在生成论文摘要