Boundary Slope Control in Topology Optimization for Additive Manufacturing: for Self-support and Surface Roughness
JOURNAL OF MANUFACTURING SCIENCE AND ENGINEERING-TRANSACTIONS OF THE ASME(2019)
摘要
This paper studies how to control boundary slope of optimized parts in density-based topology optimization for additive manufacturing (AM). Boundary slope of a part affects the amount of support structure required during its fabrication by additive processes. Boundary slope also has a direct relation with the resulting surface roughness from the AM processes, which in turn affects the heat transfer efficiency. By constraining the minimal boundary slope, support structures can be eliminated or reduced for AM, and thus, material and post-processing costs are reduced; by constraining the maximal boundary slope, high-surface roughness can be attained, and thus, the heat transfer efficiency is increased. In this paper, the boundary slope is controlled through a constraint between the density gradient and the given build direction. This allows us to explicitly control the boundary slope through density gradient in the density-based topology optimization approach. We control the boundary slope through two single global constraints. An adaptive scheme is also proposed to select the thresholds of these two boundary slope constraints. Numerical examples of linear elastic problem, heat conduction problem, and thermoelastic problems demonstrate the effectiveness and efficiency of the proposed formulation in controlling boundary slopes for additive manufacturing. Experimental results from metal 3D printed parts confirm that our boundary slope-based formulation is effective for controlling part self-support during printing and for affecting surface roughness of the printed parts.
更多查看译文
AI 理解论文
溯源树
样例
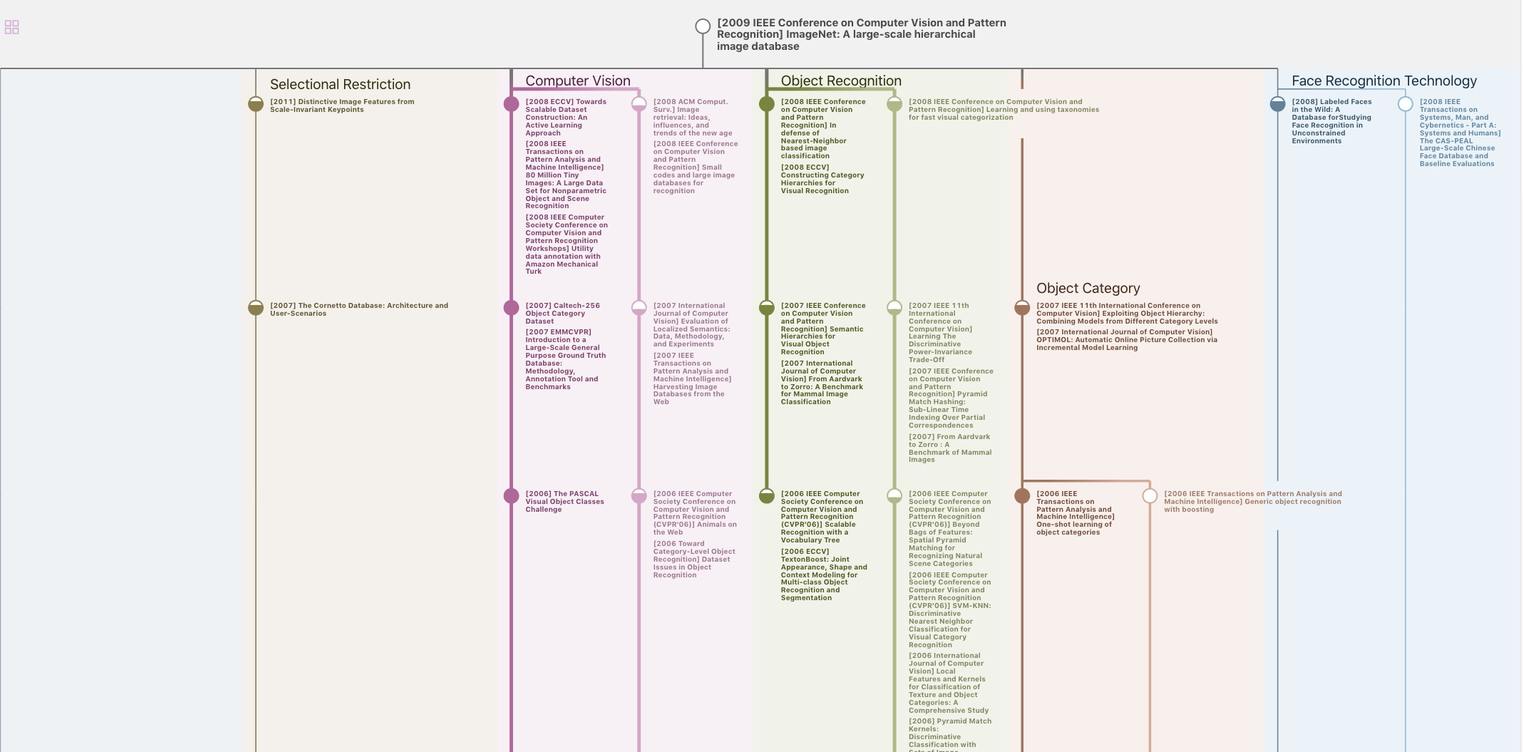
生成溯源树,研究论文发展脉络
Chat Paper
正在生成论文摘要