Control of a Hyper-Redundant Robot for Quality Inspection in Additive Manufacturing for Construction
2019 2nd IEEE International Conference on Soft Robotics (RoboSoft)(2019)
摘要
Additive manufacturing is an automated process for producing layer-by-layer material deposition. Recently this technology has been introduced in the industrial construction in order to print houses or smaller piece structures for on-site assembly, with complex geometry. In Additive manufacturing processes, the material deposition step is generally followed by a printing quality inspection step. However, the geometry of printed structures with minimal surfaces is sometimes complex, where rigid structure robots cannot reach certain zones to scan their surfaces. In this paper, a continuum-hyper-redundant manipulator equipped with a camera is attached to the end-effector of a mobile-manipulator robot for the quality inspection process. Indeed, Continuum manipulators can bend along structures with complex geometry; and this inherent flexibility makes them suitable for navigation and operation in congested environments. The number of controlled actuators being greater than the dimension of task space, this work is summarized in a trajectory tracking of hyper-redundant robots. This issue lies in the resolution of strongly nonlinear equations with a realtime computation. Thus, a hybrid methodology which combines the advantages of quantitative and qualitative approaches is used for modeling and resolution of the hyper-redundant robot kinematics. A kinematic controller was designed and a set of experiments was carried out to evaluate the level of efficiency of the proposed approach.
更多查看译文
关键词
Manipulators,Kinematics,Three-dimensional printing,Mathematical model,Inspection,Buildings
AI 理解论文
溯源树
样例
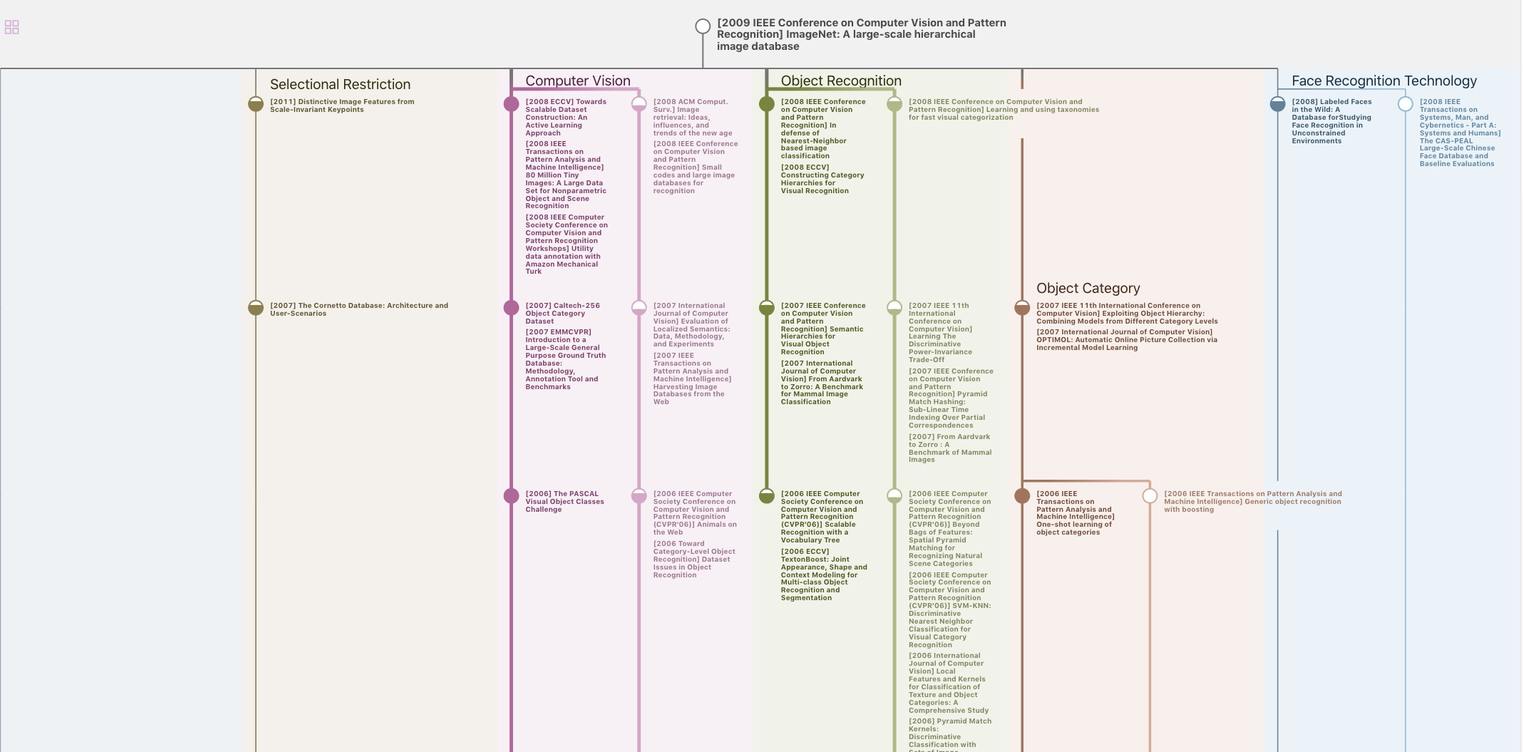
生成溯源树,研究论文发展脉络
Chat Paper
正在生成论文摘要