Numerical modeling of the effects of FRP thickness and stacking sequence on energy absorption of metal–FRP square tubes
Composite Structures(2016)
摘要
Hybrid metal-composite tubes have the potential to provide cost-effective, energy-absorbing structures for automotive applications. To provide guidance to enable the optimum design of these structures, square hybrid tubes consisting of S2 glass/epoxy composites and 304 stainless steel were modeled numerically. The models were validated with experimental results obtained from quasi-static crushing tests conducted on different combinations of two design variables: stacking sequence and thickness of the FRP section. The effects of the design variables on the energy absorption and failure modes of the hybrid tubes were explained using the models. Subsequently, the results from the numerical models were used to obtain optimum crashworthiness functions. The load efficiency factor (the ratio of mean crushing load to maximum load) and ratio between the difference of mean crushing load of hybrid and metal tube and thickness of the FRP section were introduced as the functions. To connect the variables and the objective functions, back-propagation artificial neural networks (ANN) were used. The non-dominated sorting genetic algorithm-II (NSGAII) was applied to the constructed ANNs to obtain optimal results in the form of Pareto Frontier solutions. The result is an efficient methodology to obtain the best combination of design variables for hybrid metal-composite tubes for crashworthiness applications.
更多查看译文
关键词
Axial crushing performance,Metal-composite square hybrid tubes,Neural networks,Multi-objective optimization
AI 理解论文
溯源树
样例
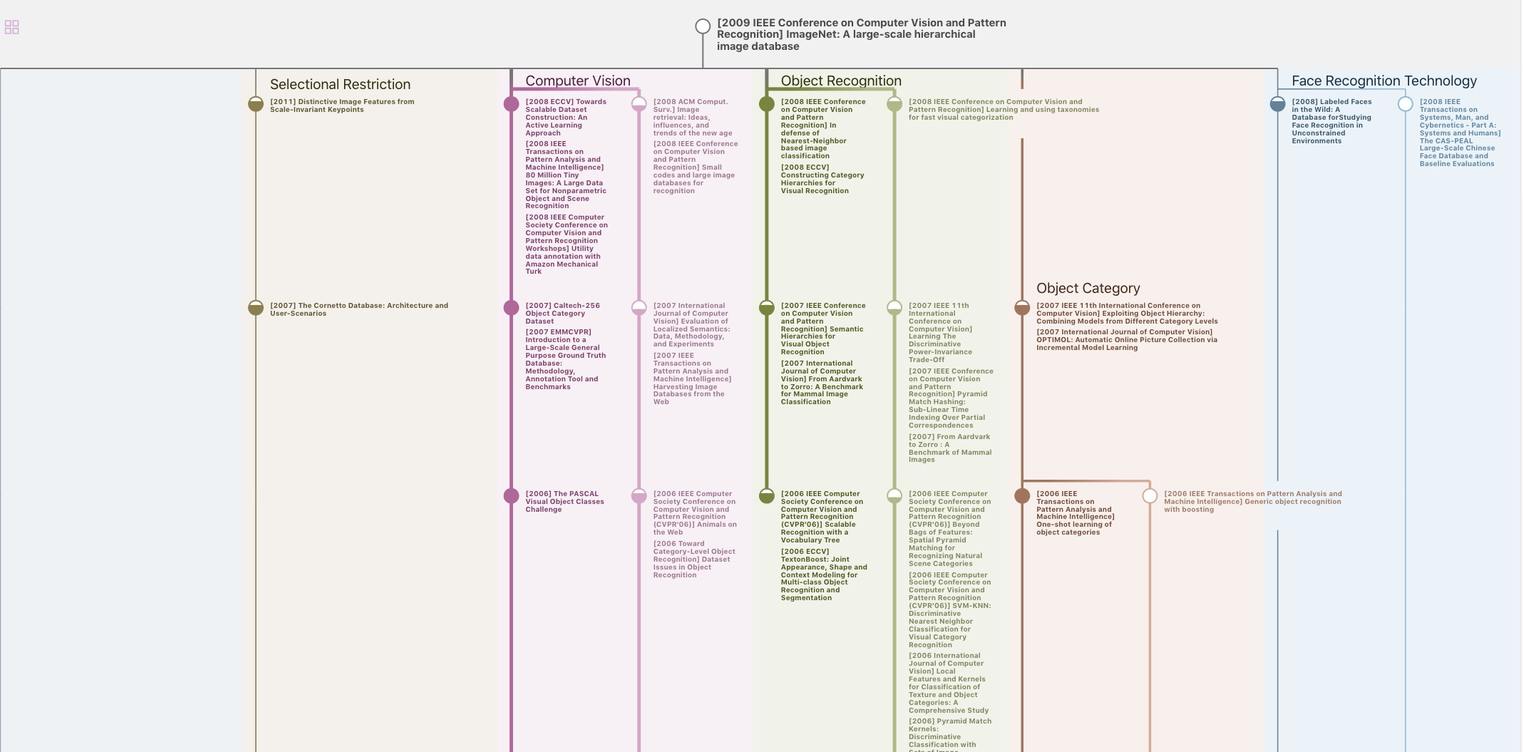
生成溯源树,研究论文发展脉络
Chat Paper
正在生成论文摘要