Sculptured Surfaces Subdivision From 3d Cloud Of Points And Association Of Optimum Ball Cutters
8TH CIRP CONFERENCE ON HIGH PERFORMANCE CUTTING (HPC 2018)(2018)
摘要
Parts with sculptured surfaces used in molds industry, etc. are machined on multi-axis CNC milling machines. Their final shapes are obtained in three stages: roughing, semi-finishing and finishing. For all stages it is indispensable to determine largest cutters and thus most efficient cutters able to machine these surfaces without gouging and collision. Nowadays, Reverse Engineering is used to reproduce objects where their CAD models are unavailable. In this process, the object is digitized to retrieve a set of dense clouds of points. In consequence, there is no relationship between points which makes the determination of optimal cutters more difficult. In this paper, for finishing sculptured surfaces on 3-axis CNC milling machines directly from 3D cloud of points, an approach is proposed to partition the cloud of points into distinct regions from estimated points local shapes (concave, convex, plane, concave developable, convex developable, saddle) and then determines the optimal ball cutter for each region avoiding interferences. For this, Delaunay triangulation is used to establish geometric relationships between points. This approach reduces the product development cycle by associating an optimal cutter to each region which decreases machining times and costs and increases productivity. (C) 2018 The Authors. Published by Elsevier Ltd.
更多查看译文
关键词
sculptured surface, cloud of points, interference, ball cutter, delaunay triangulation
AI 理解论文
溯源树
样例
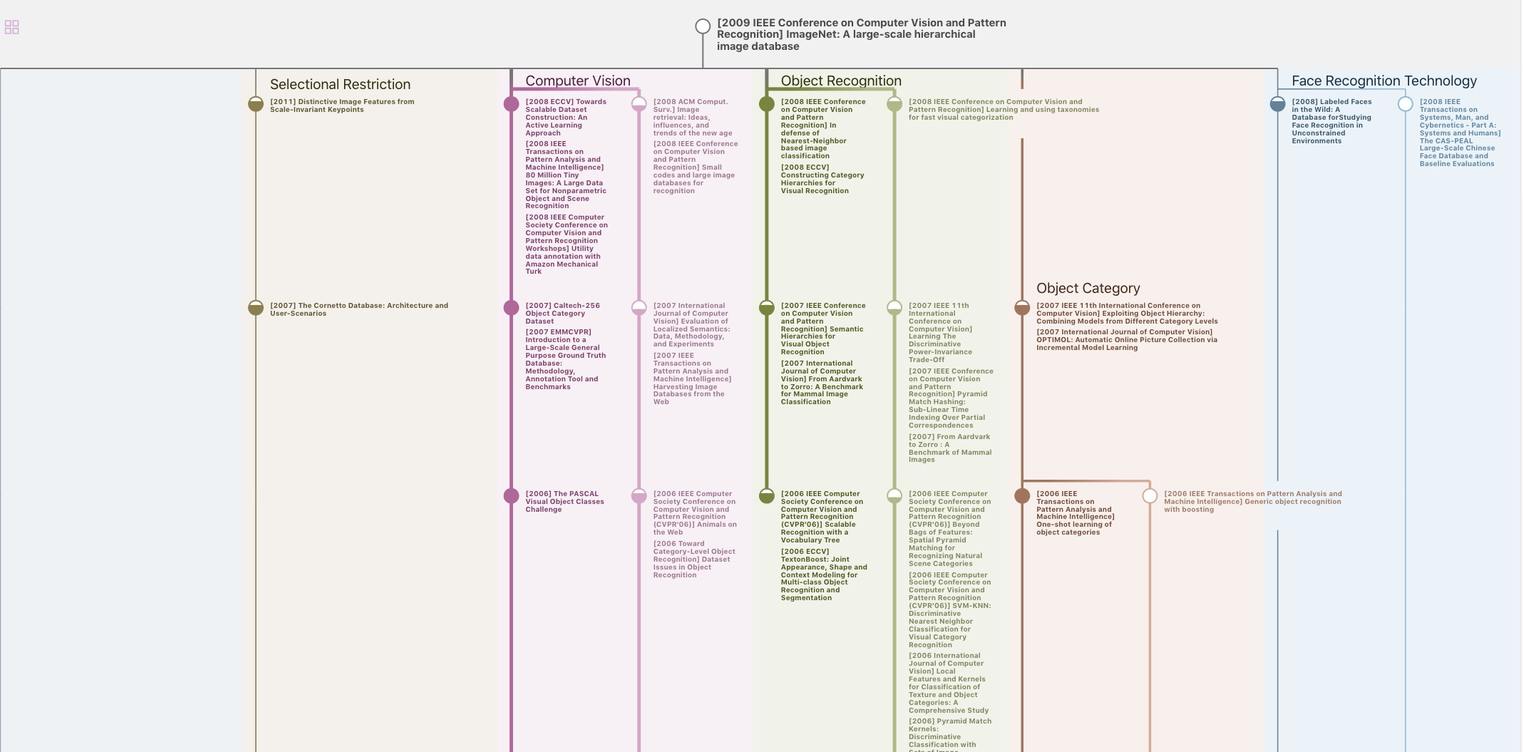
生成溯源树,研究论文发展脉络
Chat Paper
正在生成论文摘要