An Update On The Impact Of Forging Residual Stress In Airframe Component Design
MATERIALS PERFORMANCE AND CHARACTERIZATION(2018)
摘要
In a recently concluded study, the effects of forging process-induced bulk residual stresses on fatigue life were evaluated at both the coupon and large component level. During this program, it was demonstrated that the extraction of confounding residual stress effects from material property data (especially fatigue crack growth rate data), coupled with the explicit inclusion of forging residual stresses in subsequent fatigue analyses, resulted in a significant improvement in the fidelity of those analyses. In the first phase of the program, coupon-level tests were carefully designed, executed, and analyzed, and it was shown that the newly developed methods resulted in analysis versus test life correlation ratios that were either within the United States Air Force (USAF) required scatter factor of 2, or were conservative. This is in contrast to a much broader scatter band (5x) for calculations made using traditional (non-residual-stress-informed) methods. The explicit residual stress method was incorporated into an integrated structural design/analysis tool suite that allows zoning of parts into residual stress-specific regions, automated generation of location-specific fatigue spectra, automated execution of fatigue crack initiation, fatigue crack growth, and residual strength analyses, and automated generation of fatigue-based design, allowable stresses, and margins of safety. In the second phase of the program, the residual stress design procedure was applied (to the furthest extent possible) to the design and manufacture of a large, fighter aircraft bulkhead. The objective of this phase of the program was to demonstrate, by way of two large component fatigue tests, that the technology would scale to the structural level, and that its use would result in components that are either lighter or more durable (or both) than their traditionally designed counterparts. In this article, we compare and contrast the traditional versus residual stress-informed design procedures, and we describe in detail the resulting baseline and "optimized" test articles. A full description of the fatigue tests, along with comparisons between detailed fatigue calculations and test findings, are given.
更多查看译文
关键词
residual stress, aluminum forgings, integrated computational materials engineering, integrated computational structures engineering, fatigue crack initiation, fatigue crack growth
AI 理解论文
溯源树
样例
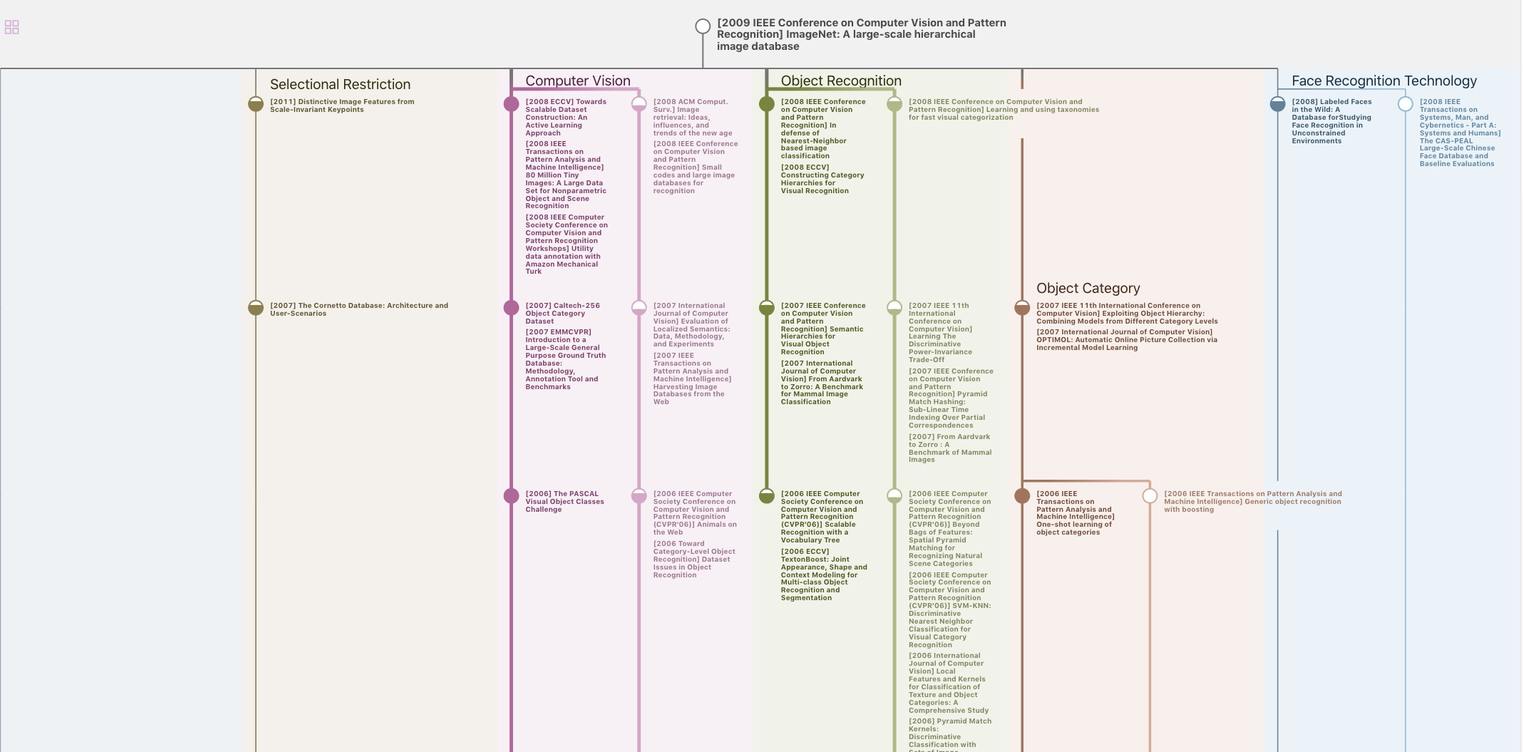
生成溯源树,研究论文发展脉络
Chat Paper
正在生成论文摘要