A Microforce-Sensing Mobile Microrobot for Automated Micromanipulation Tasks
IEEE Transactions on Automation Science and Engineering(2019)
摘要
This paper presents a microforce-sensing mobile microrobot (
$\mu $
FSMM) for use in automated micromanipulation tasks. The design consists of a planar vision-based microforce sensor end-effector, while the microrobot body is made of chemically etched nickel that is driven by an exterior magnetic field. With a known stiffness, the manipulation forces can be determined from observing the deformation of the end-effector through a camera attached to an optical microscope. After analyzing and calibrating the stiffness of a micromachined prototype, the mobility and
in situ
force-sensing capabilities are verified through real-time, closed loop, force controlled manipulation tests with automated path planning and navigation. The calibrated stiffness of the microforce sensor end-effectors fabricated is on the order of 10
−3
N/m. The online (real time) force-sensing resolution is approximately
$1.5~\mu \text{N}$
. The sensing range is 0–20
$\mu \text{N}$
along the two planar directions. In automated micromanipulation experiments with a microcomponent, the
$\mu $
FSMM utilizes real-time force control to apply a prescribed force of
$6~\mu \text{N}$
to a desired location on a fixed microobject. Similarly, in another automated micromanipulation experiment, the
$\mu $
FSMM demonstrates the use of real-time force control to limit the manipulation forces experienced by the microobject to remain below a threshold of 12
$\mu \text{N}$
.
Note to Practitioners
—This paper was motivated by recent interest single-cell biological micromanipulation tasks that seek to understand the role of environmental forces on the mechanics of cell development (mechanobiology) and the biological mechanisms that control such behavior (mechanotransduction). In addition, tissue engineering applications require the safe micromanipulation of single cells to desired locations in the workspace for growing tissue scaffolds. The
$\mu $
FSMM presented here can be easily inserted into existing biological testbeds to use for these aforementioned applications. The designed magnetic coil system is compatible with standard inverted optical microscopes, while a digital camera for real-time image processing is already standard in these testbeds. The developed software interface can be used to prescribe automated microforce controlled manipulations of single cells and tissues in the workspace to carry out these aforementioned tasks. This paper is also suitable for carrying out general automated micromanipulation and microassembly tasks with advanced manufacturing applications.
更多查看译文
关键词
Force,Robot sensing systems,Task analysis,Real-time systems,Biology,Microscopy
AI 理解论文
溯源树
样例
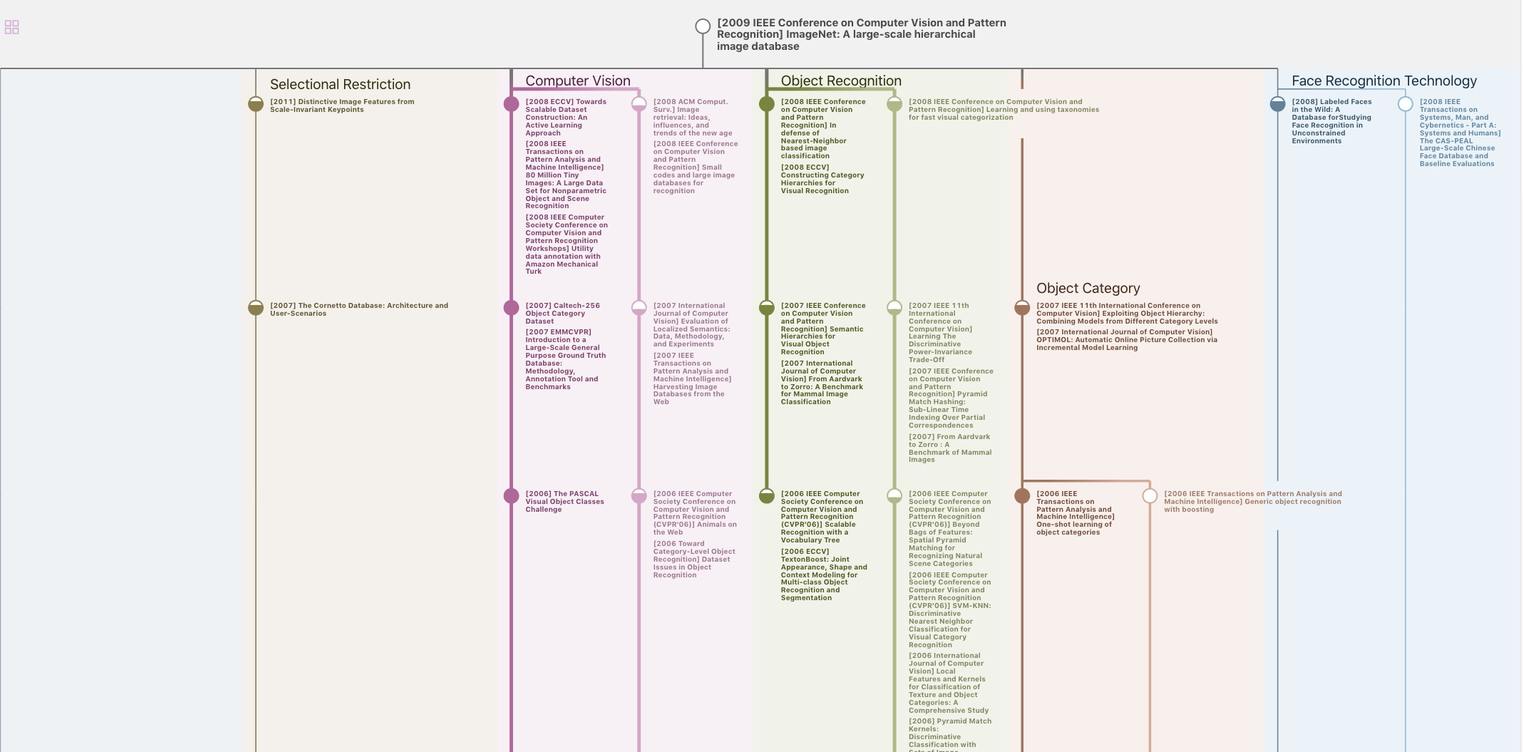
生成溯源树,研究论文发展脉络
Chat Paper
正在生成论文摘要