Impact Experiment Analysis Of Mems Ultra-High G Piezoresistive Shock Accelerometer
2018 IEEE MICRO ELECTRO MECHANICAL SYSTEMS (MEMS)(2018)
摘要
A novel ultra-high g shock micro accelerometer with four self-supporting piezoresistive micro beams was proposed to simultaneously enhance the sensor performance of sensitivity and frequency response. The finite element method (FEM) simulations indicated that the pure axial deformations could occur on self-supporting piezoresistive micro beams via optimizing structure dimensions. And the average stress distribution in piezoresistive beams was 81.5 MPa, the natural frequency of sensor was about 505.00 kHz. To verify the sensitivity and natural frequency of fabricated shock accelerometer, impact tests were carried out using Hopkinson pressure bar under impact loads of 100,000 g. The results were obtained in the form of response curves of a shock signal. Then, the average sensitivity was calculated as 1.586 mu V/g/3V, and the natural frequency was obtained as 445 kHz by fast Fourier transform. The experimental results agreed well with the FEM simulations except for a slight mismatch in natural frequency which was probably resulted from the errors of device fabrication and package processes. The experiment results reliably demonstrate that the proposed shock accelerometer, with high natural frequency and high sensitivity, is capable of measuring ultra-high g loading shock.
更多查看译文
关键词
piezoresistive beams,fabricated shock accelerometer,shock signal,FEM simulations,MEMS ultra-high G piezoresistive shock accelerometer,piezoresistive microbeams,sensor performance,frequency response,finite element method simulations,pure axial deformations,ultrahigh g shock microaccelerometer,stress distribution
AI 理解论文
溯源树
样例
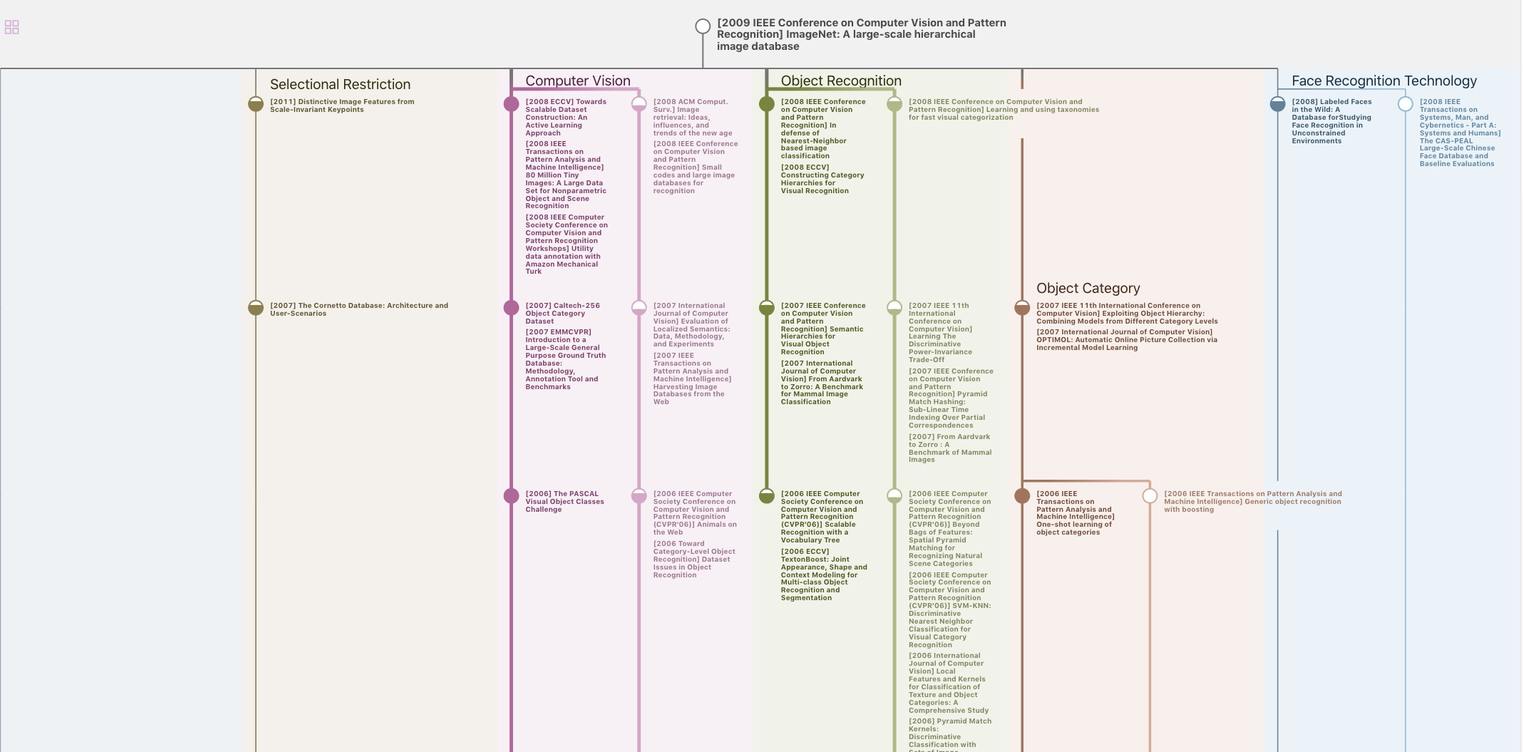
生成溯源树,研究论文发展脉络
Chat Paper
正在生成论文摘要