An Investigation into the Interrelationship between Aircraft Systems and Final Assembly Process Design
Procedia CIRP(2017)
摘要
Modern aircraft are more integrated with advanced systems functionalities, which result in ever-increasing aircraft complexity, further development difficulties and development delays. These system complexities are mostly in the form of system interactions that make it difficult to understand the overall system characteristics. At the early stages of final assembly line (FAL) design, one of the most important objectives is to arrange the installation and test tasks from components to sub-systems and systems in the proper sequence to meet the designed functions and prevent hazards from the integration process. Improper sequencing of the final assembly process will cause rework, time delays, cost and potential safety risk in development. In the field of final assembly line design, previous research has mostly focused on assembly line balancing or supply chain design based on structural parts assembly. However, these approaches do not consider the early final assembly line definition or test allocation for system functions. In this paper, the research proposes a method based on a systems engineering view and integrated computer aided design (CAD) to help better understand system interactions and generate viable final assembly process sequencing. This research aims to develop a concept of unified master data for final assembly design, which contains 3D geometrical CAD, system functions and interaction characteristics. The paper will present the methodology framework, key concepts and associated industrial software packages for implementation. The paper concludes with further discussion of an initial case study.
更多查看译文
关键词
Aircraft Systems Integration,Final Assembly Process Design,Integrated CAD
AI 理解论文
溯源树
样例
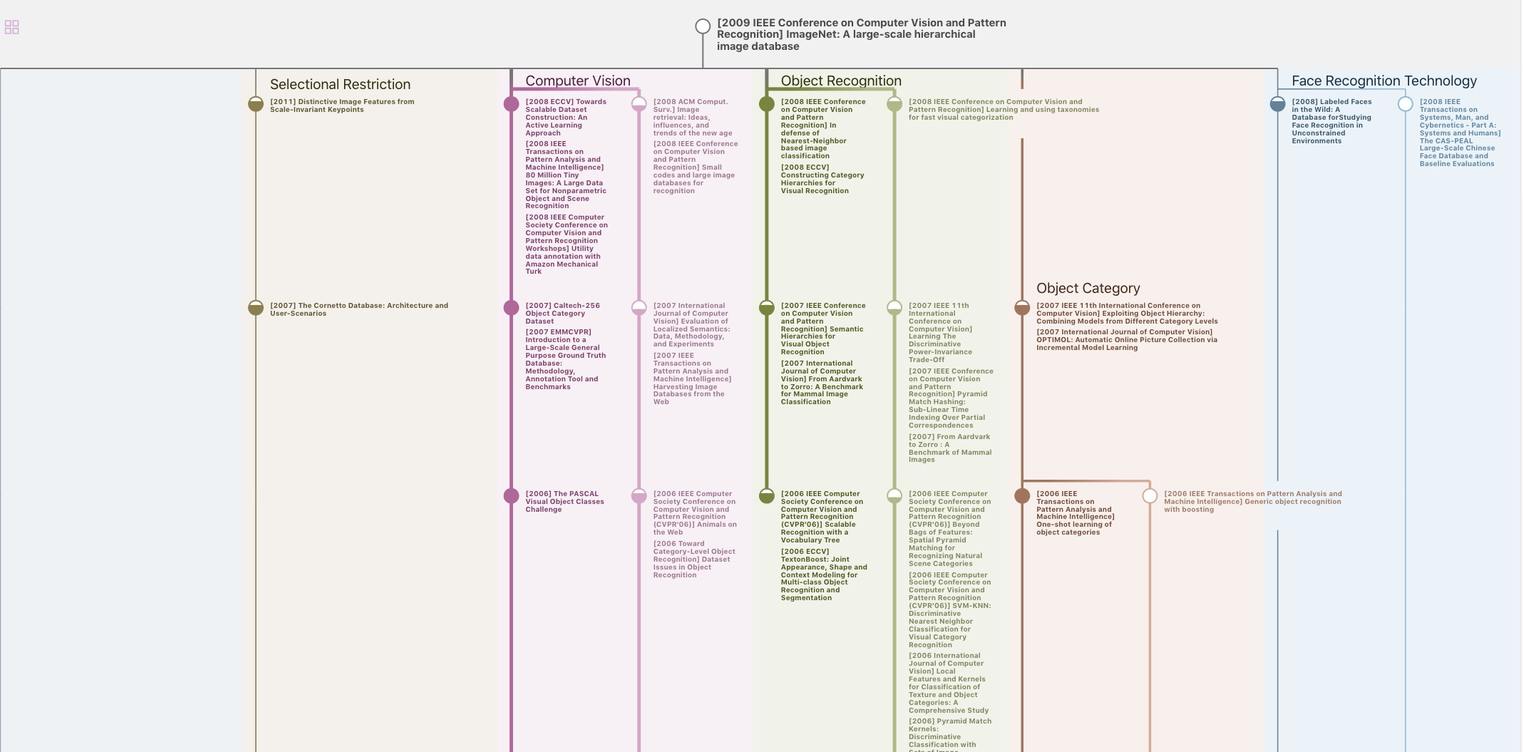
生成溯源树,研究论文发展脉络
Chat Paper
正在生成论文摘要