Comparative assessment of the fire structural performance of carbon-epoxy composite and aluminium alloy used in aerospace structures
Materials & Design(2016)
摘要
An experimental investigation is presented comparing the fire structural survivability of two important types of aerospace materials: carbon fibre-epoxy composite and aluminium alloy. The thermal response, softening rate, deformation behaviour and structural survivability for the two materials are compared when exposed to a thermal flux. Simulated fire structural tests are performed on quasi-isotropic carbon-epoxy composite and aluminium alloy (AA2024-T3) involving one-sided unsteady-state heating and constant tension loading. When exposed to the same radiant thermal flux, the surface and internal temperatures of the composite and aluminium alloy were different due to differences in their thermal conductivity as well as fire-induced damage (e.g. delamination cracks, fibre-matrix debonding) and decomposition to the composite. Under tensile loading, the aluminium deformed when exposed to fire via elastic, plastic and creep-induced softening processes whereas the composite deformed at a much slower rate due to matrix softening and decomposition. For the experimental test conditions, the tensile load-bearing capacity of the composite was superior to the aluminium alloy when exposed to the thermal flux, and this was due to the capacity of the load-bearing carbon fibres to retain high tensile stiffness and strength to much higher temperatures.
更多查看译文
关键词
Composites,Fire,High temperature,Mechanical properties
AI 理解论文
溯源树
样例
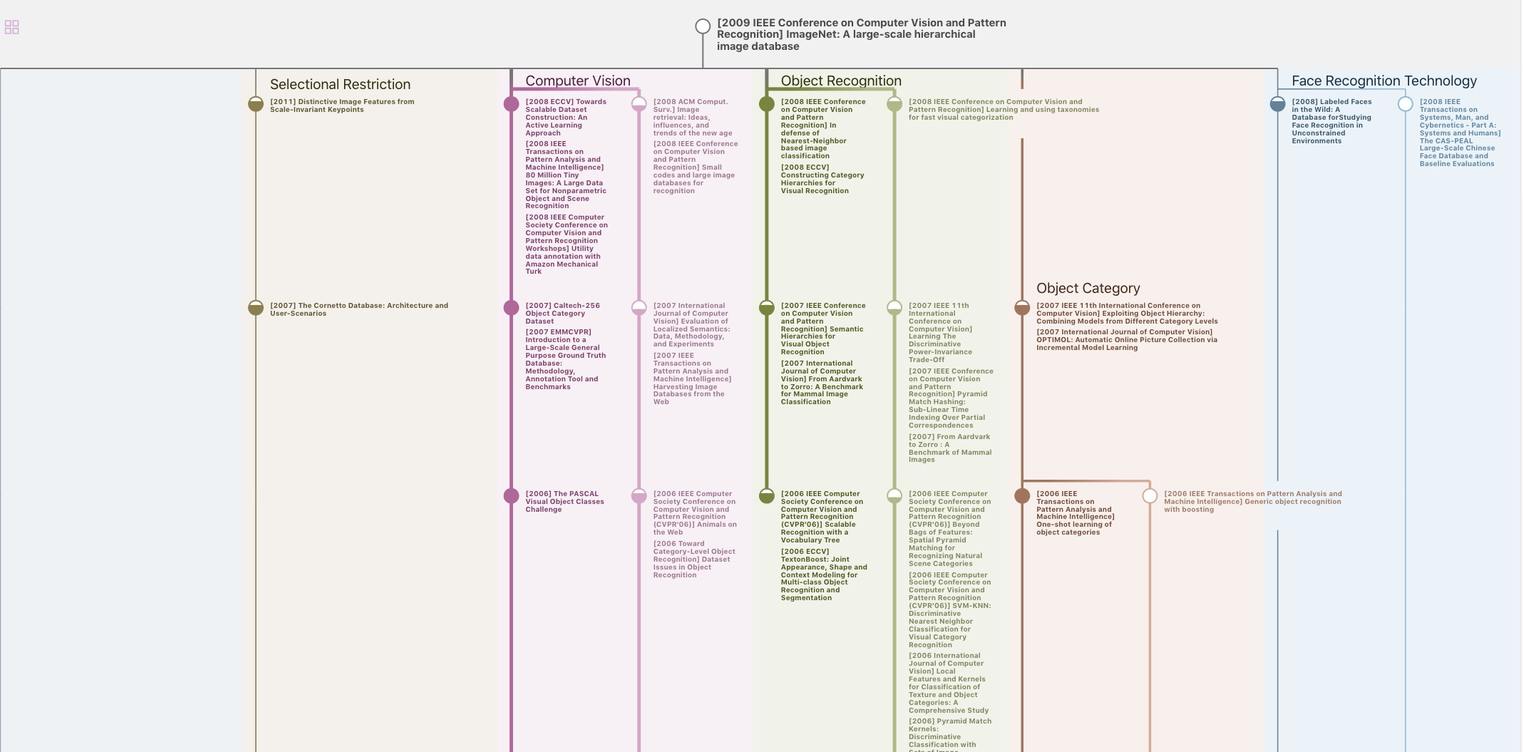
生成溯源树,研究论文发展脉络
Chat Paper
正在生成论文摘要