Reducing deformation, stress, and tool wear during milling processes using simulation-based multiobjective optimization
The International Journal of Advanced Manufacturing Technology(2018)
摘要
This paper presents the optimization of a dry machining process where thermomechanical effects like shape deviations and a time-dependent domain are major challenges. First, the simulation model to compute finite element approximations to a general milling process is presented. The model includes a submodel (dexel model) for material removal and process forces and heat flux introduced by the machining tool. In a second part, we present a multiobjective optimization algorithm based on metamodels that serve as a tool to identify the process parameters that improve processes with different performance measures that exhibit conflicting behavior. With this metamodel-based optimization method, we avoid the use of a large number of high-fidelity computer simulations, which are commonly computationally expensive. The approach is tested on two case studies for optimizing (a) workpiece deformation and equivalent stress after milling, and (b) shape error and tool wear.
更多查看译文
关键词
Milling,Multiobjective optimization,Thermomechanics,Adaptive FEM
AI 理解论文
溯源树
样例
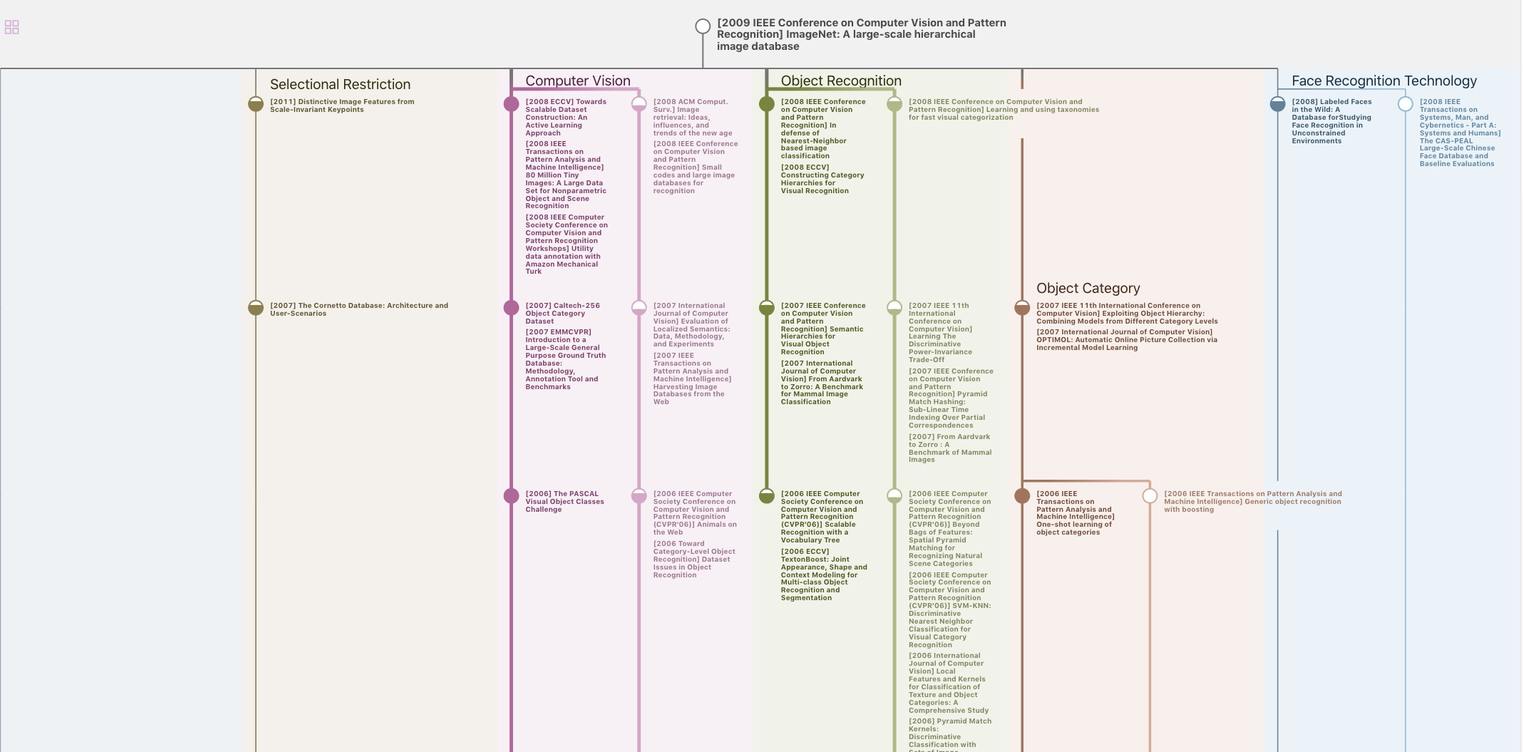
生成溯源树,研究论文发展脉络
Chat Paper
正在生成论文摘要