Optimizing Grippers For Compensating Pose Uncertainties By Dynamic Simulation
2016 IEEE INTERNATIONAL CONFERENCE ON SIMULATION, MODELING, AND PROGRAMMING FOR AUTONOMOUS ROBOTS (SIMPAR)(2016)
摘要
Gripper design process is one of the interesting challenges in the context of grasping within industry. Typically, simple parallel-finger grippers, which are easy to install and maintain, are used in platforms for robotic grasping. The context switches in these platforms require frequent exchange of gripper fingers to accommodate grasping of new products, while subjected to numerous constraints, such as workcell uncertainties due to the vision systems used. The design of these fingers consumes the man-hours of experienced engineers, and involves a lot of trial-and-error testing.In our previous work, we have presented a method to automatically compute the optimal finger shapes for defined task contexts in simulation. In this paper, we show the performance of our method in an industrial grasping scenario. We first analyze the uncertainties of the used vision system, which are the major source of grasping error. Then, we perform the experiments, both in simulation and in a real setting. The experiments confirmed the validity of our approach. The computed finger design was employed in a real industrial assembly scenario.
更多查看译文
关键词
gripper design process,robotic grasping,parallel-finger grippers,trial-and-error testing
AI 理解论文
溯源树
样例
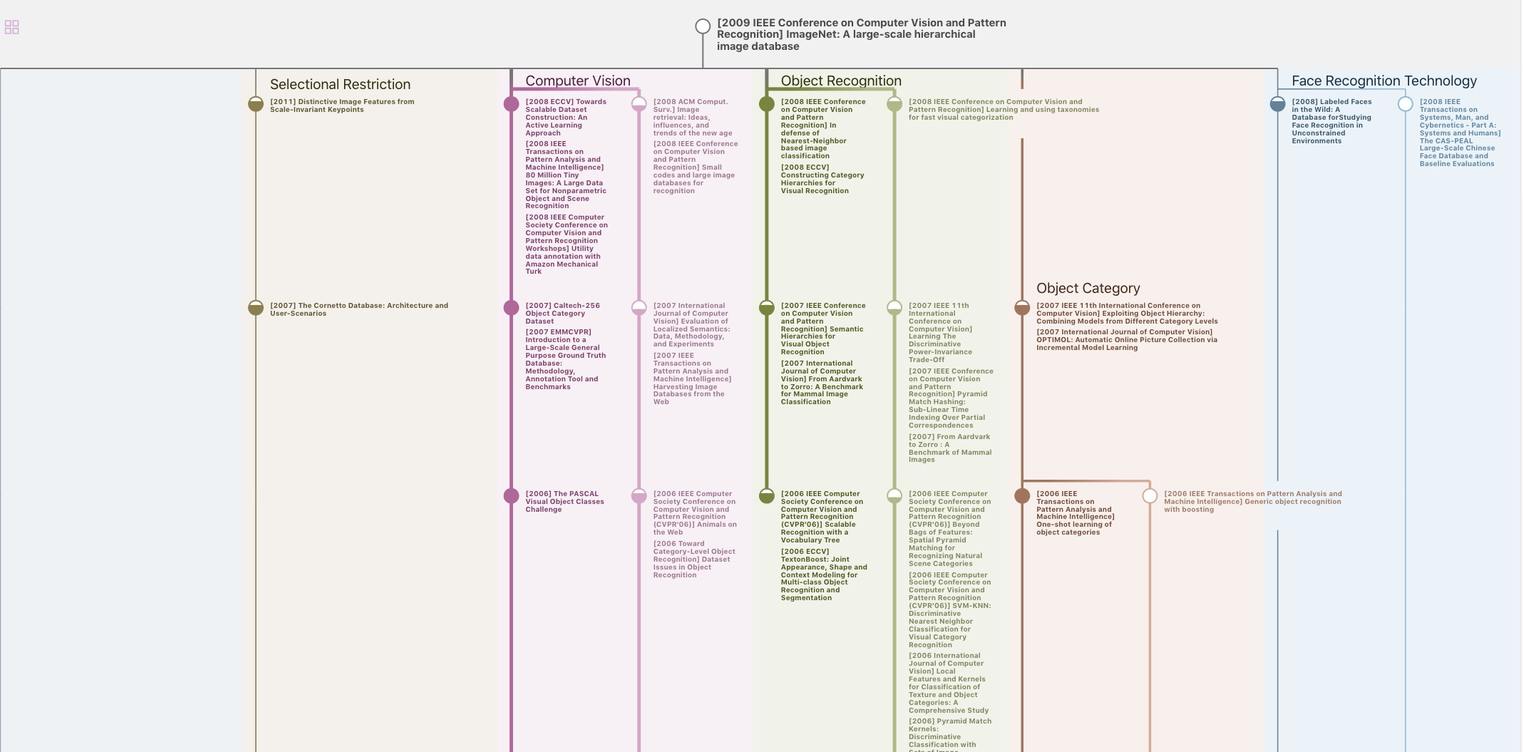
生成溯源树,研究论文发展脉络
Chat Paper
正在生成论文摘要