Customization Of Low-Cost Hexapod Robots Based On Optimal Design Through Inverse Dynamics Computation
2015 20th International Conference on Methods and Models in Automation and Robotics (MMAR)(2015)
摘要
The Stewart parallel mechanism is used in various applications due to its high load-carrying capacity, accuracy and stiffness, such as flight simulation, spaceship aligning, radar and satellite antenna orientation, rehabilitation applications, parallel machine tools. The dissemination of such parallel robots is however limited by three factors: the limited workspace, the singularity configurations existing inside the workspace, and the high cost. In this work, a simulation environment to support the design of a cost-effective Stewart Platform-based mechanisms for specific applications and to facilitate the choice of suitable components, e.g., linear actuators, plate sizes, is presented. The optimal design here presented has multiple objectives. It intends to maximize the payload and minimize the forces at each leg needed to counteract external forces applied to the mobile platform during positioning or manufacturing applications. These objectives can be achieved through a dynamic optimization. It also aims at avoiding reduction of the robot workspace through a kinematic optimization.
更多查看译文
关键词
low-cost hexapod robot customization,optimal design,inverse dynamics computation,Stewart parallel mechanism,high load-carrying capacity,flight simulation,spaceship aligning,radar orientation,satellite antenna orientation,rehabilitation applications,parallel machine tools,parallel robot dissemination,singularity configurations,simulation environment,Stewart Platform-based mechanisms,mobile platform,positioning application,manufacturing application,dynamic optimization,robot workspace,kinematic optimization
AI 理解论文
溯源树
样例
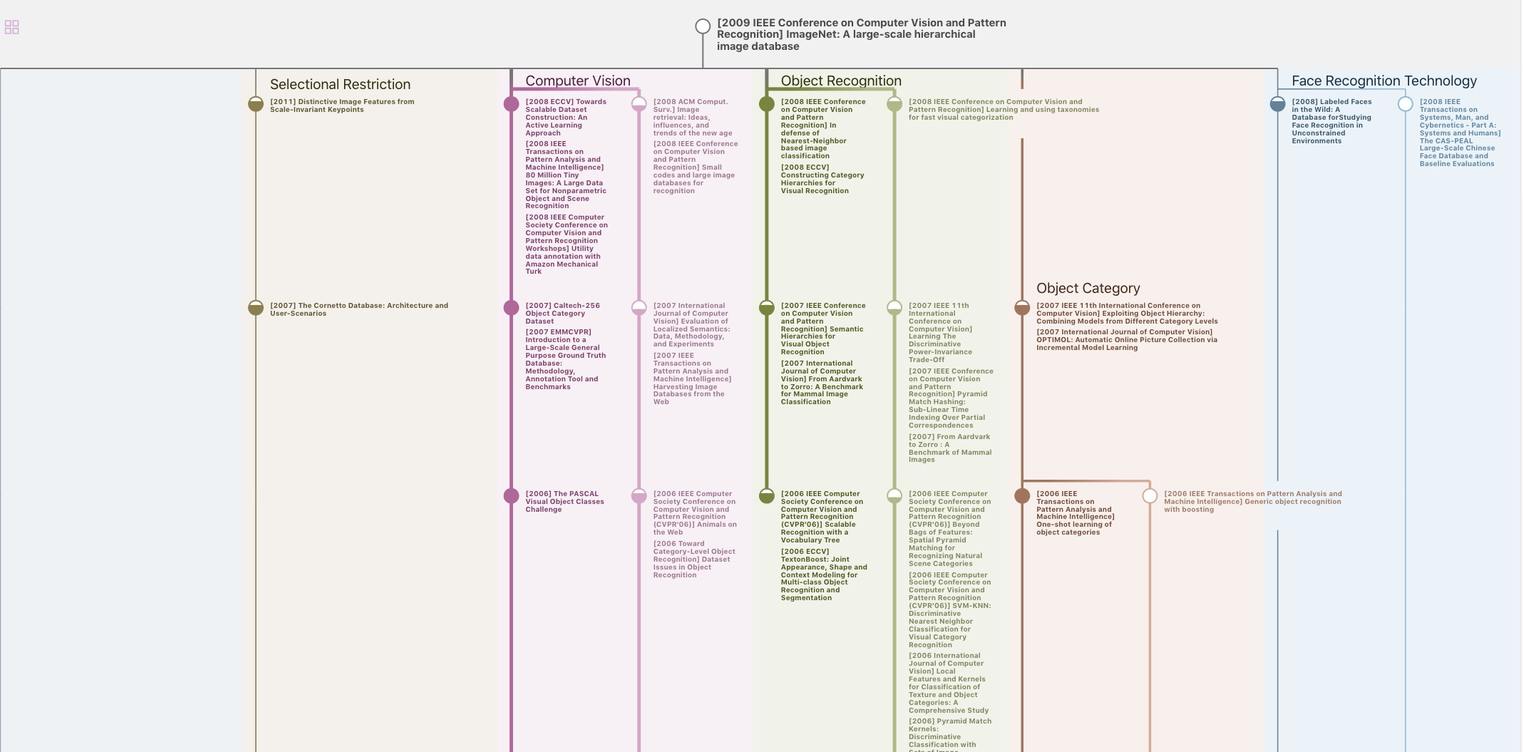
生成溯源树,研究论文发展脉络
Chat Paper
正在生成论文摘要