Minimization of hot spot in a microchannel reactor for steam reforming of methane with the stripe combustion catalyst layer
International Journal of Hydrogen Energy(2013)
摘要
Hot spot formation is inevitable in a heat exchanger microchannel reactor used for steam reforming of methane because of the local imbalance between the generated and absorbed heat. A stripe configuration of the combustion catalyst layer was suggested to make the catalytic combustion rate uniform in order to minimize the hot spot near the inlet. The stripe configuration was optimized by response surface methodology with computational fluid dynamics. With the optimal catalyst layer, the hot spot was not observed near the inlet and the maximum temperature decreased by 130 K from that of the uniform catalyst layer without any conversion loss. The maximum relative particle diameters of the uniform and the optimal stripe catalyst layer were about 3.68 and 2.51, respectively, and the surface-averaged particle diameter of the optimal stripe catalyst layer was 7.64% less than that of the uniform stripe catalyst layer.
更多查看译文
关键词
Steam reforming of methane,Microchannel,Heat exchanger reactor,Hot spot,Response surface methodology,Catalytic surface area
AI 理解论文
溯源树
样例
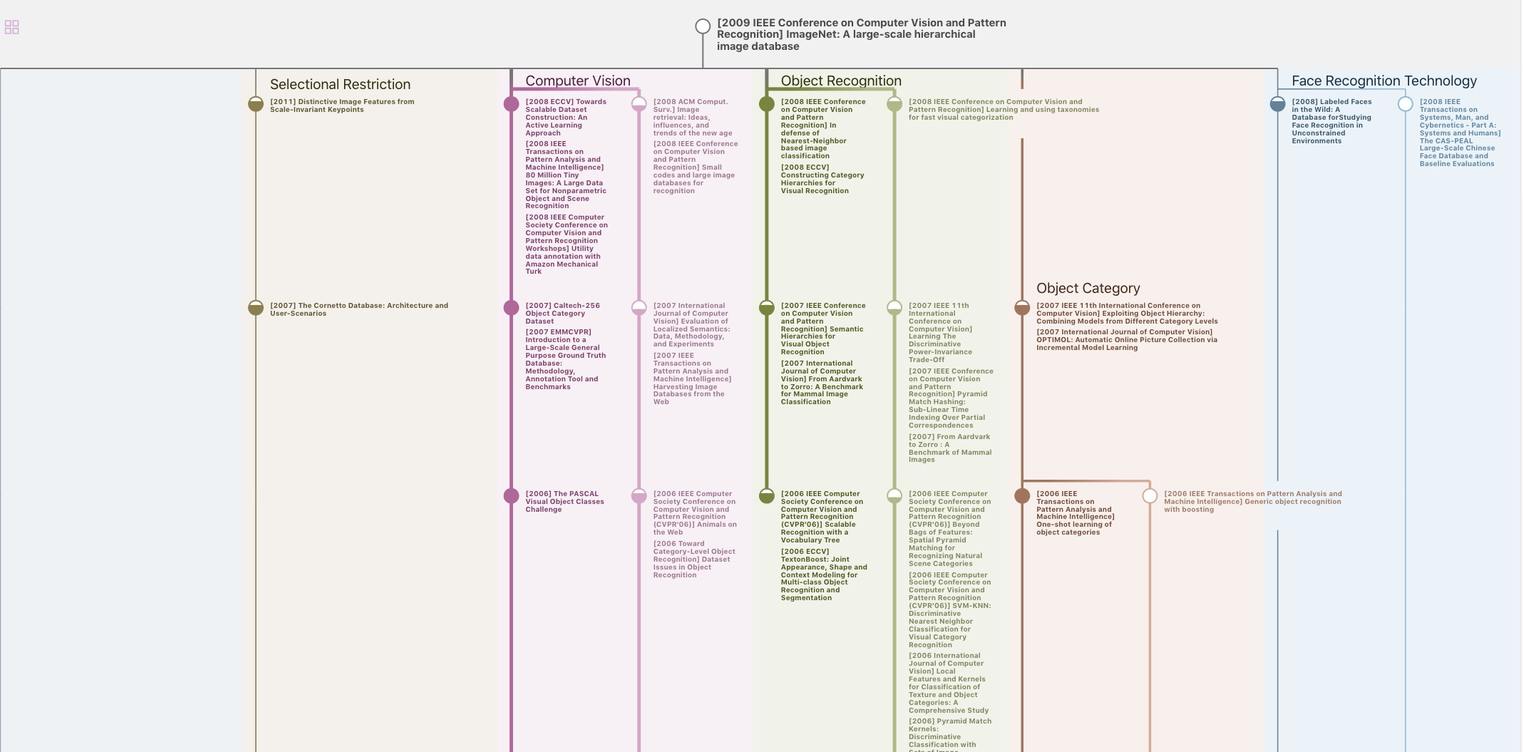
生成溯源树,研究论文发展脉络
Chat Paper
正在生成论文摘要