Fatigue Crack Growth Analysis Under Spectrum Loading in Various Environmental Conditions
Metallurgical and Materials Transactions A-physical Metallurgy and Materials Science(2013)
摘要
The fatigue process consists, from the engineering point of view, of three stages: crack initiation, fatigue crack growth, and the final failure. It is also known that the fatigue process near notches and cracks is governed by local strains and stresses in the regions of maximum stress and strain concentrations. Therefore, the fatigue crack growth can be considered as a process of successive crack increments, and the fatigue crack initiation and subsequent growth can be modeled as one repetitive process. The assumptions mentioned above were used to derive a fatigue crack growth model based, called later as the UniGrow model, on the analysis of cyclic elastic–plastic stresses–strains near the crack tip. The fatigue crack growth rate was determined by simulating the cyclic stress–strain response in the material volume adjacent to the crack tip and calculating the accumulated fatigue damage in a manner similar to fatigue analysis of stationary notches. The fatigue crack growth driving force was derived on the basis of the stress and strain history at the crack tip and the Smith–Watson–Topper (SWT) fatigue damage parameter, D = σ max Δε/2. It was subsequently found that the fatigue crack growth was controlled by a two-parameter driving force in the form of a weighted product of the stress intensity range and the maximum stress intensity factor, Δ K p K max 1− p . The effect of the internal (residual) stress induced by the reversed cyclic plasticity has been accounted for and therefore the two-parameter driving force made it possible to predict the effect of the mean stress including the influence of the applied compressive stress, tensile overloads, and variable amplitude spectrum loading. It allows estimating the fatigue life under variable amplitude loading without using crack closure concepts. Several experimental fatigue crack growth datasets obtained for the Al 7075 aluminum alloy were used for the verification of the proposed unified fatigue crack growth model. The method can be also used to predict fatigue crack growth under constant amplitude and spectrum loading in various environmental conditions such as vacuum, air, and corrosive environment providing that appropriate limited constant amplitude fatigue crack growth data obtained in the same environment are available. The proposed methodology is equally suitable for fatigue analysis of smooth, notched, and cracked components.
更多查看译文
关键词
Residual Stress, Stress Intensity Factor, Fatigue Life, Fatigue Crack Growth, Fatigue Crack Growth Rate
AI 理解论文
溯源树
样例
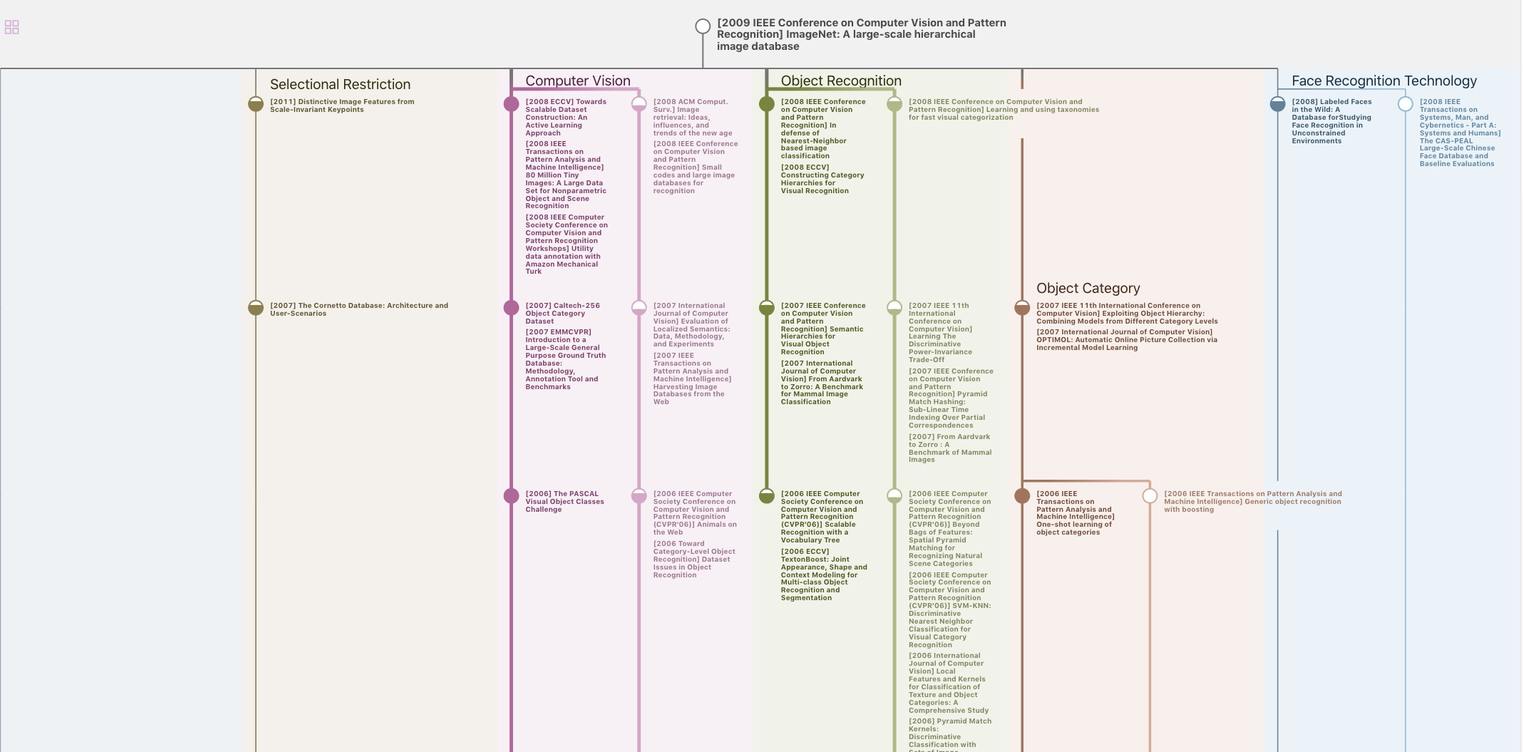
生成溯源树,研究论文发展脉络
Chat Paper
正在生成论文摘要