Non-singular tool path planning by translating tool orientations in C-space
The International Journal of Advanced Manufacturing Technology(2014)
摘要
This paper discusses the singular problem in five-axis machining of freeform surfaces. At first, the generating mechanism of the singularities is studied on the unit sphere in the P-system. Then a new method is developed to avoid the singularities by translating the tool orientations in the configuration-space (C-space) at the time just after the initial cutter locations have been generated for a cutter contact (CC) trajectory on the surface. The tool orientation vectors of the initial cutter locations are projected onto the C-space, forming the orientation polyline. In the C-space, a taper circle is defined. The singularities are detected by contact checking between the orientation polyline and the taper circle. Once they contact, the orientation polyline is translated by a minimum translating vector to avoid the contact. The minimum translating vector is picked on the offset polyline of the original orientation polyline. After that, the translated orientation polyline is inversed to calculate the optimized cutter locations in the P-system. The benefit of avoiding singularities at the tool path planning stage is that the original CC points on the CC trajectory are respected. The developed method is programed and tested through contrastive experiments. Results show that the optimized cutter locations can effectively avoid the singularities.
更多查看译文
关键词
Five-axis singularity, Freeform surface machining, C-space, Translating orientation polyline
AI 理解论文
溯源树
样例
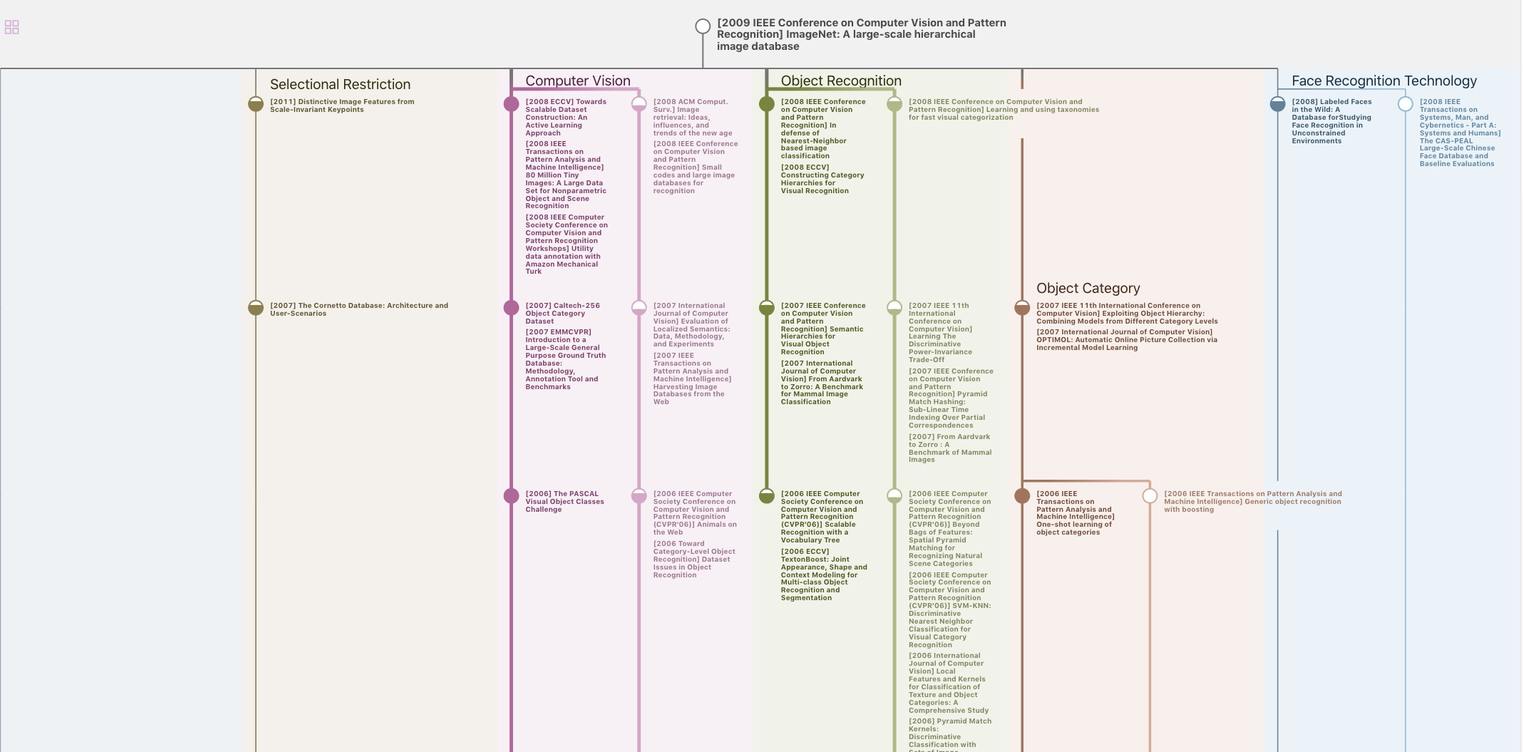
生成溯源树,研究论文发展脉络
Chat Paper
正在生成论文摘要