The influence of tool geometry and rotational speed on friction stir spot welding of aluminum alloy AA- 6181-T4
SOLDAGEM & INSPECAO(2012)
摘要
Friction Stir Spot Welding is a process that occurs in solid state with high energy efficiency, low manufacture costs and environmentally friendly These friction processes are an alternative to conventional processes like resistance spot welding, riveting and clinching. The absent of a fusion zone on these processes avoid defects like porosity, bubbles, recess, inclusions and undesired microstructures, that appears very often on weld metal and heat affected zones of fusion weld processes. The Friction Stir Spot Welding process (SPFMM-FSSW) consists in a rotating tool (pin and shoulder combined) that penetrates the overlap joint stirring the material and consolidating the joint. The contact of adjacent region of the tool generates the friction heating and, this heating, promotes the plasticization of the material that, at the same time, is stirred by the tool pin leaving a stir zone and a keyhole after process is finished. The aim of the present work is to evaluate the influence of tool profile and rotational speed on the mechanical and metallurgical behavior of friction stir spot welded AA6181-T4 aluminum alloy The metallurgical characterization was performed through optical microscopy, stereoscope and scanning electron microscopy. The mechanical testing was made trough shear test, microhardness profile and torque/forces monitoring during the process. It was possible to observe a tendency of increasing in mechanical strength of the joint with applying higher rotational speed values. The utilization of different tool profiles presented significant differences, but, with much reliance of the rotational speed, pin and shoulder combination.
更多查看译文
关键词
Friction welding,Tool Profile,Rotational Speed
AI 理解论文
溯源树
样例
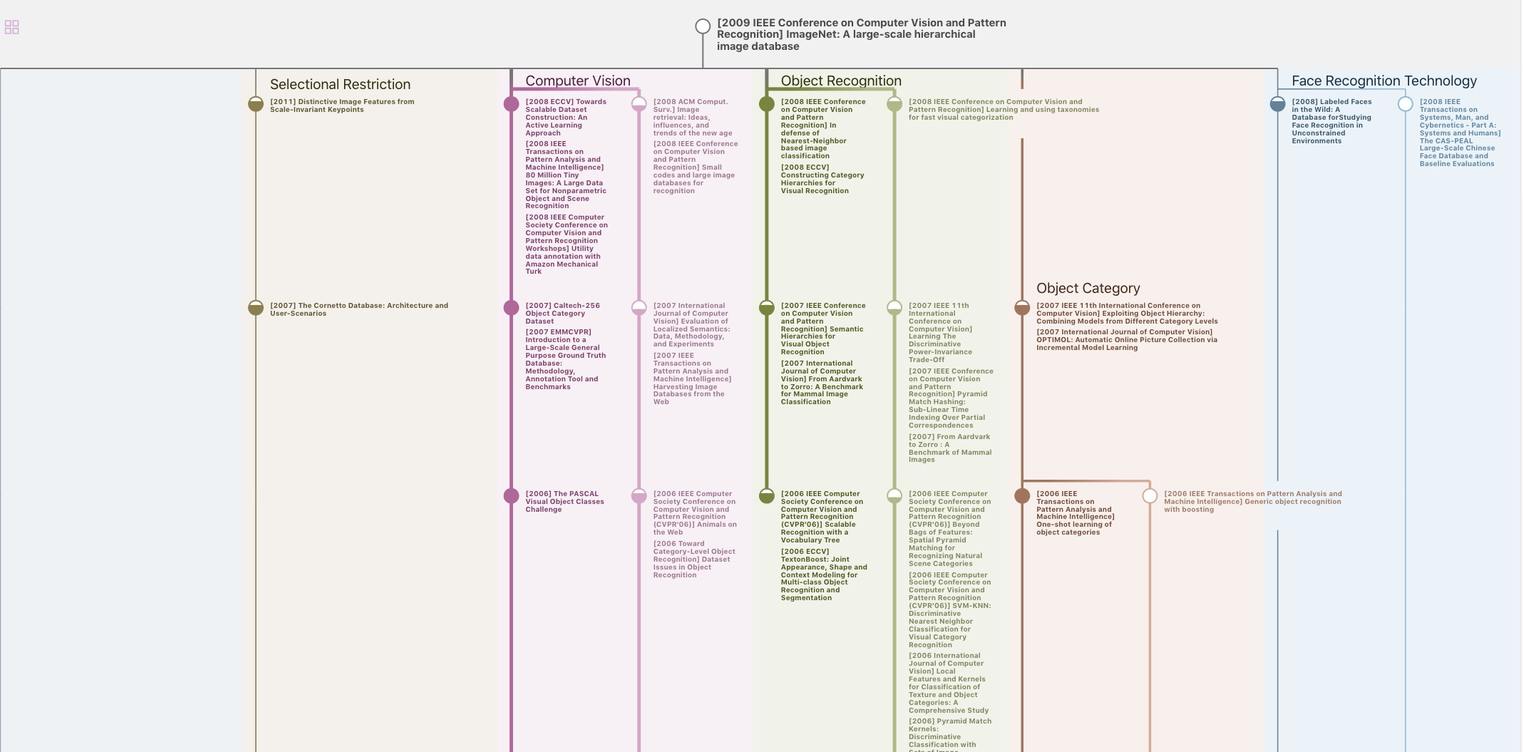
生成溯源树,研究论文发展脉络
Chat Paper
正在生成论文摘要