Development Of Closed-Form Solutions For Fast Thermal Modeling Of Rotating Electric Machinery
2013 IEEE INTERNATIONAL ELECTRIC MACHINES & DRIVES CONFERENCE (IEMDC)(2013)
摘要
Accurate knowledge of winding temperature is critical for the control, protection, and real-time monitoring of high-performance electric machines. Lumped parameter and finite element analyses can be used to model thermal stress, but both have drawbacks in applications where fast estimates of local temperature distributions are necessary. To overcome this, a closed-form solution for the steady-state stator temperature distribution over one slot pitch in a radial air gap electric machine is presented. Machine symmetry and material thermal properties are used to create a representative layer model in which a solution to Laplace's equation is developed. In addition to lumped parameter and three-dimensional (3D) finite element models, the method is verified through experimental results. Analytical model winding temperature predictions are within about 2.5% of finite element model predictions. Estimates of stator slot, tooth, and end-winding temperatures are within 7% of experimental measurements. The results are shown to have value for parametric machine design and protection.
更多查看译文
关键词
heat transfer,windings,boundary conditions,air gaps,thermal stress,laplace equation,finite element analysis,temperature measurement,lamination
AI 理解论文
溯源树
样例
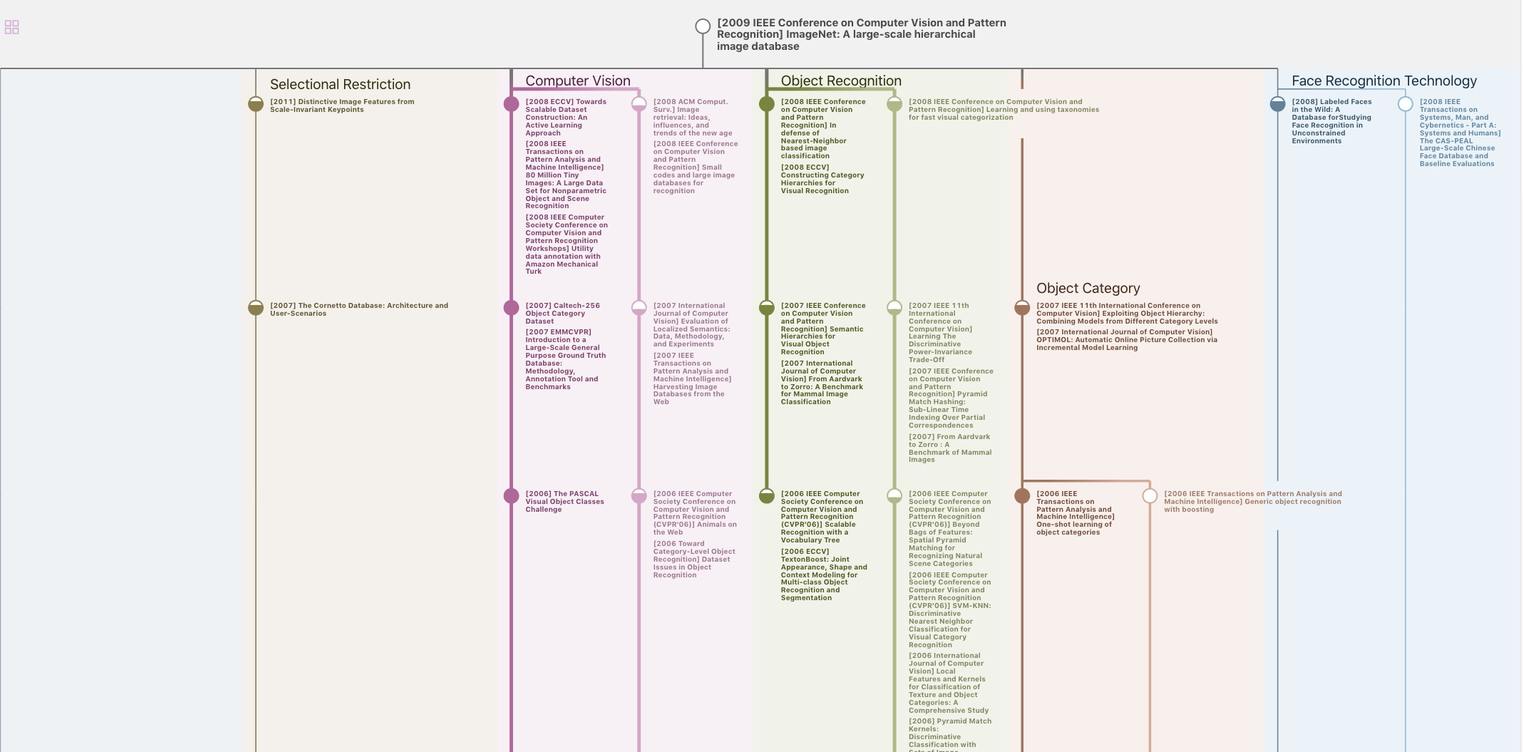
生成溯源树,研究论文发展脉络
Chat Paper
正在生成论文摘要