A Finite Element Evaluation Of A Bearing Instrumentation Method For Evaluating Bearing Load Distributions And Roller Stresses Of The Final Drive Of A Wind Turbine Gearbox
INTERNATIONAL GEAR CONFERENCE 2014(2014)
摘要
This paper presents an evaluation of measurements being taken on a 750 kW wind turbine gearbox that is being tested by the National Renewable Energy Laboratory (NREL). The high speed stage gears and bearings have been identified as critical components of the gearbox. During a phase of testing, this portion of the gearbox has been instrumented and tests have been developed to evaluate the loads on the high speed tapered roller bearings (TRBs). Gages are placed in axial grooves that are machined into the outer race of the TRBs. Each bearing has four axial grooves with two gages per groove. There was initial concern as to whether the strain levels would be high enough in the bearing raceways to provide an adequate signal to noise ratio, motivating the analysis presented here.In this paper, an advanced finite element based contact modeling procedure has been applied to model the high speed stage with the bearings fully modeled in order to evaluate strain levels. The model includes the rollers of each of the bearings on the gear and pinion shafts as well as the gear tooth contacts. A major conclusion is that the strains of the slotted grooves are at such a level that they have acceptable signal to noise levels. This was verified in results of the initial experiments that are presented.
更多查看译文
AI 理解论文
溯源树
样例
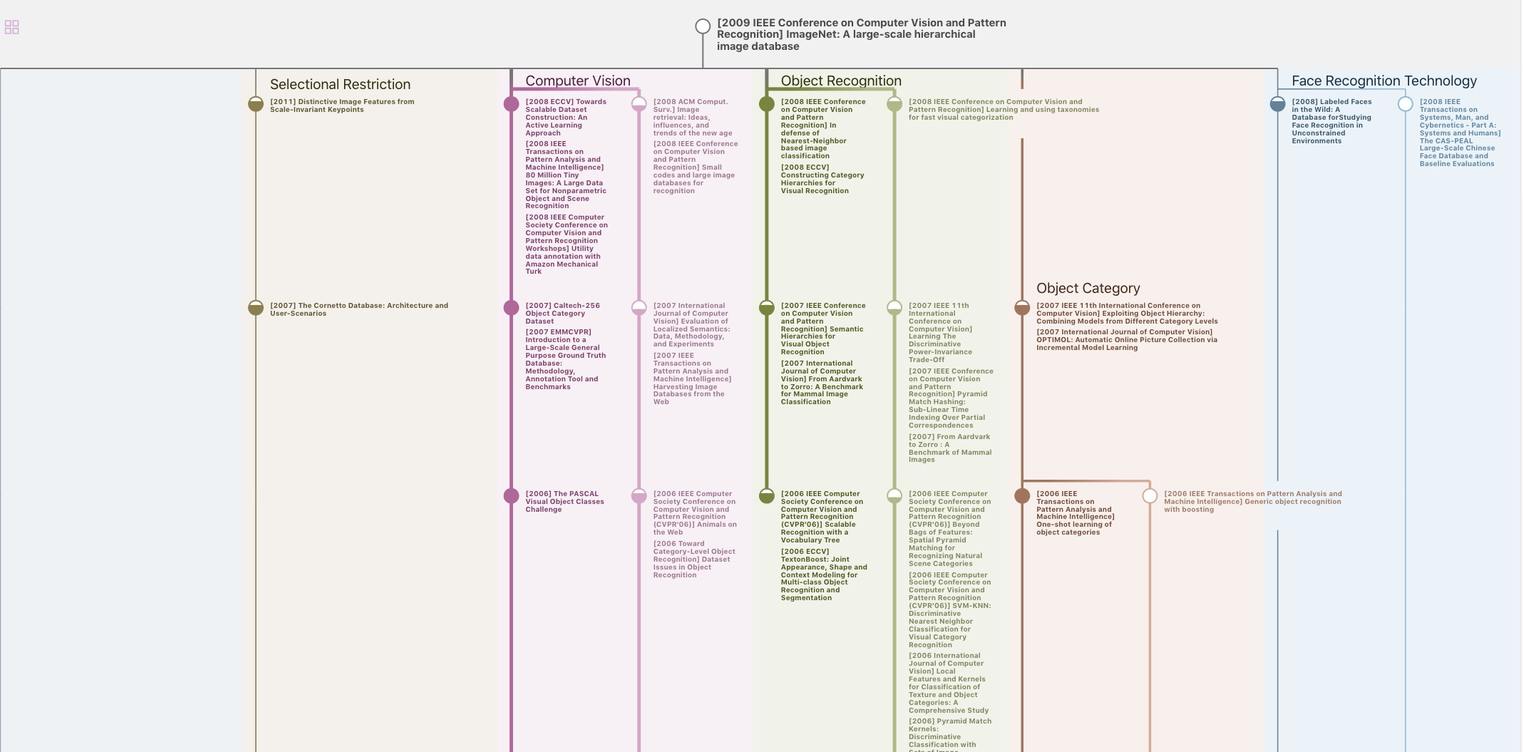
生成溯源树,研究论文发展脉络
Chat Paper
正在生成论文摘要