Development of a large ingot continuous caster
METALLURGICAL RESEARCH & TECHNOLOGY(2015)
摘要
A large ingot continuous caster (LICC) has been developed to increase international competitiveness in world steel markets by obtaining a higher yield and reduction of process for steelmaking industries as well as increasing quality by replacing the ingot casting process for production of an extra-large section size strand and high-alloy specialty steel. A conventional continuous caster of an extra-large section size needs a considerable amount of investment compared with a vertical semi-continuous caster such as the LICC. While the LICC is favorable for producing small lots for various steel grades, a conventional continuous caster is suitable for mass production of certain steel grades. The process of a conventional continuous caster and the process of a LICC from a ladle to a strand are similar to each other except for the withdrawer type and the standing below the LICC mold until complete solidification is achieved. At the end of the casting, the LICC bloom moves downward and stops at a certain distance below the mold, and then stands on a vertical position waiting for complete solidification. The LICC bloom is pushed horizontally to the tilter, the purpose of which is to set the bloom in a horizontal position. During the pushing stage, the bloom is separated from a well block. After a hot run of the pilot large ingot continuous caster (LICC), more than 90 heats of 12-ton liquid steel per heat for various steel grades were cast through the caster without any negative impact on the equipment or operations. From the LICC process developed by POSCO, most steel grades such as medium-carbon structural steels, stainless steels and tool steels have been cast successfully and confidently. Their surface and internal quality were found to be better than those of ingots and easily acceptable for the next process. We were able not only to design a continuous casting plant from concept design to detailed design but also to operate a new caster by ourselves. The equiaxed zone was much enlarged and its structure was found to be compactly composed of fine globular crystals. The shrinkage pipe was also greatly reduced from L to 0.23L by top heating and stirring. The casting speed, casting temperature, stirring and temperature gradient of the strand were found to be the "vital few" parameters affecting the internal quality based on investigations of the evaluation results of the macro-structure of the cast TD11 steel. The internal quality of the LICC strand for TD11 steel was much improved by using the optimum combination of these parameters, and the rolled bloom from the LICC strand has excellent internal soundness.
更多查看译文
关键词
Large ingot continuous caster (LICC),concept design,basic design,solidification profile,shrinkage pipe,internal quality,highalloy specialty steel,tool steel
AI 理解论文
溯源树
样例
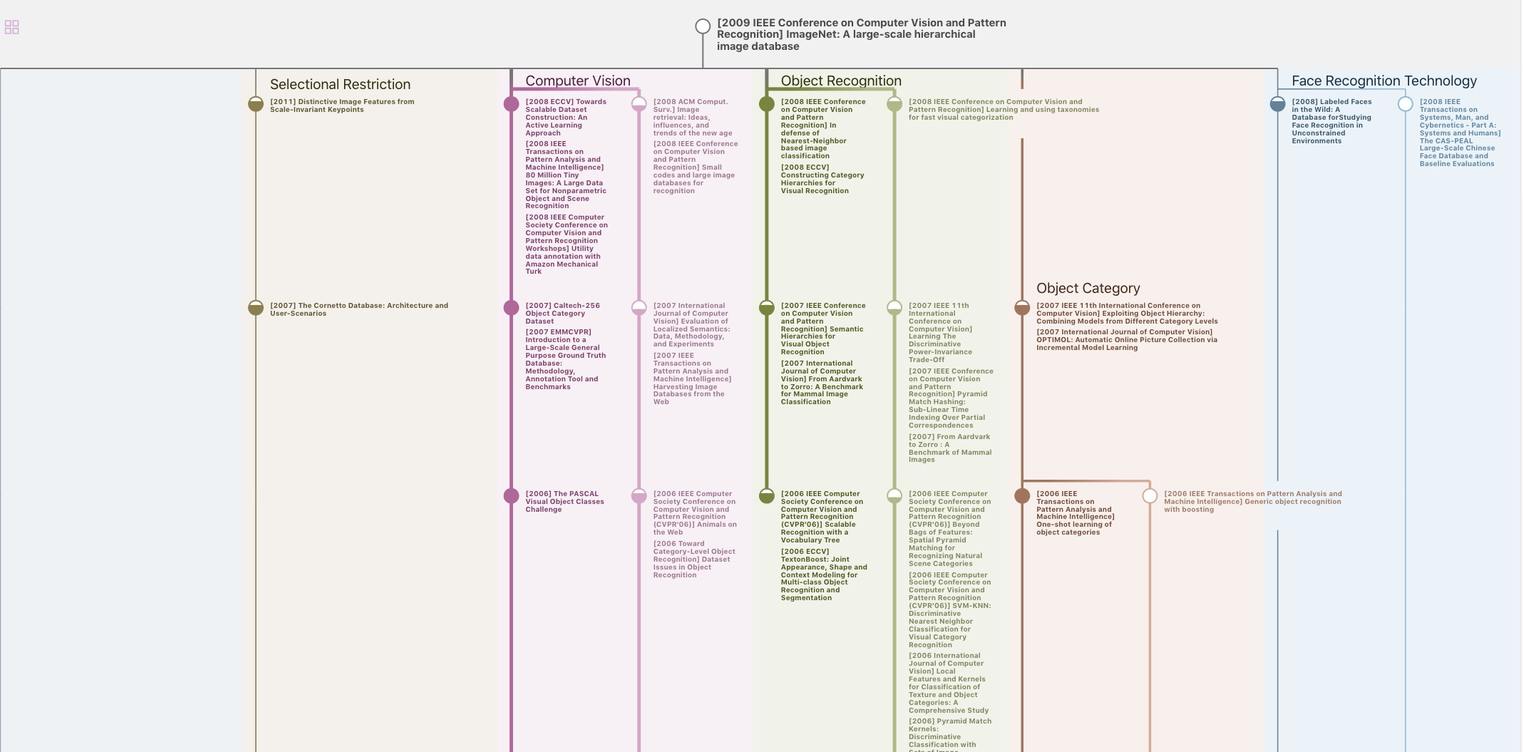
生成溯源树,研究论文发展脉络
Chat Paper
正在生成论文摘要