Roll compaction process modeling: transfer between equipment and impact of process parameters.
International journal of pharmaceutics(2015)
摘要
In this study, the roll compaction of an intermediate drug load formulation was performed using horizontally and vertically force fed roll compactors. The horizontally fed roll compactor was equipped with an instrumented roll technology allowing the direct measurement of normal stress at the roll surface, while the vertically fed roll compactor was equipped with a force gauge between the roll axes. Furthermore, characterization of ribbons, granules and tablets was also performed. Ribbon porosity was primarily found to be a function of normal stress, exhibiting a quadratic relationship thereof. A similar quadratic relationship was also observed between roll force and ribbon porosity of the vertically fed roll compactor. The predicted peak pressure (Pmax) using the Johanson model was found to be higher than the measured normal stress, however, the predicted Pmax correlated well with the ribbon relative density/porosity and the majority of downstream properties of granules and tablets, demonstrating its use as a scale-independent parameter. A latent variable model was developed for both the horizontal and vertical fed roll compactors to express ribbon porosity as a function of geometric and process parameters. The model validation, performed with new data, resulted in overall good predictions. This study successfully demonstrated the scale up/transfer between two different roll compactors and revealed that the combined use of design of experiments, latent variable models and in silico predictions result in better understanding of the critical process parameters in roll compaction.
更多查看译文
AI 理解论文
溯源树
样例
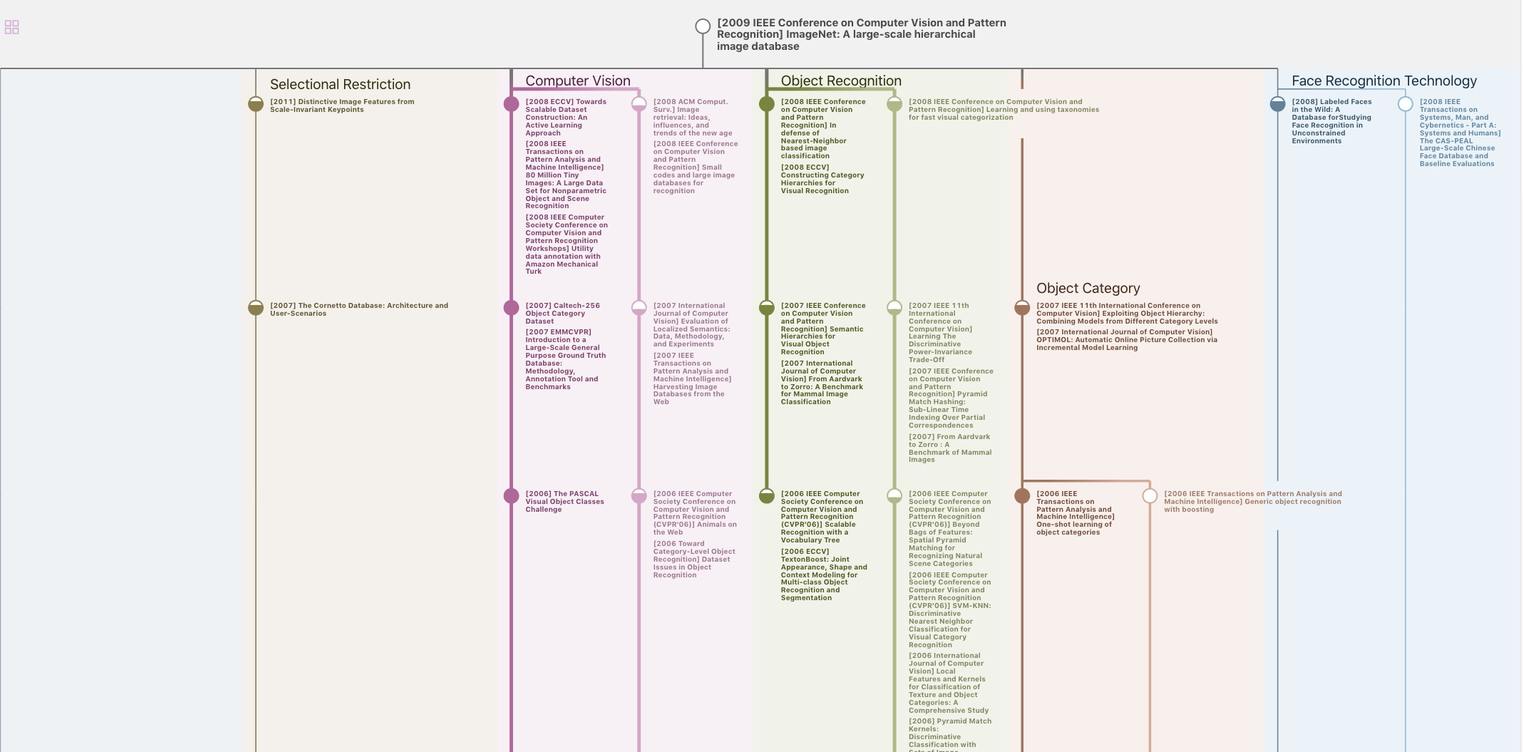
生成溯源树,研究论文发展脉络
Chat Paper
正在生成论文摘要