Effect Of Thermal And Mechanical Loads On The Centrifugal Impeller Deformation And Its Structure Optimization
PROCEEDINGS OF ASME TURBO EXPO 2009, VOL 5(2009)
摘要
Micro gas turbines are becoming popular for the distributed electric generator and propulsion system of small air vehicles. The centrifugal compressor impeller is an important component in the micro gas turbine and its aerodynamic performance and structural reliability have great effects on the system. This paper studied the impeller deformation caused by the thermal load (temperature variation) and mechanical loads (aerodynamic pressure and centrifugal force) and its influence on the impeller aerodynamic performance. Combined computational fluid dynamics (CFD) flow analysis and finite element method (FEM) structure analysis, using the fluid-solid and heat-solid interaction technology, the aerodynamic and temperature effects were transferred on the solid blade surfaces as loads to analyze the strain and stress of the centrifugal blade. The working blade profile was achieved by calculating the deformation magnitude of the solid grid nodes.The research showed that the largest deformation occurred at the blade inducer tip and the variation of tip clearance caused by blade deformation brought some influence not only on the aerodynamic performance but also on the structure reliability of the impeller. In order to reduce the impeller deformation under working condition, the hub section profile of the impeller was redesigned by an optimization method.
更多查看译文
关键词
impellers,optimization,stress,deformation
AI 理解论文
溯源树
样例
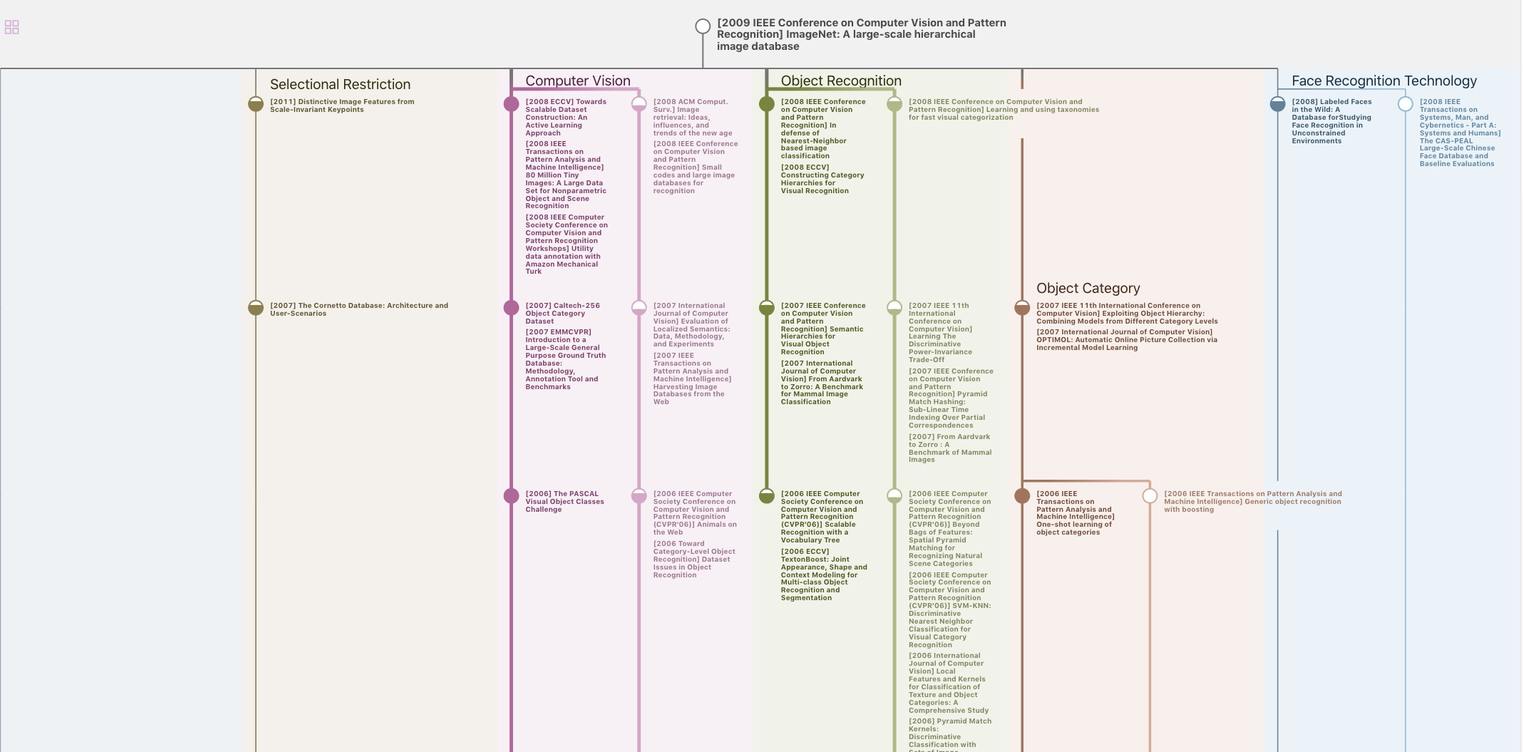
生成溯源树,研究论文发展脉络
Chat Paper
正在生成论文摘要