Numerical optimal design of a non-overload centrifugal pump
ASME Fluids Engineering Division Summer Meeting(2012)
摘要
Shaft power characteristics of centrifugal pumps attract extensive attentions in order to improve the operating reliability of pumps. TS-50-32-250 type low specific speed centrifugal pumps are selected as the research subjects. Three parameters of impeller including blade outlet angle beta(2), outlet width b(2) and wrapping angle of blade theta are selected for the impeller shape optimization. Maximum flow design method and non-overload design method are adopted to design 7 impellers. Numerical simulation with CFX 12.1 is used to reduce the cost and shorten the design period. The time-averaged Navier-Stokes equations of 3D steady flow in the pump are calculated by CFX 12.1 based on the standard k-epsilon turbulence model together with standard wall function. The structured grids of different qualities are used in unmodified impeller for comparison to confirm that the results are not influenced by the quality of mesh. The optimal impeller is obtained when beta(2), b(2), 8 are 18, 7mm, 175 degrees, respectively. The performances of NCPs at other working conditions satisfy the requirements of heads and efficiencies obtained from China National Standard. The shaft power reaches to 15 kW which is the power rating of the matched motor, at 1.45Q(R) (35m(3)/h), showing that the non-overload performance of the pump is also significantly improved after modifying impeller geometries. Impeller 6 is considered as the optimal one and produced for experiments. Experiment results prove that it is effective and reliable to improve a non-overload pump's performance by maximum flow design method and non-overload pump design method. The results provide a reference for increasing the efficiencies and heads of non-overload pumps at multiple operating conditions.
更多查看译文
关键词
design,centrifugal pumps
AI 理解论文
溯源树
样例
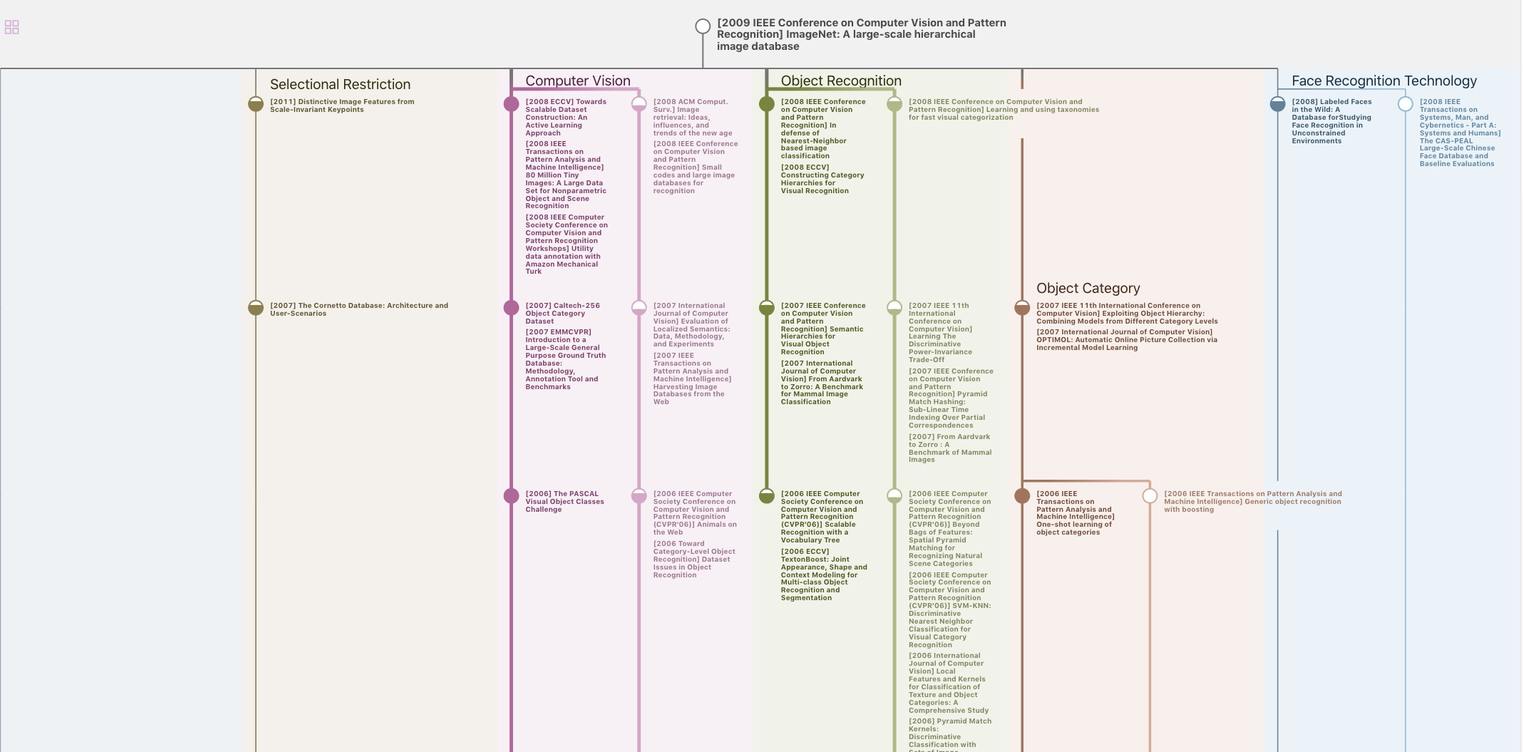
生成溯源树,研究论文发展脉络
Chat Paper
正在生成论文摘要