A new binder system for preparing high strength inorganic molds in precision casting
Materials Chemistry and Physics(2011)
摘要
Research highlights ▶ The new binder system has been developed using precursor materials. ▶ The binder composition affects the glassification efficiency. ▶ The fracture strength is markedly enhanced in the new binder systems. ▶ The new binder system with 7.6 wt% PDMS shows the highest strength of 8 MPa. Abstract A new composite binder system has been developed to improve the strength and to decrease the processing time of inorganic binder mold for precision casting, as functions of dipping time and binder composition. The new binder system was prepared by mixing tetraethyl orthosilicate and polydimethyl siloxane as silicate precursors, and sodium methoxide as the precursor of sodium oxide. Samples of molds coated with an organic binder were dipped into the prepared binder systems, and then heat treated at 1000 °C for a period of 1 h. The fracture strength was markedly enhanced in the new binder systems owing to the increase in reaction depth, independent of the dipping time, whereas the fracture strength of the conventional binder system was not increased, even after a dipping time of 2 h. The new binder system containing 7.6 wt% PDMS showed the highest nominal strength of 8 MPa. When PDMS was used as the silicate precursor in the new binder system, the high glassification efficiency of silicate led to the higher fracture strength, resulting from the lack of hydrolysis and condensation reactions of PDMS. The fracture strength could be controlled by changing the molecular structure of binder and the binder composition. Keywords Ceramics Inorganic compounds Heat treatment Mechanical properties 1 Introduction The ceramic mold process using inorganic binders such as ethyl silicate and colloidal silica aquasols has been developed recently in precision casting, especially applicable to the precision casting of thin stainless steel using a lost wax casting technique [1,2] . Saridikmen et al. studied the fabrication of ceramic mold using inorganic binders with two different compositions, ethyl silicate and ethyl silicate/aluminum tri-sec-butoxide solution [3] . However, the process for prevention of the reaction between ceramic mold and molten metal has lots of limiting factors to be applied to real work environments, due to the high temperature of molten metal (above 1450 °C) and the high shrinkage of ceramic mold. Jiang et al. researched the dimensional changes and variability of ceramic molds in steel castings through a stepped pyramid-shaped part [4] . Gelling agent such as ammonium carbonate and acetic acid has to be added in the ceramic mold process using silicate as inorganic binder. However, the inorganic binder molds fabricated by the convert mold process have many advantages for precision casting, such as low heat treatment (about 1000 °C), without gelling agent, high strength, enhancement of collapse, easy processability, and high thermal stability. These properties have led to their use in many industrial applications, for example, in the preparation of the automobile and aerospace components. The convert mold process is typically divided into three main processes: (1) the fabrication of the starting mold coated with an organic binder, (2) the drying process for a period of 1 h at 80 and 200 °C after dipping into a precursor slurry containing a inorganic binder, and (3) the final heat treatment for a period of 1 h at 1000 °C. The starting mold, substrate, shows a secondary shrinkage behavior at above 1000 °C, inducing the shape deformation and dimension change of the mold. Glassification of sodium silicate is insufficient at below 1000 °C, leading to the decrease in the fracture strength of the mold. In addition, the mold for precision casting in industry is pre-heated at about 1000 °C. Therefore, the final heat treatment in the convert mold process is usually performed at 1000 °C. The reaction mechanism during the convert mold process is divided into a hydrolysis and heat treatment stages [5,6] , shown in the following reactions; Hydrolysis reaction: (1) NaOR + H 2 O → ROH + NaOH (2) (RO) 3 Si[O–Si(OR) 2 ] n OR + ( n + 2)H 2 O → ( n + 1)SiO 2 + 2( n + 2)ROH where NaOR, ROH, NaOH, (RO) 3 Si[O–Si(OR) 2 ] n OR, and SiO 2 denote sodium alkoxide, an alcohol, sodium hydroxide, alkyl silicate, and silica, respectively [7] . Sodium alkoxide is hydrolyzed to form sodium hydroxide (by Eq. (1) ), and alkyl silicate is hydrolyzed to form silica and alcohol (by Eq. (2) ). Heat treatment reaction: (3) 2NaOH + SiO 2 → Na 2 O·SiO 2 + H 2 O Sodium silicate (Na 2 O·SiO 2 ) is produced by the reaction between sodium hydroxide and silica at the temperature of about 1000 °C. Sodium oxide (Na 2 O) is used as a network modifier to allow easy formation of a glass phase and to decrease the viscosity of the glass phase [8] . Consequently, the organic binder coated on the mold is converted into the inorganic binder by the reactions shown in Eqs. (1)–(3) . Even though the convert mold process reveals the improved mold collapsibility and thermal stability compared with the conventional mold prepared using a silica binder (shell mold), the hydrolysis reaction in the slurry containing the precursor of inorganic binder means that the atmospheric moisture should be controlled during the process. Therefore, a new convert process using a solid-state binder has been proposed [9] . In this work, molds for precision casting were fabricated using two types of binder system, tetraethyl orthosilicate (TEOS) with the hydrolysis reaction and polydimethyl siloxane (PDMS) without the hydrolysis reaction as silicate precursors and sodium methoxide (NaOMe) as a precursor of Na 2 O. These were studied as functions of dipping time and binder composition in an effort to enhance the fracture strength, achieve a more favorable collapsibility, and improve the thermal and dimensional stability. The characteristics of samples prepared using the new binder systems were measured using various analytical techniques. The relationship between fracture strength and binder composition is discussed based on the microstructures observed before and after the heat treatment. 2 Experimental The new composite binder systems in the convert mold process for precision casting were prepared using TEOS (Sigma–Aldrich Korea, Yongin, Korea) of silicate type and PDMS (Sigma–Aldrich Korea, Yongin, Korea) of siloxane type as the silicate precursors, and NaOMe (Sigma–Aldrich Korea, Yongin, Korea) as the Na 2 O precursor. The sample size used as the starting substrate was 10 mm × 10 mm × 50 mm, which was determined by a commercial organization (Metia Co., Ltd., Changwon, Korea). The samples coated with an organic binder were dipped into the prepared binder systems for periods of 0.5, 1, and 2 h at room temperature. The dipped samples were dried at 80 °C for a period of 1 h, and then heat treated at 1000 °C for a period of 1 h. In this study, drying at 200 °C was not carried out to shorten the processing time. Basic formulations and experimental ranges for preparing molds by converting the organic binder to the inorganic binder are shown in Table 1 . The hydrolysis reaction of the precursors used in this work was carried out by the addition of water at 80 °C for a period of 1 h, and then the samples were dried at 80 °C for a period of 12 h. The difference before and after the hydrolysis reaction was analyzed using a Fourier transform infrared spectrometer (FT-IR, Nicolet, Thermo Fisher Scientific, MA, USA) and an X-ray diffractometer (XRD, Philips X-pret MPD, Model PW3040, Eindhoven, Netherlands). The fracture morphology and microstructure were observed using a scanning electron microscope (SEM, JEOL Model JSM-5610, Tokyo, Japan), and the elemental analysis of the precursors was carried out using an energy dispersive X-ray spectrometer (EDS, energy resolution = 133 eV, Oxford Inst., Oxford, UK). The fracture strength of samples before and after the heat treatment was measured using a universal testing machine (UTM, Instron 5566, Instron Corp., Norwood, MA, USA) in the bending mode at a rate of 0.5 mm min −1 . Tests were carried out at room temperature, and five runs were performed to determine the standard deviation of the strength. 3 Results and discussion 3.1 IR spectra of the binder FT-IR spectra of various precursors, such as NaOMe, TEOS, and PDMS, and the new binder systems (TEOS with NaOMe and PDMS with NaOMe) are shown in Fig. 1 , both before and after the hydrolysis reaction. Fig. 1 (a) shows the FT-IR spectra of NaOMe. The peak intensities at 1400 and 900 cm −1 were conspicuously increased, caused by Na 2 CO 3 created from the hydrolysis reaction of NaOMe. Fig. 1 (b) shows how the TEOS peak was changed after the hydrolysis reaction. The TEOS peak before the hydrolysis reaction had two characteristic bands at 2800–3000 cm −1 and 1000 cm −1 , which were assigned to the C–H stretching and Si–O stretching vibrations, respectively. However, after the hydrolysis reaction, the C–H stretching peak disappeared and the peak arising from the Si–OH group occurring at 3500 cm −1 was observed. In addition, Si–O–Si group bending peak occurring at 470 cm −1 was observed [10] . These results confirm that the TEOS underwent two reactions: (1) the hydrolysis reaction with water, and (2) the condensation reaction between Si–OH molecules after the hydrolysis reaction, which is principally the sol–gel process [11,12] . The characteristic bands arising from PDMS showed the Si–OH stretching peak occurring at 3500 cm −1 , the C–H stretching peak occurring at 2800–3000 cm −1 , the sharp and strong Si–O–Si stretching peaks at occurring at 800 and 1100 cm −1 , and the Si–CH 3 stretching peak occurring at 1250 cm −1 ( Fig. 1 (c)) [13,14] . The PDMS spectrum did not change after the hydrolysis reaction. This suggests that PDMS did not undergo the hydrolysis and condensation reactions, anticipating a high glassification efficiency of the binder system. PDMS has the molecular structure that contains Si–O–Si linkages, whereas TEOS forms these linkages after undergoing the sol–gel process, as shown in Fig. 2 . Therefore, the fracture strength of the mold containing PDMS could be higher than that containing TEOS or that prepared with the conventional binder system. In addition, the new binder system (TEOS + NaOMe) showed the significantly different spectra before and after the hydrolysis reaction as shown in Fig. 1 (d), while the new binder system (PDMS + NaOMe) had a similar spectrum before and after the hydrolysis reaction ( Fig. 1 (e)) except for the peak occurring at 1600 cm −1 resulting from NaOMe. 3.2 XRD analysis XRD profiles of the precursor materials (NaOMe and TEOS) and the new binder systems (TEOS with NaOMe and PDMS with NaOMe) are shown in Fig. 3 after the hydrolysis reaction. NaOMe was converted into Na 2 CO 3 and NaCO 2 H from the NaOH formed by the hydrolysis reaction ( Fig. 3 (a)), and TEOS is changed into amorphous silica ( Fig. 3 (b)). The product from TEOS with NaOMe had almost no diffraction peaks owing to the glass phase formed by the reaction of silica (SiO 2 ) with Na ions ( Fig. 3 (c)), indicating that the glass phase was completely amorphous [15–17] . However, when PDMS was used as the binder material, the crystalline peaks of Na 2 CO 3 with a low intensity were observed. This means that PDMS and NaOMe without and with the hydrolysis reaction, respectively, existed separately in the new binder system ( Fig. 3 (d)). In addition, the difference in the binder systems using TEOS and PDMS as the silicate precursors was more observable in the SEM morphology. 3.3 Morphology and element analysis of precursors The SEM morphology and EDS analysis results of the precursors after the hydrolysis reaction are shown in Fig. 4 . In the EDS analysis ( Fig. 4 (a)), the carbon (C) element from the Na 2 CO 3 molecules proven by the XRD analysis ( Fig. 3 ) was detected, meaning that the NaOH formed by the hydrolysis reaction was changed into Na 2 CO 3 by reacting with CO 2 in the ambient air. The relatively large SiO 2 particles were formed by the condensation reaction between Si–OH molecules resulting from the hydrolysis reaction of Si–O–CH 3 , as shown in Fig. 4 (b). In addition, Fig. 4 (c) and (d) shows different morphologies owing to the different chemical reactions of TEOS and PDMS. Namely, particles in the binder system containing TEOS and NaOMe had a similar shape to those of neat TEOS, while particle morphology in the binder system containing PDMS with NaOMe resembled that of NaOMe. 3.4 Reaction depth and fracture morphology The variation of reaction depth as a function of the dipping time is shown in Table 1 and Fig. 5 . The reaction depth was measured using samples that had been just dried and heat treated after dipping into the binders prepared with a unique condition. In the case of the conventional binder (Run 1 series), as the dipping time was increased from 0.5 to 2 h, the reaction depth of the binder increased from about 1.49 to 2.57 mm (see Fig. 5 (a)). Namely, this means that the center of samples was empty after the heat treatment, inducing a significant decrease in the strength of the sample compared with the untreated sample. However, in the new binder systems (Runs 3 and 4 series), except for Run 2 ( Fig. 5 (b)), the reaction was fully built up in the whole region of sample during the heat treatment, indicating that all the samples after the heat treatment had a higher strength. This suggests that the new binder systems are more effective in diffusing the binder into the sample and in reducing the processing time compared with the conventional binder system. 3.5 Fracture strength The fracture strength of samples with different binder compositions and dipping times was investigated, and the results are shown in Fig. 6 . In general, the fracture strength of samples after the heat treatment should be a higher value than that of the samples before the heat treatment due to the glassification of silicate by the reaction of SiO 2 with Na ions during the heat treatment. However, the conventional binder system showed the fracture strength that decreased sharply after the heat treatment owing to a large unreacted part inside the sample induced by the narrow reaction depth. However, in the case of the new binder systems containing PDMS (Runs 3 and 4), the fracture strength after the heat treatment was significantly increased compared with the conventional binder system, caused by the high glassification efficiency of PDMS that did not undergo the sol–gel process and by the relatively deep reaction depth. Except for the conventional binder system, the fracture strength decreased slightly as the dipping time increased due to agglomeration and reverse diffusion. The new binder system with 7.6 wt% PDMS (Run 3-1) showed the highest nominal strength of 8 MPa, while additional PDMS did not affect the fracture strength. 3.6 Surface morphology of particles Typical SEM morphologies of particles in the fracture surfaces of samples prepared by Run 2 before and after the heat treatment are shown in Fig. 7 as a function of dipping time. Before the heat treatment, cracks were observed at the interface between particles (denoted by the arrows in Fig. 7 (a-1) and (c-1)), and on the surface of particles (denoted by the arrow in Fig. 7 (b-1)), whereas these cracks disappeared after the heat treatment because of the formation of the glass phase during the heat treatment. All particles were well coated, regardless of the dipping time. SEM morphologies of particles in the fracture surfaces of samples dipped into various binder compositions for 2 h are shown in Fig. 8 before and after the heat treatment. Generally, the glassification of inorganic binder is important factor to increase the fracture strength and thermal stability of the mold. As shown in Fig. 8 , the glass phase was well developed at the interface ( Fig. 8 (c)) and/or on the surface ( Fig. 8 (d)) of particles prepared by the binder system containing PDMS (indicated with arrows in Fig. 8 ). However, the glass phase was not fully developed at the interface and/or on the surface of particles prepared by the binder system without PDMS, especially in the case of conventional binder system ( Fig. 8 (a)). It means that siloxane type without the sol–gel reaction has a higher glassification efficiency than silicate type with the hydrolysis and condensation reactions, especially than the conventional binder system. It is verified that the glassification efficiency strongly affected the fracture strength of samples, showing the higher strength in samples prepared by the new binder system containing PDMS. 4 Conclusions The new binder systems that increased fracture strength and reduced processing time were successfully developed using precursor materials, such as tetraethyl orthosilicate (TEOS), polydimethyl siloxane (PDMS), and sodium methoxide (NaOMe). TEOS was converted into silica (SiO 2 ) by a sol–gel process, but PDMS did not undergo any chemical reaction, highlighting the difference between PDMS and TEOS in terms of the final fracture strength resulting from the glassification efficiency. The fracture strength of samples with the new binder systems mostly increased after the heat treatment, whereas the fracture strength decreased sharply for the conventional binder system due to the untreated regions caused by the relatively narrow reaction depth. The new binder system with 7.6 wt% PDMS showed the highest nominal strength of 8 MPa, due to the high glassification efficiency of PDMS that did not undergo the hydrolysis and condensation reactions. The SEM morphology of particles was independent of the dipping time, but the binder composition affected the glassification efficiency. The fracture strength could be controlled by changing the molecular structure of binder and the binder composition. Acknowledgements This work was supported by the Power Generation & Electricity Delivery ( R-2007-1-003-02/2009T100200025 ) and Human Resources Development ( 2007-P-EP-HM-E-02-0000 ) of the Korean Institute of Energy Technology Evaluation and Planning (KETEP) grants funded by the Korean Ministry of Knowledge Economy. References [1] Y.A. Meng B.G. Thomas Metall. Mater. Trans. 34B 2003 707 [2] M. Şimşir L.C. Kumruoğlu A. Őzer Mater. Designs 30 2009 264 [3] H. Saridikmen N. Kuskonmaz Ceram. Int. 31 2005 873 [4] J. Jiang X.Y. Liu Mater. Process Technol. 189 2007 247 [5] M. Barsoum Fundamentals of Ceramics 1997 McGraw-Hill Seoul [6] W.D. Callister Materials Science and Engineering: An Introduction 1997 Wiley New York [7] S. Ege Organic Chemistry 1994 D.C. Heath and Company Toronto [8] P.G. Shewmon Diffusion in Solids 1963 McGraw-Hill New York [9] N. Sasaki Found. Manage. Technol. Feb. 2009 21 [10] X. Shi S. Xu J. Lin S. Feng J. Wang Mater. Lett. 63 2009 527 [11] Y. Chen Y. Hong F. Zheng J. Li Y. Wu L. Li J. Alloys Compd. 478 2009 411 [12] J.L. Gurav A.V. Rao A.P. Rao D.Y. Nadargi S.D. Bhagat J. Alloys Compd. 476 2009 397 [13] M. Anbia M. Lashgari Chem. Eng. J. 150 2009 555 [14] W. Xue A. Bandyopahyay S. Bose Acta Biomater. 5 2009 1686 [15] G.F. Terry Lay M.C. Rockwell J.C. Wiltshire C. Ketata Ceram. Int. 35 2009 1961 [16] P.K. Sahoo R. Samal S.K. Swain P.K. Rana Eur. Polym. J. 44 2008 3522 [17] A.K. Sandhu W. Singh O.P. Pandey Mater. Chem. Phys. 115 2009 783
更多查看译文
关键词
Ceramics,Inorganic compounds,Heat treatment,Mechanical properties
AI 理解论文
溯源树
样例
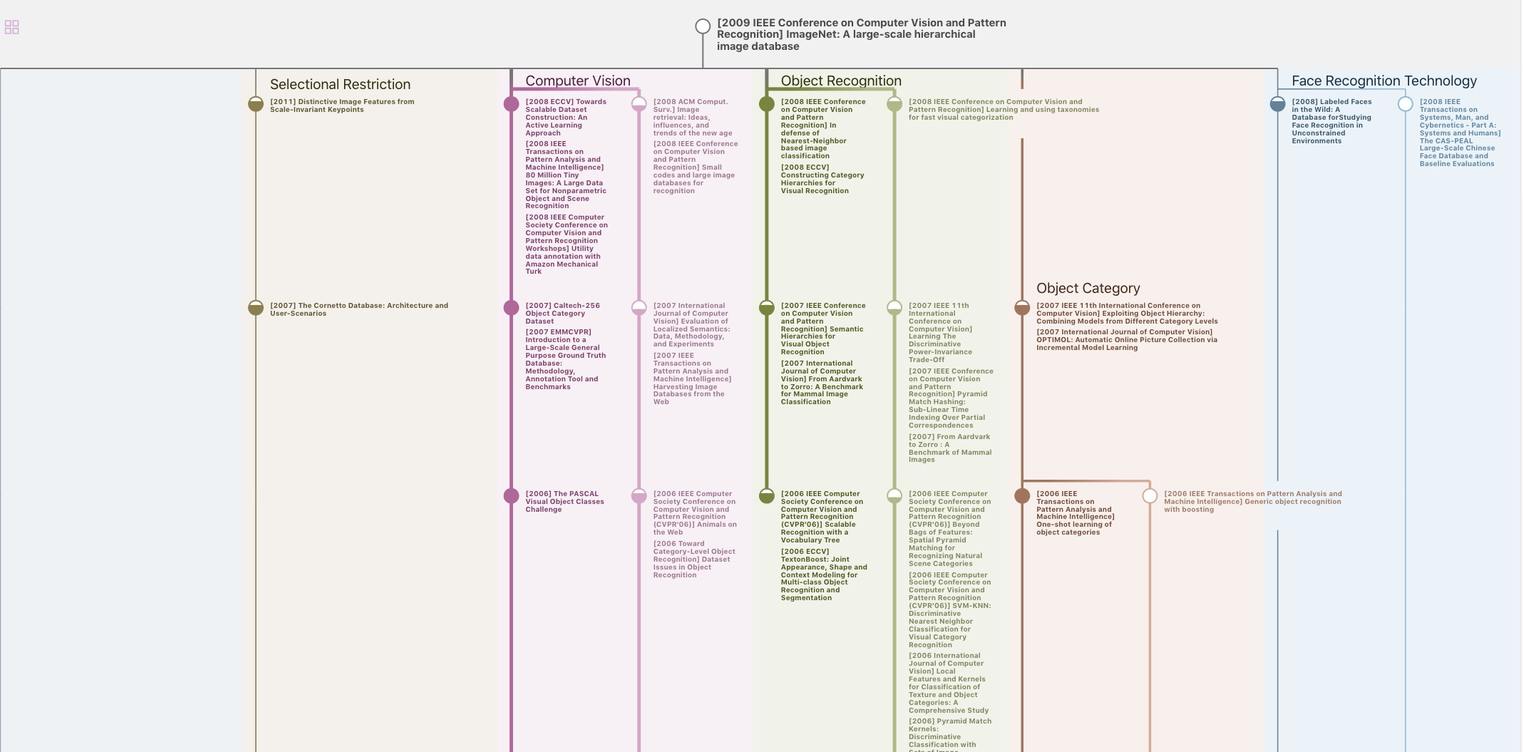
生成溯源树,研究论文发展脉络
Chat Paper
正在生成论文摘要