30mm wide process of GdBCO PLD/clad-type textured metal substrates
Physica C: Superconductivity and its Applications(2011)
摘要
Gd 1 Ba 2 Cu 3 O x (GdBCO) coated conductors using bi-axially textured clad-type substrates have been developed for high temperatures superconducting (HTS) power cables. In this project, large amount of coated conductors (CCs) are necessary for the several tests of basic properties of HTS power cables and the fabrication of a 15 m long 3-in-one HTS model cable. In order to ensure an adequate amount and properties of coated conductors, the stable manufacturing technology and the high production rate at each process are required. In this report, we have newly installed a high power laser of 300 W for the PLD system, resulting in improvement of the manufacturing stability and the deposition rate for GdBCO film. In addition, we have optimized target–substrate distance in PLD process, and the uniformity of I c distribution across 30 mm wide tapes were remarkably improved. Furthermore, the surface morphology of buffer layers were enhanced by optimizing the deposition condition using electron beam (EB) evaporation method, and the maximum I c value for a short sample has achieved 497 A/cm at 77 K in the self-field. Based on these progresses, we are currently developing the stable manufacturing process for long CCs with over 400 A/cm. Keywords GdBCO coated conductors High temperature superconductors PLD method 1 Introduction Recently, extensive research and development of REBCO (RE: rare earth systems) coated conductors (CCs) for several power applications have been conducted around the world [1] . In Japan, a national project for development of materials & power application of CCs has been started since 2008, and we have been fabricating GdBCO CCs for a 15 m long, 5 kA, 66 kV class 3-in-One HTS model cable system as a part of this project [2,3] . This HTS cable is characterized by its large capacity of 570 MVA, low AC loss of less than 2 W/m/phase at 5 kA rms , and the small cable diameter of 150 mm, and the HTS cable will have superior performance such as the largest both capacity and transport current density as well as the smallest AC loss of any other power cables in the world. The 3-in-One HTS model cable is composed of three cables placed in one cryostat, and each cable is fabricated by assembling a number of 4 mm wide GdBCO tapes along a copper core. In order to meet the requirement for the cable’s performance, it is necessary to routinely produce long CCs with the high I c value of more than 400 A/cm (=160 A at 4 mm wide tape). Moreover, long CCs more than 10 km in total are required to develop the element technologies in addition to the HTS cable itself in this project; therefore, establishing stable and rapid production process of CCs with high I c is also important as a basis of developing the HTS cable. We have adopted a wide tape approach using 30 mm wide substrates to improve the production throughput, and then the 30 mm wide tapes are cut into 2 mm or 4 mm wide tapes using a slitter. Moreover, we have developed the deposition process for buffer layers and the superconducting layer by installing a 300 W new laser for PLD system and optimizing the deposition condition of a seed layer using electron beam (EB) evaporation method. This paper describes our 30 mm wide manufacturing process and the present progress status of development of CCs for the HTS cable. 2 30 mm wide manufacturing process of GdBCO tapes The architecture of the GdBCO coated conductor is shown in Fig. 1 . The tapes are composed of a 30 mm wide textured clad-type metal substrate, a multi-buffer layer of CeO 2 /YSZ (yttrium stabilized zirconia)/CeO 2 , a GdBCO superconducting layer, Ag and Cu protection layers. The clad-type textured metal substrate, which consists of a thin bi-axially textured Ni layer on a non-crystalline stainless tape, was produced by the conventional cold-rolling and heat treatment processes. The typical value of in-plane alignment, a full width at half maximum (FWHM) of XRD scan for Ni(1 0 0), is 4.6°. Moreover, the clad-type substrate has less magnetism and higher mechanical strength than typical Ni-alloy textured substrates; therefore, coated conductors using the clad substrate are suitable for AC applications and also have advantage of its low AC loss [4] . The multi-buffer layers of CeO 2 /YSZ/CeO 2 are deposited on 30 mm wide substrate by a reel to reel RF sputtering or EB evaporation. The first CeO 2 layer deposited on the substrate plays a role of a seed layer. The second YSZ layer prevents Ni in the substrate from the inter-diffusion and the reaction to superconducting layer, which can degrades I c values. The third CeO 2 layer acts as the relaxation of lattice-mismatch between the YSZ layer and the superconducting layer, and showed around 4.6° of in-plain grain alignment (Δ ϕ ) across the 30 mm tape width, which was evaluated by a full width at half maximum (FWHM) of X-ray ϕ scan for CeO 2 (1 1 1) pole. The crystallinity of the third CeO 2 layer was analyzed by X-ray diffraction of θ − 2 θ , showing highly uniform crystallinity over the tape width with the cube textured ratio of I (2 0 0)/[ I (2 0 0) + I (1 1 1)] = 99% [5] . The GdBCO film is fabricated on the CeO 2 /YSZ/CeO 2 buffer layers by a reel to reel PLD system using the 300 W Kr-F ( λ = 248 nm) excimer laser. The pulse energy and the repetition rate are 1 J and 300 Hz, respectively. The deposition is repeated 6 or 8 times with the tape moving at a speed of 24 m/h for each layer under 10 Pa of the O 2 partial pressure, that is, the actual manufacturing speed for PLD process was 3–4 m/h for 30 mm wide tapes. After the deposition of the GdBCO film, Ag layer is sputtered as a stabilization layer. Finally, the 30 mm wide CC is slit into 4 mm or 2 mm tapes and electroplated with copper as a protection layer. In slitting process, rectangular blades are adopted to reproducibly slit CCs, and the I c maintenance ratio of CCs after slitting them was confirmed to be over 90% in both cases of 2 mm and 4 mm wide tapes. 3 Status of manufacturing process 3.1 Enhancement of surface morphology of buffer layers Through the project started since 2008, production process of 100 m class CCs with typical I c of 250 A/cm at 77 K was successfully developed. However, in order to demonstrate the HTS model cable, long CCs with high I c of over 400 A/cm is necessary. For development of long GdBCO coated conductors with high and uniform I c properties, improvements of deposition process for buffer layers and superconducting layer are important, and it is well known that the I c property is strongly affected by surface roughness and crystallinity of buffer layers. Fig. 2 shows an AFM (Atomic Force Microscope) image of a surface morphology of a cap-CeO 2 layer. As shown in Fig. 2 a, surface of the cap layer was very rough and small precipitates with sub-micron scale were observed. This surface was resulted from a number of micro-cracks of the seed CeO 2 layer deposited by RF-sputtering, and these problems might be considered to degrade flatness and crystal orientation for buffer layers. From the investigation of the deposition condition, it turned out that the micro-cracks of the seed layer are related to film thickness and deposition temperature. Moreover, it is also considered that the micro-cracks can be caused by a columnar CeO 2 seed layer growth mode. Therefore, we applied EB evaporation method for seed layer deposition to reduce the columnar growth and successfully obtained a flat seed layer without any cracks by optimizing the deposition condition. The thickness of the seed layer was also reduced from 140 nm to 100 nm. Fig. 2 b shows a surface morphology of cap CeO 2 layer deposited on the improved seed layer. The surface became significantly flat, and the average roughness measured by AFM was improved from 9 nm to 5 nm. 3.2 Development of PLD process for high I c GdBCO superconducting layers In our 30 mm wide manufacturing process, PLD process is critically important in determining productivity and I c values of CCs. A 300 W excimer laser for PLD system was newly installed for improving the productivity, and PLD process made excellent progress in I c properties and uniformities of I c distributions across the tape width. With installation of the 300 W laser, the plume size was enlarged up to around 10 cm in diameter at the tape surface when the pulse energy and the repetition rate are 1 J and 300 Hz, and the deposition rate was also greatly increased. The thickness for a single deposition is around 0.35 μm at the tape moving speed of 24 m/h. Furthermore, the relationship between the I c value and the tape moving speed in PLD process was investigated, and it turned out that the high I c values can be obtained by increasing the tape moving speed to 24 m/h. Fig. 3 shows the I c values with previous and improved deposition processes as a function of the GdBCO film thickness at 77 K. A dotted line indicates the I c property of GdBCO films fabricated by the previous process with the laser frequency of 180 Hz and the tape carrying speed of 12 m/h. The I c property of this process tended to be saturated at 250 A/cm. A solid line indicates the I c value of GdBCO films, which was deposited by using the 300 W laser, on improved crack-free buffer layers. As can be seen in Fig. 3 , I c property has been greatly improved, and achieved 497 A/cm w at 77 K for a short sample ( J c = 1.78 MA/cm 2 ). The typical I c properties were around 250 A/cm when using 1 J, 180 Hz laser; therefore, this result reveals that the I c value has almost doubled by applying improved seed layers and using 1 J, 300 Hz laser for PLD process. Moreover, we applied this improved PLD process and crack-free buffer layers to the manufacturing process for long CCs, and successfully obtained a 22 m long GdBCO tape with high I c of more than 160 A in 4 mm width ( = over 400 A/cm w) at 77 K as shown in Fig. 4 . The I c distribution along the 22 m tape was measured at 1.5 m intervals by a reel to reel four-probe I c measurement. Thus, we succeeded in developing manufacturing process to meet the requirement for HTS model cable. 3.3 Improvement of I c distribution across 30 mm wide GdBCO tape In the phase of volume production, not only the I c values but also the uniform I c distribution across the 30 mm wide tapes are very important in terms of the fabrication yield. We investigated correlation between the target-to-substrate distance ( D ) and the thickness of GdBCO films, and optimized the target-to-substrate distance to improve the I c distribution across the tape width. In addition, the relationship between the target-to-substrate distance and surface morphology was also investigated. The target-to-substrate distance was adjusted such as D = 48 mm, 53 mm, 58 mm, and 63 mm. Fig. 5 shows J c values of four times deposited GdBCO tapes as a function of the distance between target and a substrate. As can be seen in this figure, a GdBCO film deposited at D = 58 shows the highest J c value of other distance conditions. From the film composition measured by EDX (Energy Dispersive X-ray analysis), it was recognized that the composition ratio gradually shifted from Cu-rich to Gd-rich with increasing the distance between the target and tapes. One of the possible reasons of Gd-rich composition at long target and tape distance such as D = 58 mm, 63 mm, is due to the scattering effect of oxygen because barium and copper are lighter than Gd and easily scattered compared with Gd [6] . The surface morphologies of GdBCO films deposited at each target-to-substrate distance are shown in Fig. 6 . It can be seen that a number of precipitates are observed at D = 48 mm, which are likely to be of copper composition, and the surface morphology became flat by increasing the distance. Fig. 7 shows the I c distribution in width direction of a 30 mm wide 10 cm long GdBCO tape deposited at D = 53 mm and D = 58 mm. In this figure, the bars and the solid line indicate the I c distribution and the film thickness, respectively. The deposition at D = 53 mm is the previous process, and D = 58 mm is the improved process. The GdBCO tape was cut into six tapes with 5 mm in width, and then we conducted the four-probe I c measurement of each tape. The left side of Y -axis as shown in Fig. 7 indicates I c values normalized by the maximum I c in the 30 mm wide tape for ease of comparison between the two samples, and the right side of Y -axis indicates the thickness of GdBCO films. As can be seen in this figure, the film deposited by the previous process shows inhomogeneity of I c distribution. On the other hand, the I c distribution of a film deposited at D = 58 mm was remarkably improved because of the uniform film thickness, which is one of the effects of increasing the distance between the target and tapes. With this improvement, it is expected that the production yields greatly improved. However, steep I c degradation was still observed on the right side of the edge in both samples. We investigated the composition distribution across the tape with EDX, and it revealed that there was an increasing tendency of the deviation from stoichiometry of Gd123 toward the right side of the sample as shown in Fig. 8 . In this figure, the elemental ratios of Gd/Gd, Ba/Gd, and Cu/Gd based on the total film composition for GdBCO films across the tapes are shown. At the right side of the tape edge, in particular, the high Gd-rich composition ratio of Gd:Ba:Cu = 1:1.75:2.5 was observed, and this result was considered as the cause of I c degradation at the edge. One of the reasons of this inhomogeneous composition is the spatial distribution of each element inside a plasma plume generated by irradiating a Gd123 target with the excimer laser. The development of the uniform I c distribution across the tape is currently underway for further improvement of the fabrication yield. 4 Improvement of overall I c distribution A histogram of the I c for a population of 4 mm wide CCs produced in 2009 and 2010 is shown in Fig. 9 . The piece length of CCs was about 20–100 m. Whereas the major I c of 4 mm wide CCs produced in 2009 was 60–90 A, the I c of CCs made in 2010 increased to 120–150 A. That is, the base performance of CCs has been improving with the development of manufacturing process in buffer layers and superconducting layer. We, however, still have a challenge for long length manufacturing process for 500 A/cm w level CCs. Therefore, we are now focusing on the development of the stable process for long CCs. 5 Conclusion The manufacturing process of 30 mm wide GdBCO coated conductors were greatly improved by installing 300 W excimer laser for the PLD process and by developing the seed layer using EB evaporation method. The maximum I c for a short sample has achieved 497 A/cm ( J c = 1.78 MA/cm 2 ) at 77 K under the self-field, and we also succeeded to fabricate a 22 m long 4 mm wide GdBCO tapes with the high I c of over 160 A in 4 mm width (>400 A/cm w). In addition, the I c distribution in width direction was successfully improved with the effect of the uniformed thickness which is achieved by adjusting the distance between the target and the substrate. Based on these progresses, we are currently focusing on the development of the stable process for 500 A/cm level long CCs as a next challenge. Acknowledgments The authors would like to thank Dr. Yuh Shiohara, Dr. Teruo Izumi, Dr. Yutaka Yamada, Dr. Yuichi Yamada, Dr. Noriko Chikumoto, Dr. Akira Ibi, Dr. Takato Machi at the Superconductivity Research Laboratory, ISTEC, for their support. This work was supported in part by the New Energy and Industrial Technology Development Organization (NEDO) as the Project for Development of Materials & Power Application of Coated Conductors, M-PACC. References [1] T. Izumi Y. Shiohara Physica C 470 2010 967 [2] Y. Shiohara N. Fujiwara H. Hayashi S. Nagaya T. Izumi M. Yoshizumi Physica C 469 2009 863 [3] T. Minamino M. Ohya H. Yumura T. Masuda T. Nagaishi Y. Shingai X. Wang H. Ueda A. Ishiyama N. Fujiwara Physica C 470 2010 1576 [4] T. Nagaishi Y. Shingai M. Konishi T. Taneda H. Ota G. Honda T. Kato K. Ohmatsu Physica C 469 2009 1311 [5] T. Yamaguchi H. Ota K. Ohki M. Konishi K. Ohmatsu Physica C 470 2010 1271 [6] K. Develos-Bagarinao H. Yamasaki Y. Nakagawa K. Endo Physica C 412–414 2004 1286
更多查看译文
关键词
GdBCO coated conductors,High temperature superconductors,PLD method
AI 理解论文
溯源树
样例
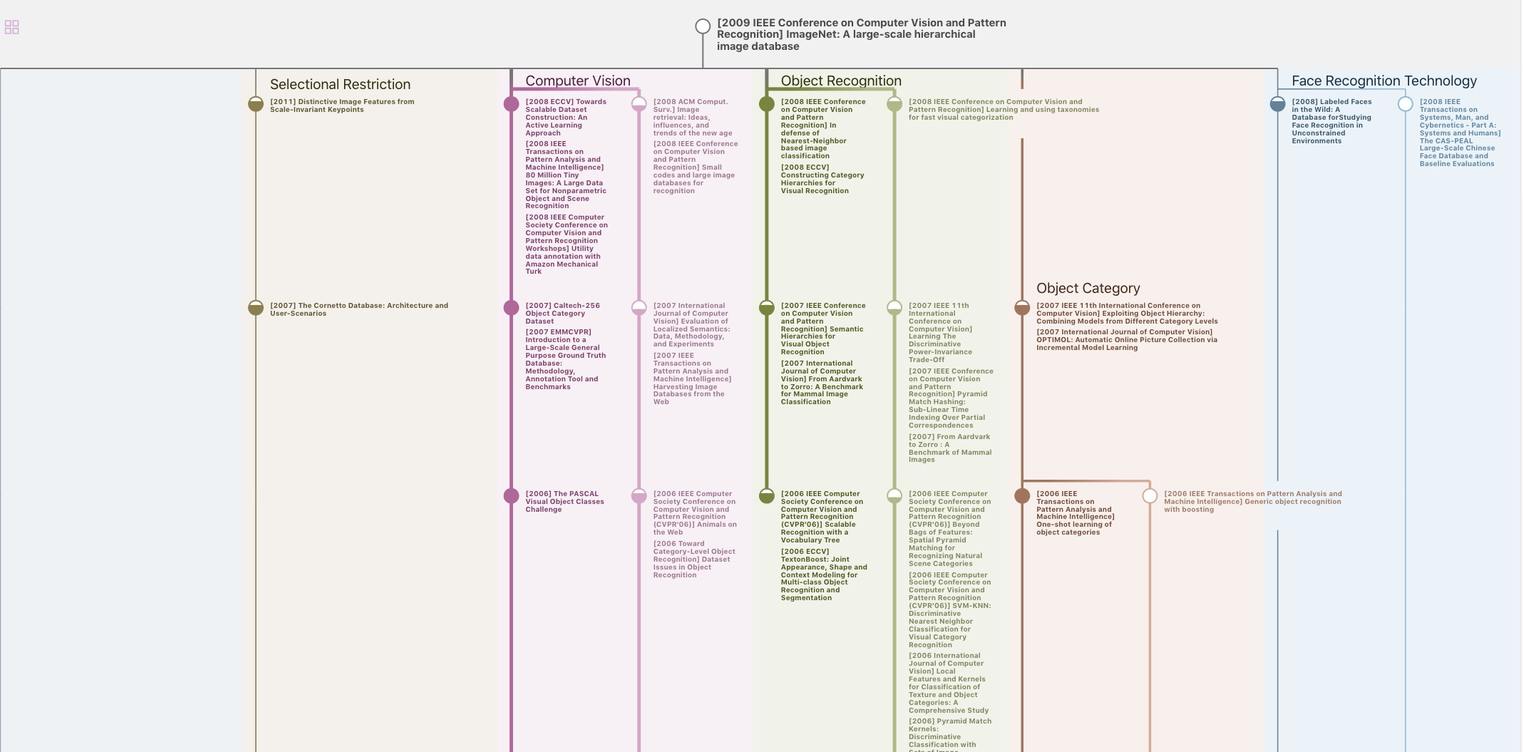
生成溯源树,研究论文发展脉络
Chat Paper
正在生成论文摘要