Carburization of W- and Re-rich Ni-based alloys in impure helium at 1000°C
Corrosion Science(2011)
摘要
Research highlights ► This work investigates the surface and bulk stability of W- and Re-rich Ni-based alloys under carburizing/oxidizing conditions (1000 °C) in order to understand the fundamental mechanisms of material degradation due to impurities in helium environment of the very high temperature helium-cooled reactor (VHTR). ► Depending on the alloy composition, carbides of type M 6 C, M 7 C 3 or M 23 C 6 were observed, with a maximum carbon pickup between 0.06 and 0.12 wt.%. Alloys with high W content exhibited M 6 C type carbides, whereas high Cr and low W alloys formed Cr-rich M 23 C 6 carbides. High additions of Re stabilized the M 23 C 6 phase due to its high solubility in these chromium-rich carbides. ► A continuous film of contiguous carbides (M 6 C and M 23 C 6 ) was observed in the grain boundaries; this is likely to be detrimental to the ductility and creep properties. ► During the first 50 h exposure, carbides were observed on the alloy surface as well as in the bulk with carbides precipitating in the grain interior and on the grain boundary. The (transient) surface carbides oxidized after prolonged exposure (100–225 h) forming stable Cr 2 O 3 oxide on the alloy surface. ► The work is particularly relevant to the development of strategies towards improvement of Ni-based alloys for intermediate heat exchangers (IHX) for service at 1000 °C in impure-He environment of the Next Generation Nuclear Plant (NGNP). Abstract The surface and microstructure stability of experimental W- and Re-rich Ni-based alloys in an impure-helium environment containing only CO and CO 2 as impurities (ppm level) have been investigated at 1000 °C. All the alloys carburized during 50 h of exposure, and, depending on the alloy composition, different carbides of the type M 6 C, M 7 C 3 and M 23 C 6 formed on the alloy surface, in grain interiors and at grain boundaries. Microprobe analysis and Calphad-based calculations indicated that the chromium carbides (particularly Cr 23 C 6 ) were enriched by rhenium. Extended exposure (225 h) led to the disappearance of surface transient carbides and the growth of surface oxide Cr 2 O 3 occurred. Keywords A. Superalloys C. Carburization C. Oxidation 1 Introduction The critical structural components in the helium gas-cooled high-temperature reactor, such as heat exchanger and primary-to-secondary piping, are predicted to operate at 1000 °C in corrosive environments for extended periods of time [1–6] . Several Ni-base alloys such as Inconel 617, Haynes 230, Alloy 800H, Alloy XR and the Ni–Cr–W have been considered as potential high-temperature materials for such reactor applications [7–22] . The principles of strengthening and creep-resistance in these alloys involve either precipitation hardening by ordered γ′ (Ni 3 Al) phase or solid solution strengthening by Mo, Ru, Ta, W and Re refractory elements, or both [23–26] . Due to the higher density of some of these elements, limited quantities are used in alloys for turbine airfoil applications. However, since these elements possess very low diffusion coefficients and have been shown to be quite effective in improving creep resistance [25,27,28] , higher levels of refractory alloying additions would be desirable for ground-based reactor applications. It should be noted that two-phase γ/γ′ Ni-alloys may not be suitable for long service time applications due to the likelihood of strength degradation via γ′ coarsening. Therefore, alloys typically selected for the reactor applications are single-phase γ-Ni and derive their strengthening from solution hardening. Due to the low amount of Al (in order to avoid γ′ precipitation), the materials are alloyed with sufficient Cr in order to form chromia (Cr 2 O 3 ) at high temperatures. In the current study, four experimental Ni-based alloys solid solution strengthened by Co, Mo, Re and W were utilized. Additionally, Al and Cr were added for protective surface oxide growth, although the alloys are predominantly chromia (Cr 2 O 3 ) formers. Unlike the alloys such as Inconel 617 (20–25 wt.% Cr), the Cr content has been reduced to ∼12–15 wt.% in order to avoid brittle topologically close packed (TCP) phase formation in combination with high Re and W. After steady-state operation, the helium coolant in secondary heat exchanger loops contains impurities such as H 2 /H 2 O, CO/CO 2 , CH 4 and N 2 at low concentration levels (ppm) due to degassing, leakages and reactions (oxidation and cracking) from the graphite core and among other materials [5,29–33] . The gas impurities typically set the oxygen and carbon potentials in the impure helium environment; an understanding of both the thermodynamics and kinetics of the gas–metal interactions are therefore, important for predicting the alloy degradation modes. It has been shown in several studies that gas (impurity) – metal reactions occur in several Ni-based alloys and, depending on the impurity type/concentration, temperature and alloy chemistry, the alloy can undergo degradation in its mechanical properties due to internal/surface oxidation, carburization, or decarburization [9,14,34,35] . Decarburization can lead to reduced creep strength due to depletion of carbides at grain boundaries while carburization can cause embrittlement of the components. A slow-growing protective surface-oxide layer is desirable at high temperatures to inhibit the diffusion of impurities into the alloy from the helium environment. However, experimental investigations have shown that a specific degradation mechanism exists that causes the destruction of the chromia layer via reaction with carbon (or carbide) above a critical temperature (>900 °C) with a concomitant release of CO gas [9,14,34,35] . In fact, decarburization of Ni–Cr–W alloys, similar in composition to the alloys studied here, has been shown to occur at 1000 °C in a He + 15 ppm CO + 1.5 ppm CO 2 environment [6] via a chromia-assisted decarburization reaction Cr 2 O 3 (s) + 3 C alloy (s) → 2Cr (s) + 3CO (g). According to this reaction, the surface oxide (Cr 2 O 3 ) is reduced by carbon in solid solution, thus eliminating the protective surface oxide. The current work focuses on conditions where carburization, rather than decarburization, occurs. The objective of the current research is to study the stability of Ni-based alloys, solid solution strengthened with high levels of refractory elements W and Re, in impure helium atmospheres containing He + 680 ppm CO + 1.5 ppm CO 2 (high CO content) at 1000 °C. Unlike typical commercial alloys, the experimental alloys did not initially contain any carbon. Additional goals were to: (1) Determine the carburization characteristics of Ni–Cr–W-based alloys by determining the surface and bulk stability of the γ-phase in a He–CO–CO 2 environment. (2) Identify the effect of alloying additions on the type and stability of the carbides. (3) Determine the surface oxide stability during continued exposure to impure He environment. 2 Materials and methods 2.1 Processing and composition Four experimental multi-component Re- and W-rich Ni-base superalloys (designated A2, A6, A8 and A9) were chosen for carburization experiments. The experimental alloys were melted using a Crystalox (Crystalox Ltd., Oxfordshire, UK) induction levitation furnace under an argon atmosphere. Nickel in the form of pure (99.99%) metal pieces was melted to produce a nickel ingot. Subsequently, a compacted powder charge containing the alloying elements was melted together with the nickel ingot followed by a final addition of aluminum. All the powders of alloying elements were obtained from Alfa Aesar (Ward Hill, MA) at the highest purity available. The final ingots measured typically between 75 and 85 g and were melted twice to minimize elemental segregation. The ingots were then encapsulated in argon backfilled quartz tubes and homogenized at 1325 °C for 36 h followed by water quenching. The grain sizes of the alloys subsequent to homogenization were in the range of 500–1000 μm. The nominal and the measured (by EMPA analysis) compositions of the individual alloys are listed in Table 1 . It should be noted that the amounts of refractory elements (Mo, W and Re) used in the current study are nearly twice as in the second-generation superalloys (René N5, [26] ). Compared to the experimental alloys, Inconel 617, a potential candidate for the heat-exchanger components, contains only ∼8–10 wt.% refractory (Mo). The liquidus and solidus temperature of each alloy was determined from DTA heating curves, obtained with a SETARAM SETSYS 18 DTA unit at a scanning rate of 5 °C/min using 3 mm diameter × 4 mm height cylindrical specimens and weighing ∼300 mg, Fig. 1 a. The addition of Mo, Re and W led to increased solidus ( T s ) and the liquidus ( T l ) temperatures compared with values for a commercial alloy Inconel 617 (1354.3 and 1385.4 °C for solidus and liquidus, respectively), thus potentially providing additional high-temperature capability. 2.2 Experimental procedures and specimens Experiments were conducted in a specially designed system that allowed reliable control of impurity levels (CO and CO 2 ) during the entire experiment. The design of the high-temperature environmental chamber is discussed in detail elsewhere [36] and is briefly summarized below. Samples measuring 6 × 6 × 1.2 mm were polished to 1.0 μm surface finish cleaned in a mixture of acetone and methanol followed by deionized water and placed in quartz tubes inserted into a high-temperature furnace, with all the sample surfaces in contact with the flowing helium gas mixture. Before the experiment, high purity (99.9999%) N 2 and He gas were used to flush the atmospheric air in the quartz tubes. Exposures to a gas mixture containing He + 680 ppm CO + 1.5 ppm CO 2 were conducted at a steady rate of 70 cm 3 /min. Subsequently, the samples were inserted into the high-temperature zone (1000 °C) of the furnace from the cold zone of the quartz tube for up to 225 h. A gas chromatograph (Perkin Elmer Clarus 500) equipped with a discharge ionization detector (DID) was used to analyze the gas chemistry during the entire duration of the experiment. For each alloy, a total of four samples were used for the study and at the end of specified time of exposure, separate samples were removed from the hot-zone to the cold-zone of the furnace. Post experiment, the samples were analyzed for their weight change using a microbalance (precision of 10 μg). Microstructures were characterized with a SEM (Philips XL30 FEG). Composition profiles of the alloys were measured by electron microprobe analyzer (EMPA, CAMECA SX100); the accelerating voltage and beam current were set at 20 kV and 10 nA, respectively. A Rigaku Cu K α X-ray diffractometer was used in θ –2 θ mode at 40 kV and 100 mA to obtain X-ray peak profiles. 1 Since the overarching goal of the research work is to study the effect of carburization conditions on the strength and ductility of the alloy, therefore, one of the main objectives was to identify the new precipitate phases and how they modify the microstructure. Even though TEM (EELS) analysis would provide valuable information regarding the carbide/oxide phases, due to the limited amount of testing material, TEM and/or XPS surface characterization were considered beyond the scope of the current work. XRD and microprobe analysis were deemed appropriate to identify the nature and chemistry of the phases. 1 3 Results 3.1 Weight change kinetics The weight change of the alloys as a function of time during exposure to the gas of composition He + 680 ppm CO + 1.5 ppm CO 2 at 1000 °C is shown in Fig. 1 b. In general, all four alloys exhibited parabolic weight change kinetics during exposure; this is consistent with the observed kinetics of carburization of several high-temperature alloys that follow a parabolic law, indicative of a diffusion controlled process [22,37–40] . Although alloy A2 showed greater weight gain during the first 50 h exposure, alloy A6 continued to gain weight at a faster rate compared to all other alloys and followed the parabolic trend until 225 h. As mentioned earlier, none of the alloys tested contained any carbon prior to the exposure in carburizing conditions. Therefore, the weight increase should necessarily occur due to intake of carbon and oxygen through the formation of carbide and oxide, respectively. The following sections discuss, in order, the evolution in surface microstructure as well as the bulk stability of the alloy in terms of the formation and disappearance of carbide and/or oxide phases. 3.2 Surface carburization/oxidation Backscattered SEM images of the surface of all four alloys are shown in Fig. 2 a–d after carburization for 25 h in impure helium atmosphere. Based on the XRD data ( Fig. 3 ) all four alloys formed carbide phases on the alloy surface: M 7 C 3 type carbides for alloy A2, M 23 C 6 -type for alloys A6 and A9 and M 6 C-type for alloy A8. The peak-intensity in Fig. 3 has been normalized and plotted as ( I / I max ) 1/2 in order to facilitate direct comparison between different samples. The surface carbide was in the form of discrete blocky particles with irregular facets and typically measured between 2 and 5 μm, although many contiguous carbides seem to have coalesced and appeared larger. Similar carbide morphology has been observed in W-rich Haynes 556 (Fe–Cr–Ni–Co) alloy [37] . While a high density of surface carbides was observed, they were distributed non-uniformly, with some grains showing a low density of carbides, Fig. 2 a. The SEM image in Fig. 2 a has been obtained by tilting the sample to 45° such that both the surface as well as the cross-section can be observed together; the secondary electron (SE) image is shown in the inset. The carbide growth is clearly different on either side of the grain boundary. Surrounding the carbides, a thin non-continuous layer of aluminum oxide was also observed after 25 h exposure to the impure helium environment. As seen in Fig. 2 a, the alumina also forms as internal oxide precipitates beneath the surface and protruding into the substrate. It is a well-known phenomenon in Ni–Cr–Al-based alloys with high Cr and low Al content, wherein, during high temperature oxidation, the alloys form external chromium oxide and internally oxidize aluminum [41] . This aluminum oxide resembles ‘finger’ shaped protrusions or precipitates in cross-section. The Al 2 O 3 phase was not detected in the XRD spectra ( Fig. 3 ) due to the following reasons: (a) although the carbide phase was discontinuous, it occupied a large area-fraction of the alloy surface; (b) due to the thickness of the carbides, the X-ray penetration depth was not likely large enough to detect the thinner alumina formed below the carbides. Therefore, electrolytic extraction method was utilized to extract the surface oxide and analyzed. The electrolytic extraction, according to ASTM E963 [42] , is a standard procedure (Pt cathode in 10% HCl–methanol solution) that involves the chemical dissolution of the Ni-matrix leaving a residue of secondary phases; in this case aluminum oxide and carbide phases were separated via filtration. The SEM image of one such extraction residue is shown in Fig. 2 e and f, which depicts the phases formed near the surface of alloy A8 carburized for 50 h. SEM (EDS) and XRD analysis indicated that the Al 2 O 3 internal oxide was the only oxide phase that formed in a thin discontinuous plate morphology, Fig. 2 f. The small, bright colored M 6 C carbides seen in Fig. 2 e can be also recognized in Fig. 2 c, where they form adjacent to the faceted surface carbides. Therefore, the outer layer of carbide islands is followed by a thin discontinuous layer of alumina, which extends into the superalloy as thin platelets due to internal oxidation. The formation of different carbides is strongly dependent on the alloying elements, particularly, Cr, Mo and W. It has been widely reported that while Cr-rich alloys predominantly form carbides of the type M 23 C 6 or M 7 C 3 , in Ni-base alloys, the presence of Mo and W stabilizes M 6 C-type carbide [43–45] . The influence of alloying elements on the formation of the different carbides formed in these alloys is discussed in Section 3.3. The SEM micrographs of the alloy surfaces exposed to the carburizing environment for 225 h are shown in Fig. 4 a–d. Without exception, all the four alloys formed Cr 2 O 3 on the surface at these longer times, albeit non-uniformly. For the most part, the carbides were not detected on the surface at these longer times and wherever the surface Cr 2 O 3 was also absent, either the Al 2 O 3 or the substrate (γ-Ni) surface was exposed. The surface oxide (Cr 2 O 3 ) was mostly faceted and crystalline in appearance (see inset of Fig. 4 b and c), although elongated oxide needles were seen on the surface of alloy A9 ( Fig. 4 d). The oxide formation and subsequent growth has been observed on samples exposed for 100 and 225 h, as shown by the increase in the oxide XRD peak intensities in Fig. 5 a and b. Indeed, visual inspection of the sample coupons from the four alloys exposed to the carburizing environment indicated that the alloys started to form green tinted chromium oxide on the surface at 100 h. 3.3 Gas chromatography analysis: CO consumption/evolution In order to understand the mechanism of carburization, the total CO (gas) consumption/evolution was monitored by a gas chromatograph (GC) during the entire duration of the experiment. Fig. 5 c shows the difference between the amount of CO gas entering and exiting the quartz tubes positioned inside the furnace (ΔCO = CO out –CO in ); the data is normalized and plotted in ppm per sample. Based on the negative value of ΔCO, it can be inferred that all the alloys underwent rapid carburization during the first 50 h of exposure according to, for example, 23Cr + 6C → Cr 23 C 6 . Between 50 and 100 h exposure time, accounting for the GC measurement error in these conditions (for clarity, error bars of ∼5 ppm are indicated for only A2 alloy in Fig. 5 c), the alloys experienced slow carburization. However, beyond 100 h, all the alloys were observed to undergo decarburization through the release of CO and thus exhibited positive ΔCO values. As shown earlier, this release of CO was accompanied by the formation of surface oxide Cr 2 O 3 . The mechanism of CO release and the formation of surface oxide are presented in Section 4. 3.4 Bulk carburization During exposure to the helium gas mixture He + 680 ppm CO + 1.5 ppm CO 2 , all the four alloys underwent carburization, leading to the formation of carbides in the bulk also. The type, morphology and distribution of the carbides formed in the bulk are discussed individually for each alloy and the influence of the alloying elements on the formation and stability of the carbides is presented below. Since the carbides formed in the alloy interior/bulk during the first 25 h were observed for subsequent exposure times, SEM images of microstructures observed at 25 h exposure are only presented. The maximum bulk carbon content of the alloys exposed to the carburizing atmosphere was measured via combustion analysis at Sherry Laboratories (Muncie, IN). It should be noted that the samples were polished before the carbon analysis to remove the surface carbides and oxides, so the carbon content measured is reflective of the bulk carbon in the alloy ‘interior’. In this paper, the term ‘interior’ (carbide) refers to the alloy bulk that includes grain interior and grain boundaries different from the surface. 3.4.1 Alloy A2 Cross-sectional SEM image of alloy A2 exposed to the impure helium atmosphere for 25 h is shown in Fig. 6 a. Nearly all the images were obtained in the back-scattered imaging mode and therefore, the difference in the grey level, particularly, the bright white levels are indicative of high refractory element content (Z-contrast). Typically, W-containing carbides (such as M 6 C) were observed as bright precipitates and Cr-containing carbides appeared light grey in color. After exposure for 25 h, two precipitate phases were observed in alloy A2: lenticular grey colored carbides in the grain interior (GI) and white colored carbides in the form of blocky plates in the grain interior (GI) and grain boundary (GB), Fig. 6 a inset. The grain interior precipitates were typically in the range of ∼0.5–5 μm in length. EMPA and X-ray diffraction analysis indicated that the grey colored carbides in the grain interior were Cr-rich M 7 C 3 carbides ( Fig. 7 a). 2 The XRD data is typically plotted between intensity ( I ) versus 2 θ with I in arbitrary units. However, the strong peaks from the Ni-substrate often overwhelm the weaker peaks from the low density, small-sized precipitate/carbide phases and thin-layered oxide phases. Therefore, the XRD data was normalized in Figs. 3, 5 and 7 , in order to accentuate the carbide/oxide peaks. The XRD data in Figs. 3 and 5 were taken from the surface (face) of the sample whereas the XRD data from Fig. 7 was taken from the cross-section (thickness) of the sample. Since the area sampled was greater in the former case than the latter, the signal-to-noise ratio was lower in the latter case. Therefore, different normalization was used in these two cases (( I / I max ) 1/2 or I / I max ). Since the XRD analysis was only qualitative (i.e., phase identification) and not quantitative, as long as the normalization is same for all the scans within one plot, there is no loss of argument with regards to phase identification. 2 Due to the small precipitate size an accurate measurement of composition with the EMPA was difficult due to considerable matrix effects. The maximum carbon intake in alloy A2 was 0.12 wt.%. 3.4.2 Alloy A6 A6 alloy is richer in Cr (15 wt.%) than other alloys and has the lowest W (5.3 wt.%) and one of the highest Re (7.6 wt.%) content. As expected of a Cr-rich alloy, A6 exhibited only one type of carbide, M 23 C 6 , ( Figs. 6b and 7 b). As will be shown later, this Cr-rich carbide appears dull-white (and not grey) due to high content of refractory element Re in the carbide (presented in Section 4.2). The carbides were observed in the grain boundary as irregular-shaped, elongated and nearly continuous shaped precipitates and in the grain interior as needle-shaped. The grain interior carbides varied in size between 0.5 and 3 μm in length and were seen to precipitate in three distinct orientations: two in-plane and one out-of-plane (thus appearing spherical, see inset in Fig. 6 b). Precipitate free zones (PFZ) were present near the grain boundaries, most likely due to the depletion of Cr during the heterogeneous nucleation and rapid growth of grain boundary Cr-rich carbides. Alloy A6 carburized with a total carbon intake of ∼0.10 wt.%. 3.4.3 Alloys A8 and A9 Alloy A8 has the same amount of Cr and W as alloy A2; however, it was also alloyed with Mo, Co and Re (3 wt.%), with nearly 15 wt.% of Mo + W content compared to only 8 wt.% Mo + W in alloy A6. Alloy A9 contained 12 wt.% Cr and intermediate additions of W (8 wt.%) and Re (6 wt.%) with a total W + Mo addition around 11 wt.%. Carbon analysis indicated a maximum carbon pick up of ∼0.06 wt.% in both A8 and A9 alloys. SEM micrographs ( Fig. 6 c and d) indicated the formation of two different carbide phases: grey colored carbide in the grain boundary and white colored carbides in the grain interior and boundary. The two carbides were formed contiguously in the grain boundary. XRD analysis showed that these phases were Cr-based M 23 C 6 -type carbide and W-rich M 6 C-type carbide, respectively ( Fig. 7 c and d). The Cr 23 C 6 carbides observed in the grain boundary were irregular and discontinuous, consistent with the morphology generally attributed to these carbides [44] . SEM (EDS) scans revealed that the grain interior carbides were enriched in W and Mo (in addition to Ni), whereas the grain boundary carbides were rich in Cr, W, Mo as well as Re. Large precipitate free zones (PFZ) were observed near the grain boundary, thus suggesting the depletion of Cr due to the formation of Cr-rich carbides in the grain boundary. Summarizing the general trends, all four alloys exhibited carbon pickup initially with the formation of both surface carbides and interior carbide(s) with some alloys exhibiting two types of carbides, which were Cr-rich (grey colored) and W-rich (bright colored) phases. With further exposure to the helium gas mixture, the carbides on the alloy surfaces disappeared at the expense of Cr 2 O 3 formation. 4 Discussion 4.1 Stability of carbides: thermodynamic calculations Equilibrium thermodynamic calculations of the carbide phases were conducted for comparison with the experimental observations. Assuming 0.08 wt.% of total carbon in each alloy, phase stability calculations (using the software package PanDat, CompuTherm LLC, Maidson, WI [46] ) based on the alloy compositions in Table 1 indicated that the following stable carbides should form in the alloys: • Alloy A2: M 6 C (800 °C) and M 7 C 3 (1152 °C) • Alloy A6: M 23 C 6 (840 °C) and M 7 C 3 (1249 °C) • Alloy A8: M 23 C 6 (673 °C) and M 6 C (1311 °C) • Alloy A9: M 23 C 6 (752 °C) and M 6 C (1191 °C) It should be noted that these calculations did not include any solubility of rhenium in the chromium carbides, Cr x C y The number indicated in the parenthesis is the upper limit in temperature at which the phase fraction of that particular carbide tends to zero. It can be seen that, based on the composition, each alloy forms one or two type(s) of carbide phases, a low-temperature carbide and a stable high-temperature carbide. The carbides are either Cr-rich carbides such as M 23 C 6 and M 7 C 3 or W-rich M 6 C; no M 3 C 2 or MC type carbides were predicted. Since the carburization experiments were conducted at 1000 °C, it should follow from the above calculations that alloys A2 and A6 should exhibit only M 7 C 3 type carbides and, alloys A8 and A9 should exhibit only M 6 C type carbides in their microstructure. Based on the results presented earlier, alloy A2 formed M 7 C 3 - and probably M 6 C-type carbide. However, alloys A6, A8 and A9 exhibited the low-temperature carbide M 23 C 6 , which is not expected to be present at 1000 °C. The reason for this unexpected stability of M 23 C 6 is most likely due to the higher additions of Re to the alloys, as discussed below. Typically, M 23 C 6 and M 7 C 3 are Cr-rich carbides with the former being more stable than the latter based on from the free energy of formation of the Cr-carbides [47] , whereas M 6 C typically forms when the Mo and/or W content is higher than 6–8 at.% [43] . The M 6 C is typically (Ni, Co) 3 Mo 3 C and (Ni, Co) 2 W 4 C, although wider range in composition are noted in some alloys [44,45] . The M 6 C carbides are known to be beneficial as grain boundary precipitates to control grain size in wrought alloy processing [44] . Fig. 7 e shows the morphology and distribution of the internal grain boundary carbides formed in alloy A8 after 50 h of carburization; the sample was electrolytically etched to reveal the grain boundary precipitates [42] . The Cr-rich (grey) and the W-rich (bright) carbides formed adjacent to each other i.e., in a contiguous manner. It has been suggested that continuous and/or denuded M 23 C 6 and Widmanstätten M 6 C or cellular, discontinuous grain boundary M 23 C 6 are to be avoided for best ductility and rupture life [44,45] . Therefore, the contiguous formation of the two carbides observed in this study is likely to be detrimental to the material ductility. Both M 23 C 6 and M 6 C carbides have a complex cubic structure, and in the presence of Mo or W, the former has a composition close to Cr 21 (Mo, W) 2 C 6 . M 7 C 3 is not widely observed in superalloys, but Nimonic 80A (Ni–20Cr–3Fe based alloy) is one example where it does form [44,48] . Prior studies [42] suggest that while M 6 C is an intermediate/high-temperature carbide (900–1050 °C), M 23 C 6 and M 7 C 3 are lower temperature carbides. However, in the present case, due to significant additions of Mo, Re and W, the carbides contained a high content of these refractory elements, as shown in Fig. 8 . Therefore, the temperature range of stability of the three carbides depends strongly on their chemical composition. In particular, while solubility of Mo and W is assumed in all these carbides, the effect of Re is not explicitly addressed; this is important in the current case due to high additions of Re (3–7.6 wt.%). The effect of Re on the carbide stability is presented below. 4.2 Effect of Re on chromium carbides The solubility of W, Re and Mo in the carbides has been verified using EMPA analysis. As shown in Fig. 8 a–c, the line-scans near the grain boundary carbides of alloys A6, A8 and A9 exhibit high Re solubility in Cr-rich phases. For example, in Fig. 8 a, the grain boundary (GB) M 23 C 6 carbides formed in A6 alloys after 100 h exposure show high Re and low W and Mo content. In Fig. 8 b, the grain boundary is seen to contain two types of carbides, namely, Cr-rich carbides enriched by Re and W-rich carbides enriched by Mo. The former is M 23 C 6 and the latter is likely to be M 6 C. It is not yet clear if the M 6 C carbide allows for any Re solubility. Similar enrichment by Re was also confirmed in A8 and A9 alloys that also exhibited M 23 C 6 in addition to M 6 C despite high W and Mo content in the alloy. The Calphad models used in the thermodynamic calculations referred in the previous section do not account for any solid solubility of Re in chromium carbides Cr x C y [46] . However, investigations on the Cr-(d-block element)-C ternary systems, particularly the Cr–Re–C system, indicate that the maximum solubility of Re in chromium carbides is 19 at.% (at 1675 °C) in Cr 23 C 6 , 6 at.% (at 1640 °C) in Cr 7 C 3 , and 4 at.% (at 1780 °C) in Cr 3 C 2 [49–52] . Using the isothermal data for the Cr–Re–C ternary at 1300 °C [49] and extrapolating to 1000 °C using Calphad methods leads to the ternary diagram shown in Fig. 8 d. The high solubility of Re, clearly evident at 1000 °C, is expected to increase the stability and hence the solvus temperatures of the carbides, particularly Cr 23 C 6 . This could explain the existence of M 23 C 6 carbides at higher temperatures in the alloys A6, A8 and A9. 4.3 Stability diagram In the current work, since only CO and CO 2 are used as impurities, oxidation and/or carburization of the alloys can occur. For a high CO content in the gas mixture, the activity of carbon in the helium gas environment increases and therefore, tends to be more carburizing. The extent of carburization of a given alloy depends on a number of factors, such as: (a) carbon diffusion through the alloy, (b) carbide forming elements in the alloy, (c) stability of the carbides and (d) type, nature and thickness of a protective oxide scale which is dependent on both the oxidation potential of the environment as well as the alloying elements. Typically, a stability diagram with activities of carbon and oxygen as axes is used to study the stability of metal/oxide/carbide phases [10,53] . The stability diagram, representing the thermodynamic equilibrium between the alloy and the surrounding gaseous environment, is shown in Fig. 9 a for Cr/Cr 2 O 3 /Cr 23 C 6 (say, for alloy Inconel 617 that forms predominantly Cr 23 C 6 and is a chromia (Cr 2 O 3 ) former) at 1000 °C. The phase boundaries are given by the following equilibrium reactions: • a C ∗ : Cr/Cr 23 C 6 boundary: Cr 23 C 6 ↔ 23Cr + 6C Reaction 1 • P O 2 ∗ : Cr/Cr 2 O 3 boundary: 2Cr 2 O 3 ↔ 4Cr + 3O 2 Reaction 2 • Cr 23 C 6 /Cr 2 O 3 boundary: Cr 23 C 6 + 69O 2 ↔ 46Cr 2 O 3 + 24C Reaction 3 • P CO ∗ : Cr/Cr 2 O 3 /Cr 23 C 6 boundary: 2Cr 2 O 3 + Cr 23 C 6 ↔ 27Cr + 6CO Reaction 4 A fuller description of the stability diagram and the relevant applications to study corrosion and stability in impure helium gas environment are given elsewhere [30,32,33,53] . Based on the activities of carbon and oxygen in the helium gas environment and the type of the phases observed, the stability diagram in Fig. 9 a predicts whether the alloy will undergo decarburization/carburization/oxidation. It should be noted that these are strictly equilibrium considerations and in actual operating environments the reactions need not be homogeneous [30] . In the stability diagram shown in Fig. 9 a, two environments marked as B and A correspond to two different helium gas mixtures used in this study and in a related study on decarburization [6] , respectively. The former is a gas mixture containing He + 680 ppm CO + 1.4 ppm CO 2 used in this study and the latter is He + 14 ppm CO + 1.4 ppm CO 2 [6] . Based on the above discussion, environment A should be decarburizing while environment B should be carburizing [54] . A similar plot is shown in Fig. 9 b by considering metal (Cr)/oxide (Cr 2 O 3 )/carbides (Cr x C y ) equilibria based on the stability of the carbides and oxide (i.e., free energies of the phases) [29,47] . For the environment B, the stability diagram in Fig. 9 b predicts that the alloys studied in the current work should undergo carburization and form M 6 C [6] , Cr 23 C 6 and Cr 7 C 3 but not Cr 3 C 2 since the carbon activity in the gas is not high enough, i.e., a C (gas) < a C ∗ (Cr 3 C 2 ). This was indeed observed, as presented in the previous section. However, the use of such stability diagram is not straightforward, especially for multicomponent alloys that tend to form carbides with a wide range of composition. It has been shown elsewhere that in order to study the carburization/decarburization process accurately, the stability diagrams need to consider these composition changes and account for the (phase) formation-energy variations as a function of carbide chemistry [6,30] . This is due to the dependence of the phase boundaries in the stability diagram on the formation energies of the phases involved. While the free energy data is available for carbides such as Cr x C y , the published literature does not list any mixed carbide free energy values, particularly for the refractory element additions. Therefore, these stability diagrams should be used in a qualitative sense only. Notwithstanding, the stability diagram does show the relative stability of phases as M 23 C 6 > M 7 C 3 > M 3 C 2 (decreasing order of stability), with M 6 C being most stable as argued in [6] . 4.4 Mechanism of carburization Based on the results presented above, the mechanism of carburization for the alloys considered in this work is proposed as follows: 4.4.1 Initial carburization The carbonaceous gases set up the carbon potential ( a C (gas)) in the environment at 1000 °C, as explained in Section 4.3. The driving force for the carbon transfer between the gas and the alloy may be written as Δ G = RT ln( a C (gas)/ a C (alloy)), where a C (gas) and a C (alloy) are the carbon activities in the gas and alloy, respectively. Since the alloys were initially carbon-free with a C (alloy) < a C (gas), carbon transfer occurred from the gas to the alloys, thus carburizing them. This is also confirmed by the consumption of CO gas according to Fig. 5 c. Depending on the alloy composition, as well as the carbon activity levels, several carbides formed on the surface. Particularly, since the carbon activity in the environment was greater than a C ∗ (Cr 23 C 6 ), a C ∗ (Cr 7 C 3 ) and a C ∗ (M 6 C), these carbides formed on the alloy surfaces. As the carbon activity in the helium gas mixture is less than 1, a continuous scale did not form on the surface, instead, carbon dissolution at the alloy surface and inward diffusion occurred [55] . Since the carbides are less stable than the oxides (Al 2 O 3 and Cr 2 O 3 ), and since the dissociation pressure of the oxides (10 −35 atm and 10 −22 atm, respectively) is lower than the partial pressure of the oxygen in the experiment (10 −19 to 10 −20 atm), they (oxides) are also expected to form at 1000 °C. However, in the present case, only Al 2 O 3 was observed as internal oxide precipitates during 50 h of exposure (Section 3.2). Even though the stability diagram in Fig. 9 predicts Cr 2 O 3 formation, Al 2 O 3 is the only oxide during early stages of exposure. In addition to the surface carbides, the carbon diffusion through the alloy led to the formation of internal carbides. Since the carbon diffusion kinetics are comparatively rapid than the oxidation kinetics, the carbides may be expected to precipitate very early during the carburization; indeed the CO consumption (ΔCO in Fig. 5 c) was relatively high during the first 10 h of carburization. Due to faster diffusion of carbon in grain boundaries and subsequent heterogeneous nucleation of carbides, it can be expected that the carbides first formed near the grain boundary and rapidly coarsened compared to the grain interior. In fact, it has been commonly observed that some chromia forming alloys when exposed to certain gas compositions do not form chromia scale and exhibit internal chromium carbide precipitation rather than external oxide scale formation [55] . Considering the diffusion coefficient of carbon in Ni-alloy at 1000 °C is ∼1.4 × 10 −11 m 2 /s [56] , the time required for the carbon to diffuse through the sample half-thickness ( d = 1.2 mm) may be estimated x = 4(Dt) 1/2 , and was calculated as being less than 1 h. Therefore, once the carbon solid-solubility is exceeded, the carbides may be expected to precipitate very early during the carburization, probably within the first few hours of exposure. While Cr-rich alloys formed Cr-rich carbides such as Cr 23 C 6 and Cr 7 C 3 , the W and Mo rich Ni alloys formed M 6 C [43] . An earlier study evaluated the balance between Cr and W in a Ni–Cr–W alloy system that is required to form M 23 C 6 or M 6 C carbides; for an alloy with 12 wt.% (or 15 wt.%) Cr at least 11 wt.% (or 13.5 wt.%) W is necessary to form M 6 C carbides in the alloy. However, an additional element that was seen to influence the stability of the Cr-carbides, especially Cr 23 C 6 , was found to be Re due to its high solubility in the carbide. Therefore, in order to form M 6 C carbides, higher additions of W (∼15 wt.% or higher) are probably warranted. Since it has been shown that M 6 C carbide is more beneficial as grain boundary precipitate in order to control grain size in wrought alloy processing [44] and is also more stable compared to the chromium carbides [6,30] , combined with its potent solid solution strengthening [57,58] , higher W additions (12–18 wt.%) is likely to be more beneficial. 4.4.2 Oxidation and formation of Cr 2 O 3 Referring to the stability diagram in Fig. 9 a and b, it can be seen that the carburizing environment (B) actually lies in the region identified as the ‘oxidation and slow carburization where Cr 2 O 3 is the stable phase. This signifies that the only stable phase should be Cr 2 O 3 at the surface. Based on the observations reported in Section 3.2 (see also Fig. 4 ) since the Cr 2 O 3 begins to form and grow after 100 h of exposure time along with the disappearance of the surface carbide phase, the carbides are a transient phase. Furthermore, concomitant with the oxide formation, release of CO gas was also observed (positive ΔCO in Fig. 5 c); thus it can be inferred that the surface carbides oxidized, for example, according to the reaction Cr 23 C 6 + 69O 2 ↔ 46Cr 2 O 3 + 24C. The carbon product most likely combined with the oxygen to form excess CO and detected by the gas chromatograph, as shown in Fig. 5 for times greater than 100 h. Thus, the surface carbide is a metastable phase since the stable Cr 2 O 3 is formed after prolonged exposure. In contrast, for alloys containing higher Cr content (for example, Inconel 617 with 22 wt.% Cr), the Cr 2 O 3 phase is generally observed to develop along with the carbides on the surface, with the carbides eventually disappearing at the expense of Cr 2 O 3 growth [54] . Therefore, the Cr content of the alloy not only influences the mechanism of carbide formation but also the surface oxide. Since Al 2 O 3 is known to be an excellent diffusion barrier against diffusion of C (due to negligible solubility of the latter [59] ), both external surface carburization and internal carburization may be prevented by the formation of a slow growing alpha-alumina obtained through the use of well-known MCrAlY (M = Ni, Fe or Co)-type coatings. 5 Conclusions The surface and microstructure stability of four experimental W- and Re-rich Ni-base alloys has been studied in an impure helium environment containing only CO and CO 2 impurities (He + 680 ppm CO + 1.4 ppm CO 2 ) for 225 h exposure time; the alloys were initially carbon free. Based on the observations, the following conclusions are made: (1) All the alloys were carburized with a maximum carbon pickup between 0.06 and 0.12 wt.% (2) During the first 50 h exposure, carbides were observed on the alloy surface as well as in the bulk with carbides precipitating in the grain interior and on the grain boundary. (3) Depending on the alloy composition, carbides of type M 6 C, M 7 C 3 or M 23 C 6 were observed. (4) Alloys with high W content exhibited M 6 C type carbides, whereas high Cr and low W alloys formed Cr-rich M 23 C 6 carbides. High additions of Re stabilized the M 23 C 6 phase due to its high solubility in these chromium-rich carbides. (5) The surface carbides oxidized after prolonged exposure forming stable Cr 2 O 3 oxide on the alloy surface. Acknowledgements The authors acknowledge the support of U.S. Department of Energy under contract #DE-FC07-05ID14660. They authors are also thankful for the assistance provided by Christopher Torbet with the experimental set-up. References [1] A Technology Roadmap for Generation IV Nuclear Energy Systems, US DOE Nuclear Energy Research Advisory Committee and the Generation IV International Forum, Institution, (2002). [2] E.A. Harvego, Evaluation of next generation nuclear power plant (NGNP) intermediate heat exchanger (IHX) operation conditions, Idaho National Laboratory, INL/EXT-06-11109, (2006). [3] G.O. Hayner, R.L. Bratton, R.E. Mizia, W.E. Windes, Next generation nuclear plant materials research and development program plan, Idaho National Laboratory, INL/EXT-06-11701, (2006). [4] R.N. Wright, Summary of studies of aging and environmental effects on Inconel 617 and Haynes 230, Idaho National Laboratory, INL/EXT-06-11750, (2006). [5] R.N. Wright, Kinetics of gas reactions and environmental degradation in NGNP helium, Idaho National Laboratory, INL/EXT-06-11494, (2006). [6] R.R. Adharapurapu, D. Kumar, J. Zhu, C. Torbet, G. Was, T.M. Pollock, High-temperature surface stability of W-rich Ni-based alloys in impure helium, Accepted by Metall. Trans. A. (2010). [7] H. Nickel F. Schubert H. Schuster Evaluation of alloys for advanced high-temperature reactor systems Nucl. Eng. Des. 78 1984 251 265 [8] H.G.A. Bates The corrosion behavior of high-temperature alloys during exposure for times up to 10000h in prototype nuclear process helium at 700 to 900 °C Nucl. Technol. 66 1984 415 428 [9] C. Cabet A. Terlain P. Lett L. Guétaz J.-M. Gentzbittel High temperature corrosion of structural materials under gas-cooled reactor helium Mater. Corros. 57 2006 147 153 [10] H.J. Christ U. Kunecke K. Meyer H.G. Sockel Mechanisms of high-temperature corrosion in helium containing small amounts of impurities. II: Corrosion of nickel-base alloy Inconel 617 Oxid. Met. 30 1988 27 51 [11] L.W. Graham Corrosion of metallic materials in HTR-helium environments J. Nucl. Mater. 171 1990 76 83 [12] T. Hirano H. Araki H. Yoshida Carburization and decarburization of superalloys in the simulated HTGR helium J. Nucl. Mater. 97 1981 272 280 [13] H.M. Yun P.J. Ennis H. Nickel H. Schuster The effect of high temperature reactor primary circuit helium on the formation and propagation of surface cracks in Alloy 800H and Inconel 617 J. Nucl. Mater. 125 1984 258 272 [14] F. Rouillard C. Cabet K. Wolski M. Pijolat Oxide-layer formation and stability on a nickel-base alloy in impure helium at high temperature Oxid. Met. 68 2007 133 148 [15] F. Rouillard C. Cabet K. Wolski A. Terlain M. Tabarant M. Pijolat F. Valdivieso High temperature corrosion of a nickel base alloy by helium impurities J. Nucl. Mater. 362 2007 248 252 [16] R. Tanaka T. Kondo Research and development on heat-resistance alloys for nuclear process heating in Japan Nucl. Technol. 66 1984 75 87 [17] T. Matsuo, M. Kikuchi, M. Takeyama, Strengthening mechanisms of Ni–Cr–W based superalloys for very high temperature gas cooled reactors, in: Heat-Resistance Materials, Proceedings of the First International Conference. Fontana, Wisconsin, USA, (1991), pp. 601–614. [18] T. Matsuo M. Ueki M. Takeyama R. Tanaka Strengthening of nickel-base superalloys for nuclear heat exchanger applications J. Mater. Sci. 22 1987 1901 1907 [19] Y. Muto H. Nakajima M. Eto Development of high temperature structural materials for the HTGR Nucl. Eng. Des. 144 1993 305 315 [20] I. Mutoh Y. Nakasone K. Hiraga T. Tanabe Corrosion behavior of Ni-base superalloys at 1373 K in simulated HTGR impure helium gas environment J. Nucl. Mater. 207 1993 212 220 [21] Y. Shida H. Fujikawa Yoshiatsu Sawaragi The oxidation and carbon transfer behavior of Ni-27Cr-5Mo-5W based alloys in an impure helium atmosphere at high temperature Corros. Sci. 34 1993 1157 1171 [22] M. Shindo J. Nakajima Carburization behavior of high temperature alloys in carburizing environment J. Nucl. Mater. 166 1989 278 286 [23] B.H. Kear D.P. Pope Role of refractory elements in strengthening of g and g’ precipitation hardened nickel-base superalloys Refractory Alloying Elements in Superalloys 1984 ASM Metals Park, Ohio 135 151 [24] F.R.N. Nabarro The superiority of superalloys Mater. Sci. Eng. A 184 1994 167 171 [25] T.M. Pollock R.D. Field Dislocations and high-temperature deformation of superalloy single crystals Dislocations in Solids 2002 Elsevier Science 547 618 [26] T.M. Pollock S. Tin Nickel-based superalloys for advanced turbine engines: chemistry, microstructure and properties J. Propul. Power. 22 2006 361 374 [27] C.L. Fu R. Reed A. Janotti M. Krcmar On the diffusion of alloying elements in the nickel-base superalloys K.A. Green T.M. Pollock H. Harada T.E. Howson R.C. Reed J.J. Schirra S. Walston Superalloys 2004 Pennsylvania Seven Springs: TMS, Champion 867 876 [28] M.S.A. Karunaratne R.C. Reed Interdiffusion of the platinum-group metals in nickel at elevated temperatures Acta Mater. 51 2003 2905 2919 [29] H.J. Christ D. Schwanke T. Uihlein H.G. Sockel Mechanisms of high-temperature corrosion in helium containing small amounts of impurities. I: Theoretical and experimental characterization of the gas phase Oxid. Met. 30 1988 1 26 [30] P. Combrade, D. Kaczorowski, Review of the gas/Ni-base alloys interactions in HTR impure helium, FRAMATOME ANP, TFCCR 02-1214, (2003) 1–26. [31] K. Natesan, A. Purohit, S.W. Tam, Materials behavior in HTGR environments, Argonne National Laboratory, NUREG/CR-6824, ANL-02/37, (2003) 1–69. [32] W.J. Quadakkers H. Schuster Thermodynamic and kinetic aspects of the corrosion of high-temperature alloys in high-temperature gas-cooled reactor helium Nucl. Technol. 66 1984 383 391 [33] W.J. Quadakkers H. Schuster Corrosion of high temperature alloys in the primary circuit helium of high temperature gas cooled reactors. Part I: Theoretical background Mater. Corros. 36 1985 141 150 [34] D. Kumar, G. Was, Mechanism of decarburization of alloy 617 at 1000 °C in helium containing CO and CO 2 as impurities, in: C.C. Fu, A. Kimura, M. Samaras, M.S.d. Caro, R.E. Stoller (Eds.), Materials for Future Fusion and Fission Technologies. MRS Symposium Proceedings, Warrendale, PA, 2009, 1125-R06-02. [35] M.R. Warren Rapid decarburization and carburization in high temperature alloys in impure helium environments High Temp. Technol. 4 1986 119 130 [36] D. Kumar C.J. Torbet G.S. Was A facility for conducting high temperature oxidation experiments of alloys in helium containing part per million levels of impurities Meas. Sci. Technol. 20 2009 095708 095718 [37] I.M. Allam Z.M. Gasem High temperature corrosion of alloys Haynes 556 in carburizing/oxidizing environments Mater. Corros. 58 2007 245 253 [38] P. Becker D.J. Young Carburization resistance of nickel-base, heat-resisting alloys Oxid. Met. 67 2007 267 277 [39] G.Y. Lai Carburization and metal dusting High-temperature Corrosion of Engineering Alloys 1990 ASM International 97 146 [40] H.M. Tawancy N.M. Abbas Mechanism of carburization of high-temperature alloys J. Mater. Sci. 27 1992 1061 1069 [41] C.S. Giggins F.S. Pettit Oxidation of Ni–Cr–Al alloys between 1000 °C and 1200 °C J. Electrochem. Soc. 118 1971 1782 1790 [42] “Standard practice for electrolytic extraction of phases from Ni and Ni–Fe base superalloys using a hydrochloric-methanol electrolyte”, ASTM-E963, (1995), ASTM International, PA. [43] H.E. Collins Relative stability of carbide and intermetallic phases in nickel-base superalloys Superalloys 1968 ASM Metals Park, OH 171 198 [44] M.J. Donachie Superalloys: A Technical Guide 2002 ASM International [45] C.T. Sims N.S. Stoloff W.C. Hagel Superalloys II 1987 Wiley-Interscience [46] S.-L. Chen S. Daniel F. Zhang Y.A. Chang X.-Y. Yan F.-Y. Xie R. Schmid-Fetzer W.A. Oates The PANDAT software package and its applications Calphad 26 2002 175 188 [47] S.R. Shatynski The thermochemistry of transition metal carbides Oxid. Met. 13 1979 105 118 [48] W.E. Voice R.G. Faulkner Carbide stability in Nimonic 80A alloy Met. Trans. A 16 1985 511 520 [49] L.V. Gorshkova T.F. Fedorov Y.B. Kuz’ma The rhenium–chromium–carbon system Powder Metall. Met. Ceram. 5 1966 231 233 [50] A.A. Bondar T.Y. Velikanova Aspects of construction of the constitution diagrams of ternary systems formed by chromium with carbon and d-transition metals Powder Metall. Met. Ceram. 35 1996 484 496 [51] A.V. Grytsiv A.A. Bondar T.Y. Velikanova Rhenium solid solution in the Cr–Re–C ternary system at solidus temperature J. Alloys Compd. 14 1997 402 405 [52] T.Y. Velikanova A.A. Bondar A.V. Grytsiv O.I. Dovbenko Metallochemistry of chromium in ternary systems formed by chromium with d-metals and carbon J. Alloys Compd. 320 2001 341 352 [53] W.J. Quadakkers Corrosion of high temperature alloys in the primary circuit helium of high temperature gas cooled reactors. Part II: Experimental results Mater. Corros. 36 1985 335 347 [54] D. Kumar, Mechanism of decarburization and carburization of alloy 617 at 1000°C in helium containing CO and CO 2 Ph.D. Dissertation, Materials Science and Engineering, University of Michigan, Ann Arbor (2010). [55] D. Young Corrosion by carbon High Temperature Oxidation and Corrosion of Metals 2008 Elsevier London 398 450 [56] J. Cermak H. Mehrer Tracer diffusion of 14C in austenitic Ni–Fe–Cr alloys Acta Metall. Mater. 42 1994 1345 1350 [57] Y. Mishima S. Ochiai N. Hamao M. Yodogawa T. Suzuki Solid solution hardening of nickel – role of transition metal and B-subgroup solutes Trans. Jpn. Inst. Met. 27 1986 656 664 [58] H.A. Roth C.L. Davis R.C. Thomson Modeling solid solution strengthening in nickel alloys Metall. Mater. Trans. A 28 1997 1329 1335 [59] I. Wolf H.J. Grabke A study on the solubility and distribution of carbon in oxides Solid State Commun. 54 1985 5 10
更多查看译文
关键词
A. Superalloys,C. Carburization,C. Oxidation
AI 理解论文
溯源树
样例
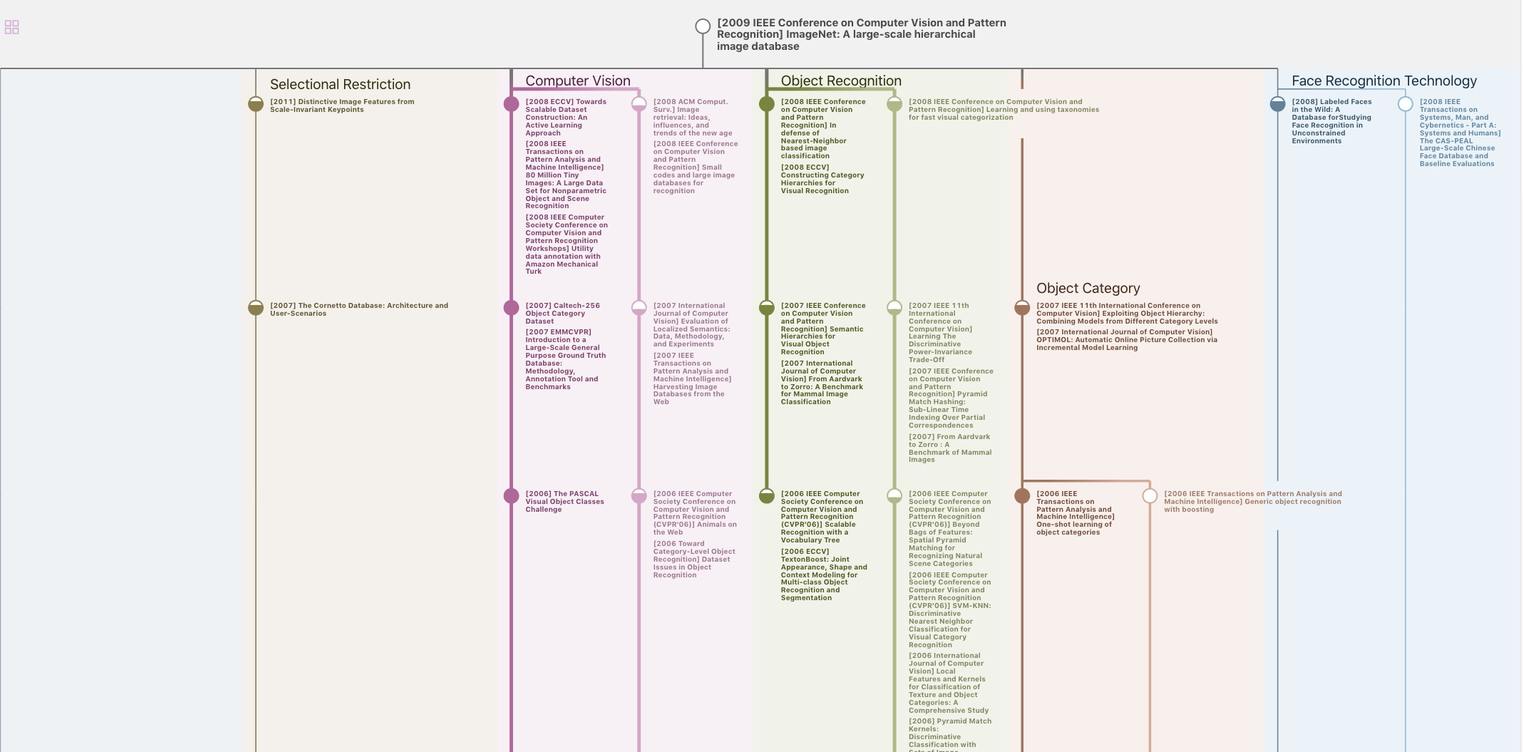
生成溯源树,研究论文发展脉络
Chat Paper
正在生成论文摘要