Fabrication of a quadrant-type accelerator structure for clic
msra(2008)
摘要
A study was done on the fabrication of the quadrant for the X-band accelerator structure of CLIC. By using a ready-made multi-axis milling machine and carbide tools, we typically reached an error level of 5 microns. The typical local profile shape was controlled within a tolerance, ± a few microns, but the absolute positioning of the shape should still be improved by several micron level to address the four rod fabrication for a structure. BACKGROUND OF THE STUDY KEK has long been developing the X-band high gradient accelerator technology for the electron-positron linear collider, NLC/GLC[1]. After the recommendation of cold technology in 2004 by the international technology recommendation panel[2], ITRP, the X-band activity at KEK has focused on some basic studies[3]. In the end of 2006, the CLIC[4] re-optimized its design and reached the choice of the frequency from 30 GHz to 12 GHz and the gradient of 150 MV/m to 100 MV/m[5]. This choice is very close to the design of the X-band technology KEK has been working on. Therefore, X-band group of KEK decided to collaborate with CERN on the CLIC acceleration technology. One of the special CLIC accelerator designs is the choice of the quadrant as a constituent of the accelerator structures. This choice makes various pros and cons; considering these, we decided to address the quadrant fabrication study as one of our basic research activities. Some of the studies were presented by T. Takatomi[6]. An excellent result was also presented by R. Zoetewey[7], though we proceeded independently and no feedback from the discussion. STRATEGY OF THE STUDY Since the fabrication of a quadrant was new to KEK, we set three stages. As the first stage, short (~10 cm) models with three cells in the middle were made by five different vendors. Taking the experience of this stage into account but basically succeeding the same machine and same tool, a full quadrant was made as the second stage. From these study, we estimate the feasibility of the structure fabrication as the last stage. In the present paper are mainly described the study results of the second stage. RESULT OBTAINED IN SHORT MODELS The 3D shape was formed by taking the 3D CAD file in stp format. This file was modified by KEK with taking the last three cells.
更多查看译文
AI 理解论文
溯源树
样例
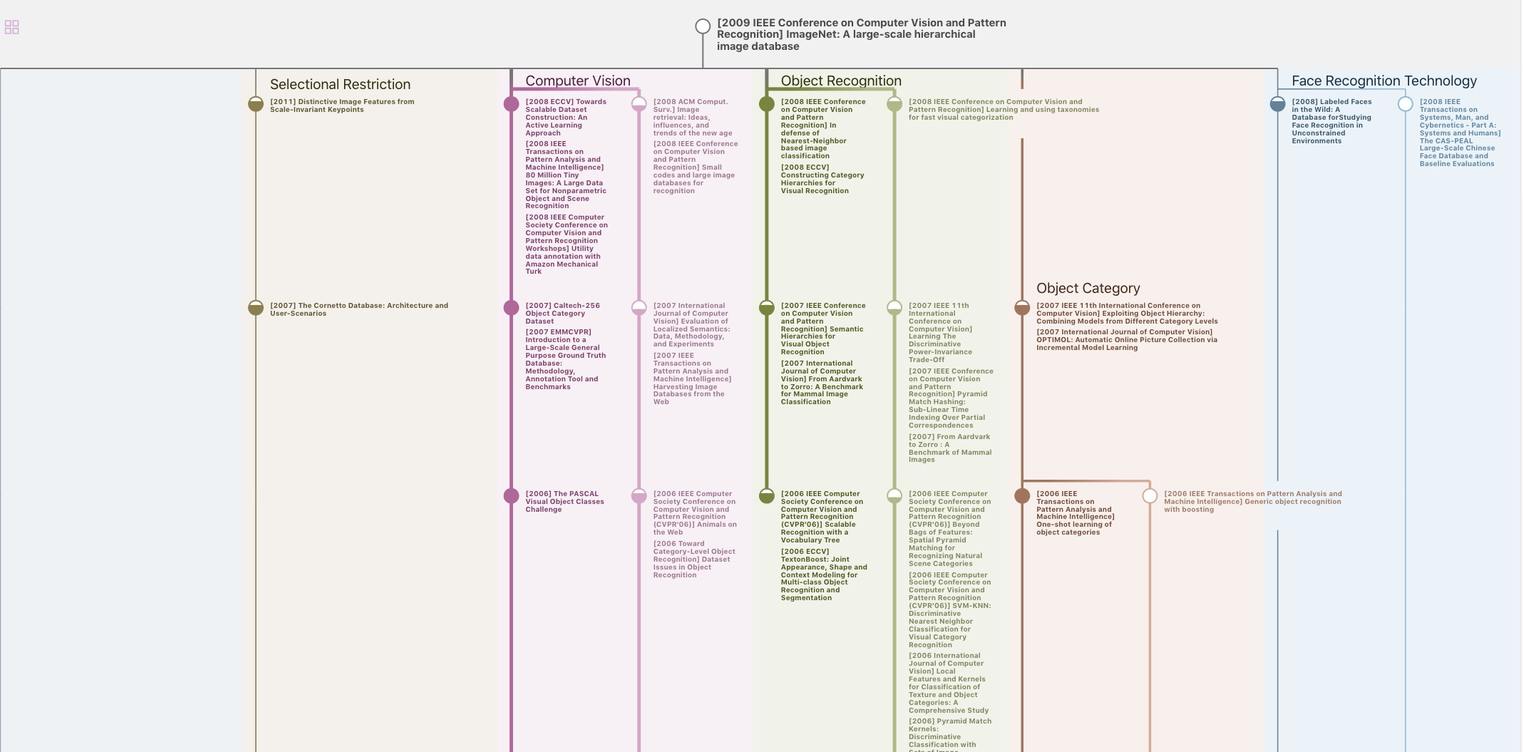
生成溯源树,研究论文发展脉络
Chat Paper
正在生成论文摘要