A qualitative comparison of stresses at aircraft bolted joint holes under initial clamping force
Procedia Engineering(2011)
摘要
The stress state around the middle (skin) plate hole of double-lap single bolted joints are investigated under an initial clamping force. Two different materials are considered for the middle plate: a quasi-isotropic carbon fiber reinforced plastic (CFRP) composite laminate and an aluminum alloy 7075-T6 plate. The outer (splice) plates are aluminum alloy 7075-T6 for both cases. The noncommercial FE code ANSYS vl2.0 is used for the analyses [1]. Linear solid brick elements are used to model the aluminum plates and the composite laminate. One element per layer approach is employed in through-the-thickness direction to model the laminated composite plate. The bolt and the washer are modeled as a single linear elastic deformable solid body. Surface-to-surface contact elements are used to define the contact behavior between the joint members including the effect of friction. Comparison of the stress results show that the clamping force has a significantly different effect for composite and aluminum plates. Initial clamping force introduces beneficial compressive stresses for aluminum plate whereas both tensile and compressive stresses occur for the composite laminate. The stress analysis results are used to explain the phenomena behind the different clamping force responses.
更多查看译文
关键词
Bolted joints,clamping force,composite materials,finite element analysis
AI 理解论文
溯源树
样例
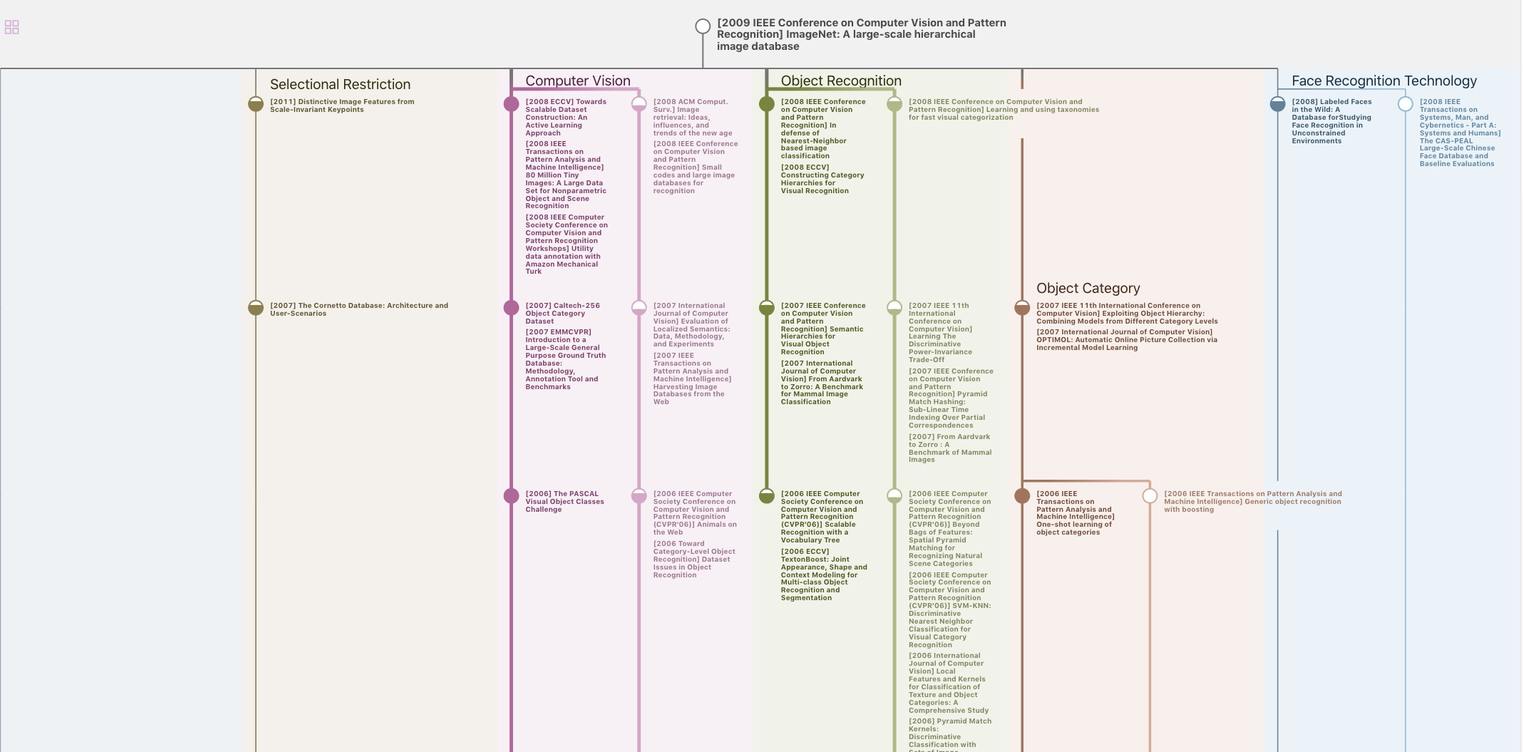
生成溯源树,研究论文发展脉络
Chat Paper
正在生成论文摘要