Strategy for the Simulation of the ITER Toroidal Field Coil Case Welding Distortion with Finite-Element Method
IEEE TRANSACTIONS ON APPLIED SUPERCONDUCTIVITY(2018)
Key words
ITER,magnets,stainless steel welding,finite element method (FEM) simulation
AI Read Science
Must-Reading Tree
Example
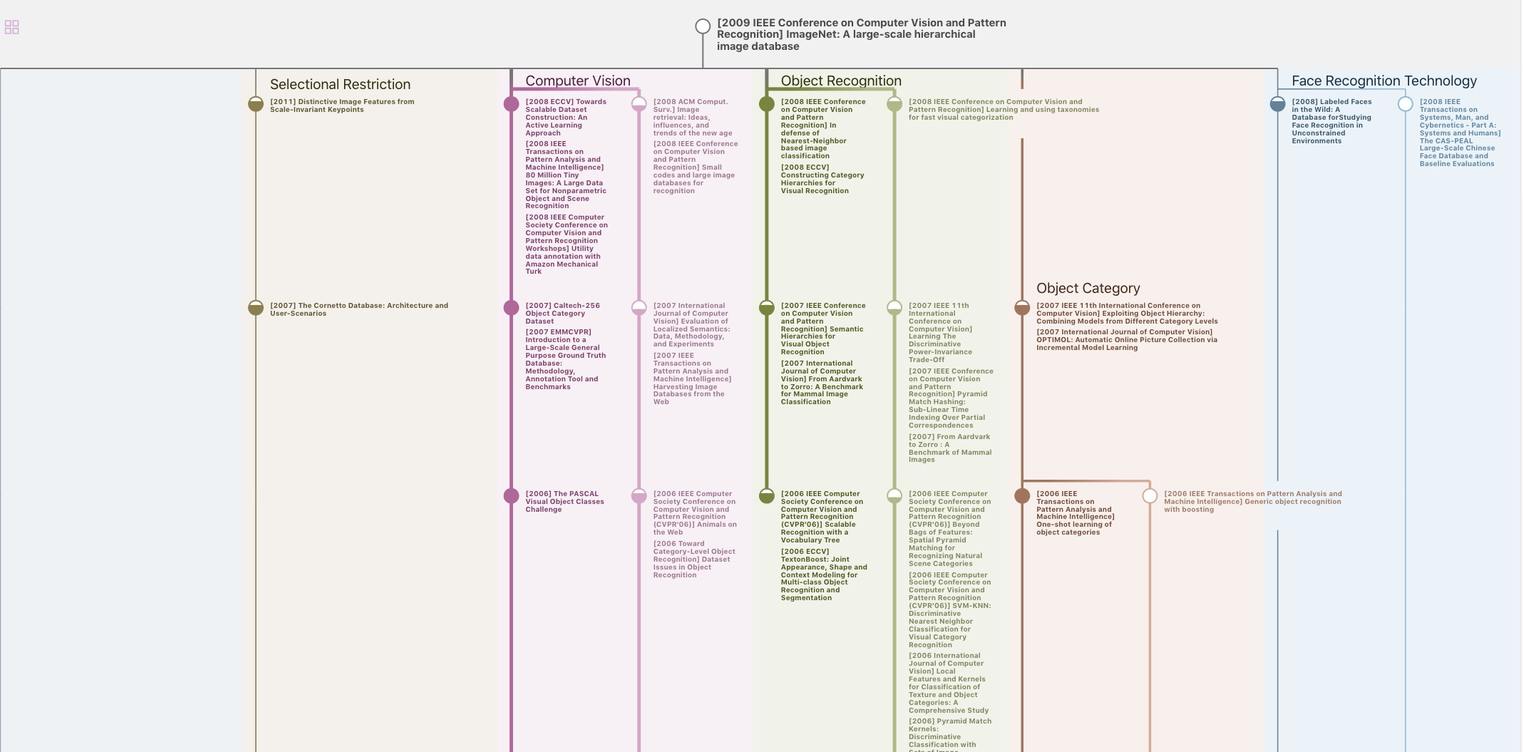
Generate MRT to find the research sequence of this paper
Chat Paper
Summary is being generated by the instructions you defined